Are you wondering what a typical mold base is? It may appear to be a simple phenomenon. Precisely, a mold foundation is a pre-machined base that helps complete your mold per your requirements.
However, when selecting, preparing, and using it – there’s more to a standard and effective mold base than just that. And to ensure that your plastic product manufacturing has no errors or issues, it’s important to be very careful when selecting and preparing the mold base.
This article will discuss selecting the ideal mold base before proceeding with the contemporary injection molding tasks.
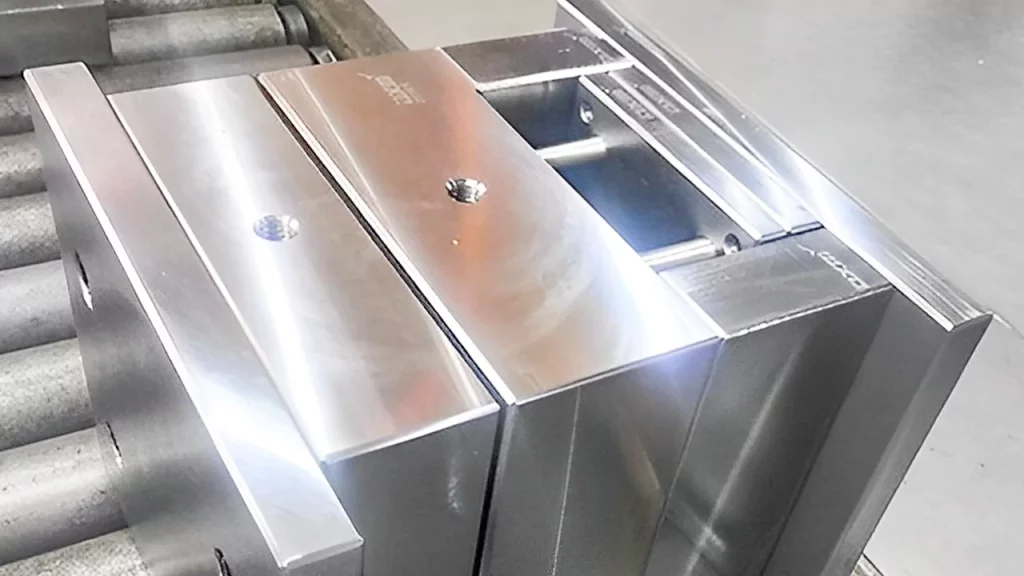
Importance of a Mold Base:
The mold foundation is the most important component since it is the structure for a whole set of molds. This base consists of a wide variety of steel plates and components. The manufacturing of mold begins with selecting a suitable mold base, which is a very significant phase because the size of the selected mold bases directly affects the quality of the mold.
However, if you do not choose the mold foundation correctly, the mold will fail in the mold creation process, and the mold base itself will be useless.
Also Read: Designing Top-Quality Plastic Molded Parts: 7 Proven Tips
Selection Principles for Different Types of Mold Base:
When deciding on a mold base, various factors, including component structure, mold parting requirements, and economic factors, should be considered. The following outlines the general guidelines for choosing a mold foundation.
Selecting a Side Gate Mold Base:
While selecting this mold base, look for the following:
- Simple construction
- Criteria for a surface finish that aren’t very stringent
- Permission for gate marks on the side
- Absence of any additional specialized constructions
Note: It is preferable to choose the side gate mold base instead of the pinpoint gate mold base if the side gate mold bases are applicable. You can use this side gate mold with the one-step splitting mold.
Selecting a Point Gate Mold:
While selecting this mold base, consider that:
- Pinpoint gate mold bases are typically chosen when the single-cavity mold and the molded object have a large projection area on the parting surface and require multipoint feeding.
- Choose the pinpoint gate mold base for molds of high-precision items or those with fewer dimensional tolerances and higher requirements on the mold’s service life.
- For a mold with multiple cavities, at least some component portions need to be fed from the inside.
- Molds for gears, multi-cavity tire molds, and other types are available.
- When it comes to molds with multiple cavities, some sizes can vary quite a bit. It is advisable to avoid positioning the gate bushing in the center of the mold when utilizing an edge gate configuration.
- Products that have a high barrel or a shell form.
Selecting a Simplified Point Gate Mold Base:
While selecting this mold base, make sure that:
When large core-pulling devices (slides, cylinders) are on both sides, selecting the precise gate mold base will significantly increase the time required. In this particular scenario, the simpler pinpoint gate mold base is the superior choice.
Additional Tips for Selecting The Right Mold Base:
Other key aspects of being aware of when you pick a mold base include the following:
- When the frame of Plate A is deep (typically greater than 60 mm), one should consider using the through-frame or the H-shaped mold base; however, Plate A should not adopt the through-frame for mold bases that include a slide or a cavity slide. Consider utilizing an H-shaped mold foundation whenever the Plate A frame is deep (often more than 60 mm).
- You can use the I-shaped mold base whenever the overall dimension of the mold base is less than 250 millimeters (including 250 millimeters). Likewise, you can use the T-shaped mold base whenever the size of the mold base falls between 250 and 350 millimeters. For mold bases greater than 400 millimeters, it’s important to use the T-shaped mold base when there is a slide and the H-shaped mold base when there is no slide.
- Utilize the mold base with a support plate when the core is round.
- There is a strict prohibition on pairing the mold base with an ejector plate with the cavity guide pin and guide bushing in the core.
- When there is a cavity slider or a slider with a cavity, the guide pin needs to extend 10-15 millimeters before you insert it into the slider. This means you can use a cavity guide pin and a core guide bushing when the guide pin is already exceptionally long to further increase its length.
3 Key Factors to Consider When You Select a Mold Base:
Below are the three crucial aspects you should keep in mind when selecting a mold base for your next injection molding project:
How Good is the Mold Base?
Undoubtedly, first impressions are the most important in determining quality. How is the mold base packaged when you receive it? What is it finishing like? If the base of your mold seems dragged behind instead of transported on the truck, it is time to reconsider the manufacturers you have chosen to work with.
Another facet of quality is that it must be consistent. If you order the same standard mold base seven days in a row, each base should be the same as the one before. Why should both of your bases be the same? What happens if someone accidentally breaks a plate? After assembly, some mold bases appear square due to grinding.
When installing a replacement plate, this presents a difficulty because it will cause the new Plate to be crooked compared to the remainder of the base. It is not going to fit correctly. The foundation plates of standard molds need to be entirely interchangeable and straightforward to replace.
It is essential that the manufacturer of your mold base machines it from the center out to the finest tolerances possible, ensuring that all parts are completely interchangeable. Not only should one be able to anticipate excellence of this caliber, but it also shouldn’t be out of their price range.
Does It Help Save Manufacturing Time?
Simply put, with advanced tools, the lead times are getting shorter. Considering this, the use of standard mold bases helps save time. These mold bases arrive to you usually within twenty-four hours of the order date. When shipping takes a week, a typical mold base is no longer considered standard. Additionally, new plates and components must be readily available for same-day shipment in an emergency.
Exist further opportunities to economize time and shorten the time needed for delivery? The mold base provider must have a library of downloadable CAD designs available in all major CAD platforms throughout the design process to reduce time spent on design.
In a world that is fast transitioning to 3-D design, it is becoming increasingly vital for the provider to have actual 3-D configurable models available in addition to the more conventional 2-D models.
In addition to these time-saving options, does your provider provide any others? Do they keep A and B plates in stock, and do those plates have pre-cut pockets and pre-cut lock pockets? Plates that have already been machined can save you significant time.
Is It Cost-Efficient?
What does your investment in a standard mold base entail? What perks do you have to pay an additional fee for that should be included in the base price? These days, standard mold bases shouldn’t be simple and limited.
Instead, they should have vented leader pins, pry slots, eyebolt holes, and even guided ejection. These functionalities and the associated components should be commercially available at no additional cost to the buyer.
Other improvements to typical mold bases include chamfered edges and safety straps. These additions are not as major as the others, but they are still beneficial. The careful attention paid to even the most minute details is another factor contributing to a mold base’s high value.
Now as evident as it sounds, time is money for everyone. Hence, you can limit the time you spend machining the mold with the help of the number of features and options you get from the mold base supplier. As the name suggests, standard features should be easily accessible so as not to impact the delivery of the mold base.
Conclusion:
A mold base is an essential component of a mold since it is the main component of a mold that is assembled from a variety of steel plates and pieces. As a result, the size of the selected mold bases directly impacts the mold’s quality.
Similar Read: Key Injection Mold Components You Should Be Familiar With