Are you a professional working in the manufacturing industry? Or do you plan to enter the injection molding manufacturing sector as a skilled machine operator? Either way, understanding the injection molding process and the common issues that may occur, including short shots, is crucial.
Now injection molding is a highly popular manufacturing process. However, despite its widespread use and popularity, injection molding has challenges.
One common issue in injection molding is a short shot, which can significantly impact the quality of the final product. And as a skilled professional operating an injection molding machine, you need to know what causes short shots in injection molding and how to fix short shots in injection molding.
To help you with that, we have listed all the causes, evaluation methods, and short-shot solutions below. Please keep reading to learn all about them.
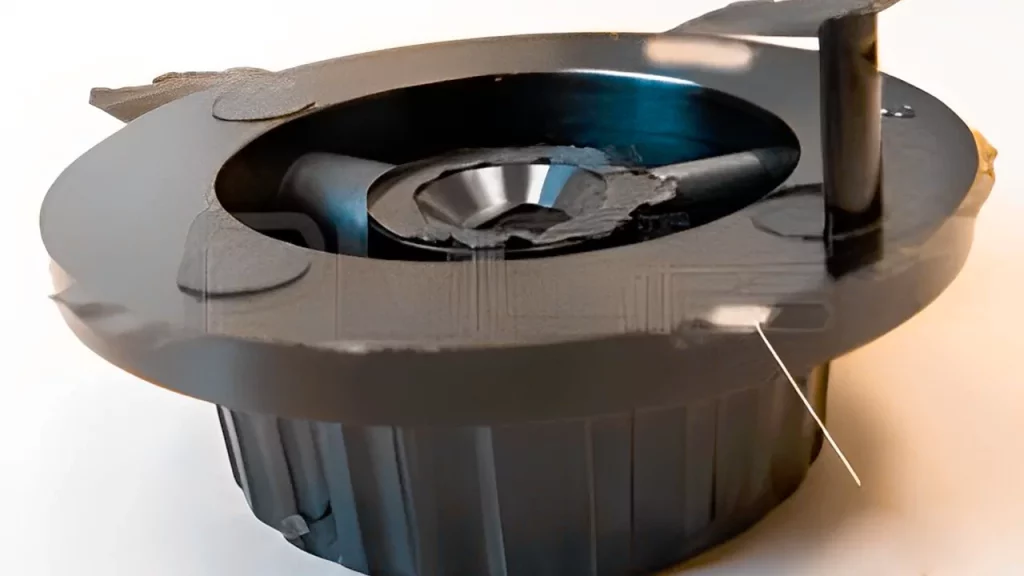
What is a Short Shot in Injection Molding?
In injection molding, a “short shot” is when the molten plastic doesn’t fill the mold cavity. This issue can lead to a part that isn’t complete or has visible flaws. How does it happen? Typically, short shots occur when the plastic injection mold doesn’t get enough plastic to fill the whole mold cavity, so there are empty spots.
These empty spots further lead to causing issues in the product part’s appearance, quality, and overall performance. For instance, parts with short shots may have weak spots or other flaws that affect how long they last and how well they work.
Hence, it’s best to avoid short shots in the first place by understanding what causes short shots in injection molding and methods of troubleshooting short shots in injection molding. Many things can cause short shots, such as insufficient injection pressure, wrong temperature settings, or insufficient plastic material. Understanding these causes can be the best approach for eliminating short shots in injection molding.
Understanding What Causes Short Shots in Injection Molding?
Whether you are familiar with the problem of short shots or hearing the first time about it, there can be many causes of this common issue that you may often overlook during manufacturing.
But don’t worry; by understanding the causes and their emergence, preventing or correcting short shots in injection molding can be easier on time. Now there are several common causes of short shots in injection molding, including:
Injection Pressure:
If the injection pressure is too low, the plastic might not be able to fill the entire mold cavity, causing a short shot. The injection pressure should be set high enough so that the plastic can fill the whole cavity without flashing or other problems.
Injection Speed:
The plastic could solidify prematurely and fail to occupy the entire mold cavity if the injection speed is too sluggish. Conversely, if the injection speed is too rapid, the plastic may be incapable of permeating all the nooks and crannies of the mold, resulting in a short shot. Therefore, to ensure that the mold is filled with the appropriate plastic in the proper amount of time, the injection speed should be adjusted accordingly.
Temperature:
If the molten plastic’s temperature is too low, it might not flow as well or fill the mold cavity, causing a short shot. In contrast, plastic may break down or cause other problems if the temperature is too high. Therefore, the temperature should be set based on what the plastic material and the shape of the mold need.
Ventilation:
If the mold doesn’t have enough ventilation, air could get stuck in the mold cavity. This would stop the plastic from flowing to all parts of the mold and cause a short shot. The mold should have enough vents so air can get out as the plastic fills the cavity.
Wall Thickness:
If the part’s walls are too thin, the plastic may not be able to fill the mold cavity. This is called a “short shot.” The mold design should be optimized to ensure the part’s wall thickness is right for the type of plastic used.
Mold Design:
A short shot could happen if the mold design isn’t optimized for the plastic material and the shape of the part. When designing the mold, things like gate size, gate location, part geometry, and the type of plastic should be considered to ensure the mold can make high-quality parts without short shots.
Detecting Short Shots in Injection Molding:
There are several ways to identify short shots in injection molding, including:
Visual Inspection:
Looking at the molded parts, you can often tell if there are short shots. A short shot usually has a void or sink mark where the plastic doesn’t fill the mold.
Dimensional Analysis:
Measuring the sizes of the molded parts can also help find short shots. If the part doesn’t fit within the allowed range of sizes, it could mean that the plastic didn’t fill the mold all the way.
Defect Analysis:
Analyzing problems with the molded parts, like sink marks or warping, can help find short shots. These flaws can happen when the plastic doesn’t fill the mold.
Process Monitoring:
Process monitoring in real-time can help find short shots as soon as they happen. Monitoring the injection pressure, injection speed, and temperature of the molten plastic can help determine why the plastic isn’t filling the mold cavity.
Common Examples Identifying the Presence of Short Shots in Injection Molded Parts:
So for all the novice and mid-level professionals unfamiliar with the presence of short shots at most, it may be difficult to evaluate if this defect is already present or not at most times. However, certain cases suggest that there are short shots that you have to fix. Some examples of such cases are:
- A plastic part with a void or sink mark in a particular area indicates that the plastic did not fill that area of the mold cavity, resulting in a short shot.
- A plastic part that is out of spec concerning its dimensions may indicate that the plastic did not fill the mold cavity.
- Warpage or other defects in a plastic part could indicate a short shot if the plastic did not fill the mold cavity.
Learn more about injection molding defects
6 Ways to Correct Short Shots in Injection Molded Products:
Once you understand the causes and methods of detecting short shots in injection molding, it’s time to begin troubleshooting them. But is correcting short shots in injection molding even possible? It surely is!
Once a short shot has been identified, several ways exist to correct the problem and prevent it from occurring in future production runs. Some common methods for correcting short shots in injection molding include:
Increasing Injection Pressure:
Increasing the injection pressure is one of the most common ways to fix short shots. The molten plastic can be forced into every part of the mold cavity by increasing pressure. This makes sure that the mold is filled.
Changing the Speed of the Injection:
The speed of the injection can also be changed to help fix short shots. If the speed is too slow, the plastic may harden before it can fill the mold. If the speed is too fast, the plastic may not be able to flow into all the corners and crevices of the mold. Changing the speed can help make sure that the mold is filled.
Changing the Temperature:
If the molten plastic’s temperature is too low, it might not flow as well or fill the mold cavity, causing a short shot. In contrast, plastic may break down or cause other problems if the temperature is too high. Hence, changing the temperature can help ensure the plastic flows correctly and fills the mold.
Ensuring the Presence of Ventilation:
If there isn’t enough ventilation, air can get stuck in the mold cavity. This stops the plastic from flowing into all areas and causes a short shot. By making the vents bigger, air can escape more easily, making it easier for the plastic to fill the whole mold.
Adjusting Wall Thickness:
If the part’s walls are too thin, the plastic might not be able to fill the mold cavity, causing a short shot. Changing the mold’s design to ensure the walls are the right thickness can help fill the mold cavity.
Changing the Size and Location of the Gate:
The gate accesses the mold’s cavity, which allows the plastic to enter. A “short shot” occurs when the plastic cannot reach all parts of the mold due to an incorrect gate size or location. Altering the gate’s dimensions and placement guarantees the mold is plastic-filled.
Conclusion:
Finding the source of your short shots is the first step toward fixing them. Having said that, once you understand what causes short shots in injection molding and how to fix short shots in injection molding, correcting short shots in injection molding becomes easier.
The injection molding technique can be modified when the root cause has been identified to guarantee full mold cavity fill. By eliminating the root cause of short shots, you can boost output quality, reduce rework and scrap, and save money while keeping issues like short shots from occurring.