Injection molding discoloration is a variation from the plastic’s base color. Overheating, contamination, and faulty production could all contribute to this faulty component.
The degree to which a flaw in the part’s coloring due to thermal degradation is evident varies with the severity of the degradation. To avoid this problem, it’s important to have a firm grasp of the factors that can lead to injection molding discoloration during the plastic injection molding process. An example of a discolored product can be seen below.
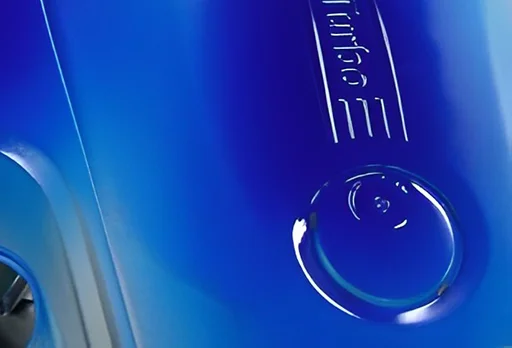
Now, let’s go ahead and dive deeper into the analysis, impact, and solutions of discoloration in injection molded parts.
Also Read: 6 Common Challenges Faced by CNC Manufacturing Companies
Impact of Discoloration on Plastic Parts:
The discoloration of plastic parts can have consequences for both the part’s appearance and function. Let’s study these consequences in more detail:
Product Aesthetics:
Plastic components that have been discolored can have a considerable adverse effect on the overall aesthetic appeal of the finished product. The appearance of the product being unpleasant, inconsistent, or even defective might be caused by streaks, stains, or an uneven distribution of color.
This can result in dissatisfied customers, an unfavorable view of the brand, and a loss of sales. Discoloration of plastic parts should be avoided at all costs, but this is especially true in industries like consumer electronics and automobiles, where appearance is paramount. This can lead to huge financial losses.
Product Performance:
Plastic components can also have their functional characteristics altered if they become discolored. The injection molding material may become weaker as a result of thermal degradation or chemical reactions that take place during the molding process. This results in a decrease in the material’s structural strength and mechanical strength. A good example of an impacted product due to injection molding discoloration.
A decrease in the coloration of a part can indicate a decrease in its resistance to impact, a decrease in its dimensional correctness, or a decrease in its resistance to chemicals. These functional flaws can potentially jeopardize the finished product’s performance and reliability, which may result in risks to users’ safety or the failure of the product itself.
Causes and Solutions of Discoloration in Injection Molded Parts:
Discoloration Due to Machining Issues:
Problem | Problem Scenario | Solutions |
1. Excessive Short Shot Ratio | Excessive shot size ratio in plastic injection molding can cause discoloration in the molded parts. It increases shear stress, heat buildup, and prolonged exposure to high temperatures, resulting in material degradation and color changes. Additionally, overpacking the mold cavity due to an oversized shot can lead to uneven filling, inadequate cooling, and inconsistent material distribution, causing variations and streaks in color. | To solve this, a shot-to-barrel ratio of 50 percent should be your goal. This is the best-case scenario, but it can be as low as 20% if the material is not particularly heat sensitive (like polypropylene), and it can be as high as 80% if the material is extremely heat sensitive (like PVC). Emptying the barrel before each shot is ill-advised since doing so would prolong the time needed to heat the subsequent material to the correct temperature, potentially compromising the material’s quality. |
2. Excessive Residence Time | This refers to the duration that plastic material remains in the heated barrel of an injection molding machine. It can contribute to plastic part discoloration of plastic parts. When the residence time exceeds the recommended limits, the plastic undergoes prolonged exposure to high temperatures, leading to thermal degradation. This degradation can cause changes in the material’s molecular structure, resulting in discoloration or yellowing. | If possible, the mold should be designed to be run in a press with an injection shot size equal to half a barrel. Minimize the material’s time in the heated barrel by optimizing the machine’s cycle and removing potential bottlenecks. |
3. High Barrel Temperature | This issue can contribute to plastic part discoloration when the barrel temperature is set too high. It can cause the plastic material to overheat, leading to thermal degradation. This degradation alters the chemical structure of the plastic, resulting in discoloration or yellowing of the finished parts. | To solve this issue, you need to reduce the temperature of the barrel to the range advised by the material supplier. Assemble the profile so the material heats up gradually from the back to the front of the barrel. |
4. Hot Nozzle Temperature Tool | When the nozzle temperature in plastic injection molding is too hot, it can lead to discoloration of plastic parts. The nozzle delivers the molten plastic material into the mold cavity. If the temperature of the nozzle is set too high, it can cause the plastic to overheat and undergo thermal degradation. This degradation alters the chemical composition of the plastic, resulting in discoloration or yellowing of the final parts. | Bring the nozzle temperature up to within 10 degrees Fahrenheit of the front of the barrel’s temperature. To compensate for heat loss between the nozzle and the sprue bushing against which it seats, an additional 10 degrees is applied. |
5. Excessive Cycle Time | When the cycle time, which refers to the time it takes for a complete injection molding cycle, is prolonged beyond the recommended duration, it can result in prolonged exposure of the plastic material to high temperatures. Prolonged exposure can cause thermal degradation, leading to alterations in the plastic’s molecular structure, which, in turn, may cause discoloration or yellowing of the finished parts. | Adjust the cycle time to suit the material and wall thickness of the molded component. The barrel temperature should be lowered if longer cycles are required. |
6. Improper Screw Design | The screw plays a crucial role in melting, mixing, and homogenizing the plastic material during molding. If the screw design is not optimized or mismatched for the specific material used, it can result in inadequate heat transfer or uneven melt distribution. This can lead to variations in temperature and inconsistent melting, causing thermal degradation and discoloration of plastic parts. | To solve this issue, we need to optimize the screw’s compression ratio for the molding material. The optimal compression ratio can be provided by the material supplier, and the compression ratio of the screw being used can be provided by the manufacturer of the screw. In the case of heat-sensitive materials, it may be necessary to replace the screw with a more appropriate compression ratio. |
Also Read: Principles of Selecting and Creating an Effective Mold Base
Discoloration Due to Mold Issues:
Problem | Problem Scenario | Solutions |
1. Improper Mold Temperature | The mold temperature plays a critical role in the cooling process and the overall quality of the finished parts. If the mold temperature is set too high or too low, it can result in inadequate cooling or improper crystallization of the plastic material. This can lead to thermal stress, color variations, or even burnt marks on the surface of the parts, resulting in discoloration. | The temperature of the mold should be set at the level suggested by the material’s manufacturer. For lighter pieces, mold heating may be increased. Reduce the mold temperature if the finished products are excessively dark. Ten cycles should pass between modifications to allow the machine to stabilize. |
2. Inefficient Cooling | Proper cooling is essential for solidifying the plastic material within the mold and achieving the desired part quality. When cooling is inadequate or uneven, it can result in incomplete solidification or improper crystallization of the plastic. This can lead to thermal stress, color variations, or even burnt marks on the surface of the parts, causing injection molding discoloration. | The cooling lines should be strategically placed and optimized from the outset of the design process. The mold designer is responsible for this. Fixing a poorly constructed mold throughout the molding process can be quite difficult. One option is to separate the temperature regulation of the two mold sections into two separate units. |
Also Read: CNC Laser Cutting Machine 101: A Detailed Buying Guide
Additional Causes of Discoloration:
Problem | Problem Scenario | Solutions |
1. Contaminated Raw Material | Contaminated raw material can contribute to plastic part discoloration in injection molding. When the raw material used in the process contains impurities, such as foreign particles or incompatible additives, it can lead to color variations or even specks on the surface of the molded parts. These impurities can interfere with the melting and homogenization, causing uneven distribution and discoloration of plastic parts. | The answer is to always store your supplies in clean, covered containers that properly label their contents, including the material’s grade and melt flow. |
2. Inconsistent Process Cycle | The process cycle consists of various stages: material melting, injection, cooling, and ejection. If any of these stages are improperly executed or vary between cycles, it can result in temperature fluctuations, inadequate cooling, or insufficient material homogenization. Such inconsistencies can lead to thermal stress, incomplete solidification, or uneven color distribution, resulting in part discoloration. | Use the machine’s automatic cycle if possible; the operator should only intervene if an emergency arises. Rather than hiring a human ”operator,” replace them with a robot. In addition, stress the significance of regular cycles to all staff members. |
Conclusion:
Knowing what causes injection molding discoloration will help ensure your parts are strong and immaculate.
If you work with the proper manufacturing business, you can be confident that they understand how to eliminate discoloration and other plastic injection flaws. Prototool takes pride in having a defect-free injection molding process.