Warpage, the injection molders‘ nemesis! It’s a common problem, especially during the fine-tuning process. Now picture a part that should match the cavity but decides to deviate, resulting in a warped section. In this scenario, even non-experts can spot the bending or twisting.
So what do you do in this situation? Simple: avoid unintentional bending to prevent warpage in plastic products from occurring in the first place on the plastic part.
However, if you still encounter the same issue, it’s crucial to identify the cause, types, and solutions of warpageto prevent it from impacting the overall quality of the injection molded part.
Today, we’re going to demonstrate a detailed approach to understanding, detecting, and solving defects like warpage.
Also Read: Al-Assisted Injection Molding: How Artificial Intelligence is Transforming Manufacturing
The Different Types of Warpage or Shrinkage:
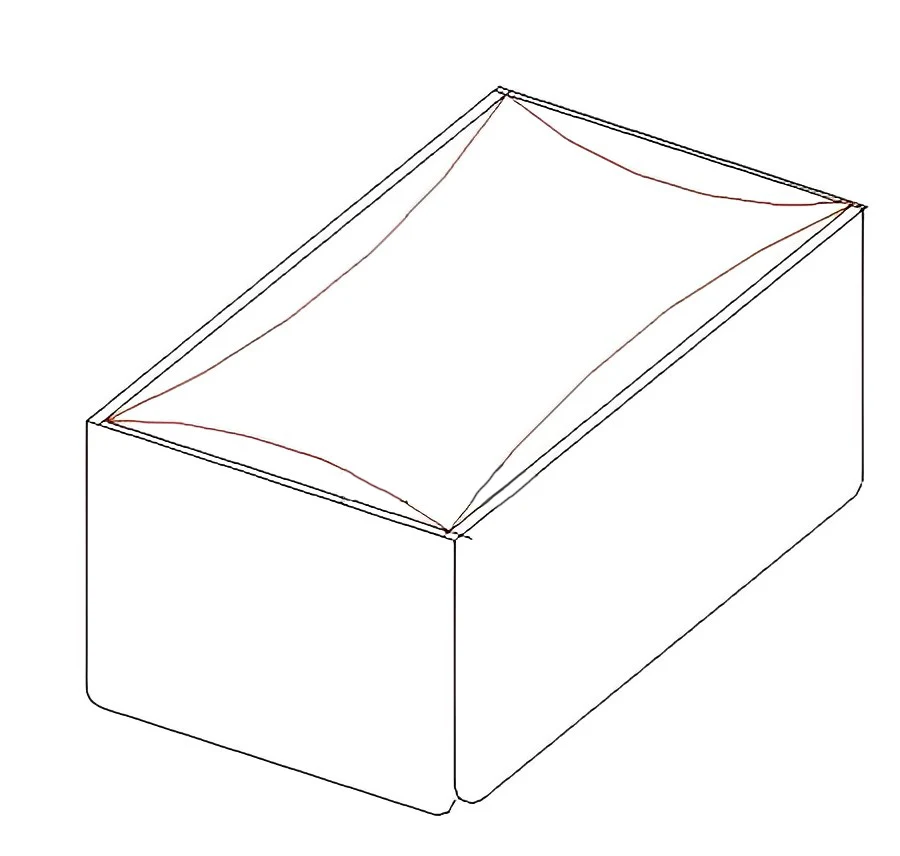
So what exactly is a warping? Simply put, it’s only a product shape difference due to shrinking. In other words, it is a type of shrinkage that extends in all directions and consistently reduces product size while maintaining shape.
However, any change in the element’s orientations will cause internal stresses. If these stresses exceed the component’s structural integrity, a warp will emerge in the ejected component.
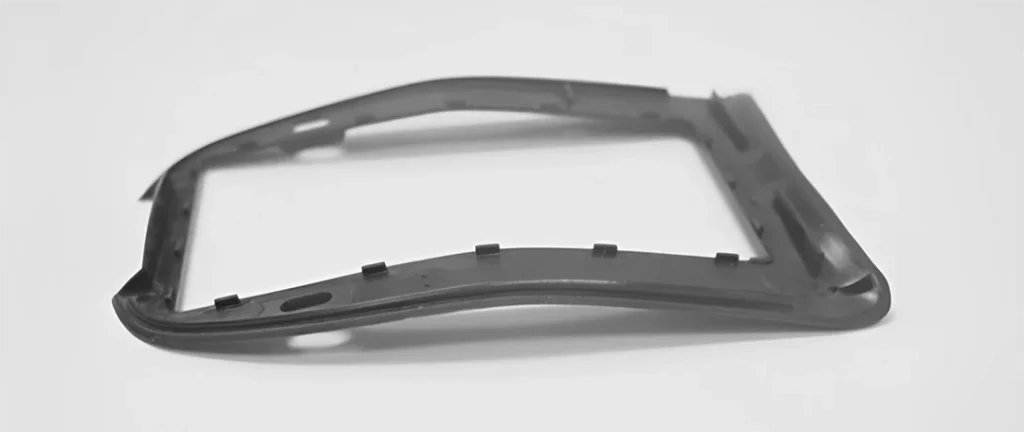
There are three forms of shrinking in plastic parts, including
Regional Shrinkage
The regions closest to the gate and the regions closest to the end of the fill are the most likely to undergo regional shrinkage. When identifying this shrinkage, the difference between the thickest and thinnest areas in the affected region should be obvious.
If the plastic product is undergoing regional shrinking, you will find one area of the product contracting faster than the others.
Directional Shrinkage:
Even though shrinkage varies from molecule to molecule and fiber alignment to fiber alignment, it can also occur in the orientation of the materials. At most, shrinkage manifests itself in both amorphous and crystalline substances.
But in contrast to crystalline materials, which typically shrink perpendicular to the flow direction, amorphous materials tend to contract along the flow direction.
Shrinkage via Thickness
When there is shrinkage on the cross-section of the part, the top part of the shrinkage is notably different from the bottom part.
In this scenario, the shrinkage or warpage in plastic products will be caused by thickness. As a result, you will have to bend the component from the side and decrease it further.
Different Plastics and Their Shrinkage Rates:
Shrinkage Rates of Common Plastics
Shrinkage Rates of Engineering Plastics
Name | Shrinkage Rate (%) | |
Raw Material | Add. 30% GF | |
POM | 2.5 | 0.5 |
PPO | 0.6 | 0.1 |
PA6 | 1.5 | 0.4 |
PA66 | 1.5 | 0.4 |
How To Prevent Plastic Warpage?
When you manufacture plastic through the injection molding technique, you will see that plastic can twist because of mistakes in the mold, the choice of material, or the injection molding machine.
To prevent this, it is important that you or your chosen injection molding company pays attention to all of these mentioned mistakes and avoid them in the first place, keeping the plastic from getting soft.
Still unsure how to keep the plastic from getting soft? Try these methods:
- Differential shrinkage and orientation effects can be kept to a minimum if your maker wants to.
- One can also set the gates of the mold so that the flow goes in only one direction.
- You can change the mold’s width to ensure it is the same thickness all over.
- The manufacturer should try to make the mold so that extra material is only added to the thick parts of the walls to make the structure more stable. This should only be done if the mold can’t be made stronger in any other way.
- The manufacturer can also add things like stiffening ribs to the design if they want to. You can change how the part is made so that there are no thick parts and the thickness of any features that meet the main surface is less.
- It’s important to remember that semi-crystalline plastic resins naturally shrink more than crystalline plastic resins, making them more likely to bend. If you don’t need these materials for your part or product, you should try to stay away from them.
Problems That Lead to Warping in Injection Molding + The Solutions:
Problem#1: Insufficient Injecting Time or Pressure
If there isn’t enough pressure on the filling, the plastic will cool and harden before the mold is filled properly.
The packing process is sped up if the plastic injection hold time isn’t long enough.
The molecules won’t be held together if there isn’t enough mold-filling pressure or hold time. This means they can move around uncontrollably as they cool. This makes the part cool down at different speeds, which causes the mold to twist.
Solution:
Make the injection pressure or hold time for the cast higher.
Problem#2: Inadequate Residence Time
The amount of time the resin is heated in the barrel is called its “residence time.” If there isn’t enough time for the molecules to stay in one place, the heat won’t be absorbed evenly throughout the object.
If you don’t heat the material enough, it will get stiff and cool before the mold is packed properly. The molecules shrink at different rates during the cooling process, which makes the mold twist.
Solution:
Add more time to the cooling part of the cycle to lengthen the time the water stays in one place. This will ensure the material stays in place for the right time and stop the mold from breaking.
Problem#3: Low Temperature in the Barrel
If the temperature of the barrel is too low, the resin can’t get hot enough to move.
Likewise, if the glue is not at the right temperature to flow and is pushed into the mold, it will harden before the molecules are packed correctly. This makes the molecules shrink at different rates, causing the mold to twist.
Solution:
Raise the warmth of the barrel. Make sure that the temperature of the material melted is the same throughout the shot size.
Also Read: A Brief Guide on Designing The Hot Runner Plate in Injection Molding
Problem#4: Low Temperature For Mold Growth
If the mold isn’t hot enough, the molecules will solidify before they pack together at different rates, which will cause the mold to twist.
Solution:
Raise the temperature of the mold based on what the resin seller says to do and make adjustments as needed. For every 10-degree change, operators should give the process ten re-stabilization rounds.
Problem#5: Different Temperatures in the Mold
When the mold temperature isn’t even, the molecules cool and shrink at different rates. This makes the mold shift.
Solution:
Look at the mold parts that touch the liquid resin. Use a pyrometer to determine if the temperature difference is more than 10 degrees F.
However, if the temperature difference between any two places is more than 10 degrees, even between the two halves of the mold, there will be a difference in how fast the parts shrink and the mold warp.
Problem#6: Low Temperature of the Nozzle
Since the tip is the last connection between the barrel and the mold, it’s important to look at it. If the opening is too cold, the resin can move more slowly, making it hard for the molecules to pack together correctly. The molecules won’t shrink simultaneously if they don’t fit together properly. This makes the mold warp.
Solution:
To solve this problem, make sure that the design of the nozzle isn’t affecting the flow rate.
Now, some nozzles aren’t made for the resin being used. If the correct nozzle for the flow and resin is being utilized and the mold is still warping, you should adjust the nozzle temperature by 10 degrees Fahrenheit until the warping issue is resolved.
Problem#7: Not Enough Flow
Resin manufacturers make different mixes for standard flow rates. Using these standard flow rates as a guide, you should choose a material that is easy to flow for products with thin walls and a stiffer material with thick walls.
For thin or thick-walled products, the operator should use the stiffest material possible since a stiffer flow improves the mold’s physical qualities. But the harder it is to push something, the stronger it is.
However, if it’s hard to push the material, it might harden before it can be packed. This causes molecules to shrink at different rates, which makes the mold shift.
Solution:
Manufacturers should work with the resin seller to determine which material will have the stiffest flow rate without causing warping.
Problem#8: Improper Processing Cycle
If the operator opens the gate too soon and the product comes out before the material has had enough time to cool down evenly, the operator has cut the process cycle short. A process cycle that isn’t always the same can cause shrinking rates that can’t be controlled, which can cause the mold to warp.
Solution:
Manufacturers should use a process loop that runs itself and only step in if there is an emergency. Most importantly, all workers should be told how important it is to keep process cycles consistent.
Problem#9: Inadequate Gate Size
When the gate size isn’t right, it slows down how fast the hot resin can flow through. If the size of the gate is too small, the rate at which the plastic fills can slow down enough to cause a huge loss of pressure from the point of the gate to the last point to fill.
This can cause the molecules to be physically stressed. When this stress is removed after injection, mold warp happens.
Solution:
The data from the resin source should be used to find the best size and shape for the mold gate. Most of the time, the best way to fix mold warpage in plastic products is to make the gate as big as possible.
Problem#10: Wrong Gate Position
In addition to the size of the gate, the position of the gate can also cause a mold to warp.
If the gate location is in a thin area of the part shape and the last point-to-fill is in a much thicker area, the filling rate can change from thin to thick. This may result in a substantial pressure drop. Eventually, this huge pressure loss can lead to a short or insufficient fill.
Solution:
The gate may need to be moved, so the mold must be redesigned. This is so that the mechanical properties of the end product can be met.
Sometimes, more gates need to be added to reduce air loss and reduce the amount of stress that is built into the mold.
Problem#11: Irregular Ejections
If the mold’s ejection system and press aren’t regularly checked and changed, they might not work right and cause uneven ejection force or parts that aren’t straight. These problems can cause stress in the mold as it tries to keep the part from coming out. After the part has been ejected and cooled, the forces cause the mold to warp.
Solution:
Operators should ensure the release system and press are checked and adjusted regularly. All adjusting tools should be locked to keep parts from moving and ensure they are well-oiled.
Problem#12: Improper Product Geometry
The product’s shape can also cause mold warping. The shape of a part can lead to many different filling patterns, which can cause the plastic to shrink differently in different parts of the hollow. If the design makes the rate of shrinkage uneven, warping can happen.
This is especially true if there is a lot of pressure loss in places where the wall stock is thin and not thick.
Solution:
In this regard, consulting professional plastic injection molding service providers like Prototool can help you address and solve the issue in time.
Suggested: Why Should You Consider CNC Prototyping? Usage Needs, Limitations, and Expert Tips
Wrap-Up:
Warping in injection molding or warpage in plastic products can be a huge concern when manufacturing plastic products. It does not affect the appearance of a product or part but also impacts the quality and performance of the part.
With this detailed guide, you can thoroughly understand how to detect and solve plastic part warping issues.