Warpage, el moldeadores por inyecciónnémesis Es un problema habitual, sobre todo durante el proceso de puesta a punto. Ahora imagine una pieza que debería coincidir con la cavidad pero decide desviarse, dando lugar a una sección alabeada. En este caso, incluso los no expertos pueden detectar la flexión o la torsión.
¿Qué hacer en esta situación? Sencillo: evitar el doblado involuntario para evitar que se produzcan alabeos en los productos de plástico en primer lugar en la pieza de plástico.
Sin embargo, si sigue encontrando el mismo problema, es crucial identificar la causa, los tipos y las soluciones del alabeo para evitar que afecte a la calidad general del pieza moldeada por inyección.
Hoy, vamos a demostrar un enfoque detallado para comprender, detectar y solución de defectos como alabeo.
Lea también: Moldeo por inyección asistido por Al: Cómo la inteligencia artificial está transformando la fabricación
Los distintos tipos de alabeo o contracción:
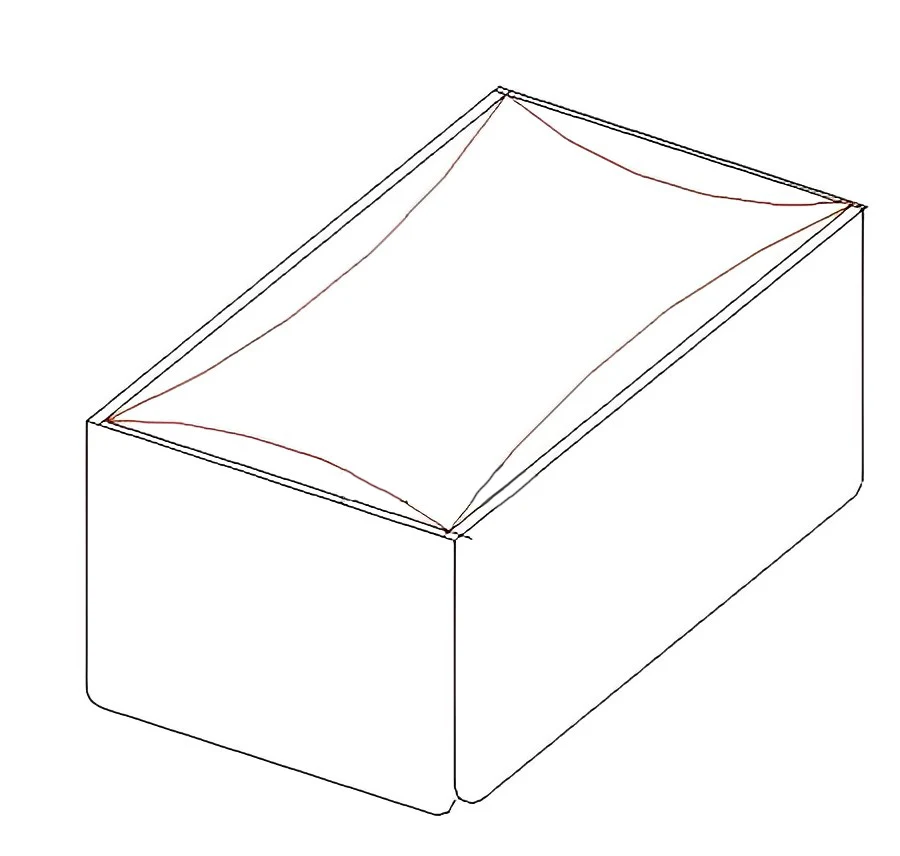
¿Qué es exactamente el alabeo? En pocas palabras, no es más que una diferencia de forma del producto debida a la contracción. En otras palabras, es un tipo de contracción que se extiende en todas direcciones y reduce sistemáticamente el tamaño del producto manteniendo su forma.
Sin embargo, cualquier cambio en las orientaciones del elemento provocará tensiones internas. Si estas tensiones superan la integridad estructural del componente, se producirá un alabeo en el componente expulsado.
Existen tres formas de contracción en las piezas de plástico, a saber
Contracción regional
Las regiones más cercanas al puerta y las regiones más cercanas al final del relleno son las que tienen más probabilidades de sufrir una contracción regional. Al identificar esta contracción, la diferencia entre las zonas más gruesas y más finas de la región afectada debe ser evidente.
Si el producto de plástico está sufriendo una contracción regional, observará que una zona del producto se contrae más rápido que las demás.
Contracción direccional:
Aunque la contracción varía de una molécula a otra y de una alineación de fibras a otra, también puede producirse en la orientación de los materiales. A lo sumo, la contracción se manifiesta tanto en sustancias amorfas como cristalinas.
Pero a diferencia de los materiales cristalinos, que suelen contraerse perpendicularmente a la dirección del flujo, los materiales amorfos tienden a contraerse a lo largo de la dirección del flujo.
Contracción por espesor
Cuando hay contracción en la sección transversal de la pieza, la parte superior de la contracción es notablemente diferente de la parte inferior.
En este caso, la contracción o alabeo en los productos de plástico se producirá por el grosor. Como resultado, tendrá que doblar el componente desde un lado y disminuirlo aún más.
Diferentes plásticos y sus índices de contracción:
Índices de contracción de los plásticos más comunes
Nombre | Índice de contracción (%) | |
Materia prima | Añadir 30% GF | |
PS | 0.6 | 0.1 |
PMMA | 0.5 | 0.1 |
LDPE | 2 | 0.5 |
ABS | 0.6 | 0.1 |
PVC | 0.4 | 0.1 |
Índices de contracción de los plásticos técnicos
Nombre | Índice de contracción (%) | |
Materia prima | Añadir 30% GF | |
POM | 2.5 | 0.5 |
PPO | 0.6 | 0.1 |
PA6 | 1.5 | 0.4 |
PA66 | 1.5 | 0.4 |
¿Cómo prevenir la deformación del plástico?
Cuando fabrique plástico mediante la técnica de moldeo por inyección, verá que el plástico puede torcerse debido a errores en el molde, la elección del material o la máquina de moldeo por inyección.
Para evitarlo, es importante que usted o su elegido empresa de moldeo por inyección presta atención a todos estos errores mencionados y evítalos desde el principio, evitando que el plástico se reblandezca.
¿Aún no sabes cómo evitar que el plástico se reblandezca? Prueba estos métodos:
- La contracción diferencial y los efectos de orientación pueden reducirse al mínimo si el fabricante lo desea.
- También se pueden ajustar las compuertas del molde para que el flujo vaya en una sola dirección.
- Puede cambiar la anchura del molde para asegurarse de que tiene el mismo grosor por todas partes.
- El fabricante debe intentar hacer el molde de modo que sólo se añada material extra en las partes gruesas de las paredes para que la estructura sea más estable. Esto solo debe hacerse si el molde no puede reforzarse de ninguna otra forma.
- Si lo desea, el fabricante también puede añadir al diseño elementos como nervios de refuerzo. Puede cambiar la forma en que se fabrica la pieza para que no haya partes gruesas y el grosor de cualquier elemento que se encuentre con la superficie principal sea menor.
- Es importante recordar que las resinas plásticas semicristalinas se contraen más que las cristalinas, por lo que es más probable que se doblen. Si no necesita estos materiales para su pieza o producto, debería intentar mantenerse alejado de ellos.
Problemas que provocan el alabeo en el moldeo por inyección + Las soluciones:
Problema#1: Tiempo de inyección o presión insuficientes
Si no se ejerce suficiente presión sobre el relleno, el plástico se enfriará y endurecerá antes de que el molde se llene correctamente.
El proceso de envasado se acelera si el tiempo de retención de la inyección de plástico no es lo suficientemente largo.
Las moléculas no se mantendrán unidas si no hay suficiente presión de llenado del molde o tiempo de retención. Esto significa que pueden moverse sin control a medida que se enfrían. Esto hace que la pieza se enfríe a diferentes velocidades, lo que provoca que el molde se retuerza.
Solución:
Aumentar la presión de inyección o el tiempo de retención de la colada.
Problema#2: Tiempo de residencia inadecuado
El tiempo de calentamiento de la resina en el barril se denomina "tiempo de residencia". Si no hay tiempo suficiente para que las moléculas permanezcan en un lugar, el calor no se absorberá de manera uniforme en todo el objeto.
Si no calienta el material lo suficiente, se pondrá rígido y se enfriará antes de que el molde se empaquete correctamente. Las moléculas se contraen a diferentes velocidades durante el proceso de enfriamiento, lo que hace que el molde se retuerza.
Solución:
Añada más tiempo a la parte de enfriamiento del ciclo para alargar el tiempo que el agua permanece en un lugar. Esto garantizará que el material permanezca en su sitio el tiempo adecuado y evitará que el molde se rompa.
Problema#3: Baja temperatura en el barril
Si la temperatura del barril es demasiado baja, la resina no puede calentarse lo suficiente para moverse.
Del mismo modo, si la cola no está a la temperatura adecuada para fluir y se introduce en el molde, se endurecerá antes de que las moléculas se empaqueten correctamente. Esto hace que las moléculas se encojan a ritmos diferentes, provocando la torsión del molde.
Solución:
Aumentar el calor del cañón. Asegúrese de que la temperatura del material fundido es la misma en todo el tamaño del disparo.
Lea también: Breve guía sobre el diseño de la placa de canal caliente en el moldeo por inyección
Problema#4: Baja temperatura para el crecimiento de moho
Si el molde no está lo suficientemente caliente, las moléculas se solidificarán antes de empaquetarse a diferentes velocidades, lo que hará que el molde se retuerza.
Solución:
Aumente la temperatura del molde en función de lo que indique el vendedor de la resina y haga los ajustes necesarios. Por cada cambio de 10 grados, los operarios deben dar al proceso diez rondas de reestabilización.
Problema#5: Diferentes temperaturas en el molde
Cuando la temperatura del molde no es uniforme, las moléculas se enfrían y se contraen a ritmos diferentes. Esto hace que el molde se desplace.
Solución:
Observe las partes del molde que están en contacto con la resina líquida. Utilice un pirómetro para determinar si la diferencia de temperatura es superior a 10 grados F.
Sin embargo, si la diferencia de temperatura entre dos lugares cualesquiera es superior a 10 grados, incluso entre las dos mitades del molde, habrá una diferencia en la rapidez con que se contraen las piezas y se deforma el molde.
Problema#6: Baja temperatura de la boquilla
Dado que la punta es la última conexión entre el barril y el molde, es importante vigilarla. Si la abertura está demasiado fría, la resina puede moverse más lentamente, dificultando que las moléculas se empaqueten correctamente. Las moléculas no se encogerán simultáneamente si no encajan bien. Esto hace que el molde se deforme.
Solución:
Para resolver este problema, asegúrese de que el diseño de la boquilla no afecta al caudal.
Ahora bien, algunas boquillas no están hechas para la resina que se está utilizando. Si se utiliza la boquilla correcta para el flujo y la resina y el molde sigue deformándose, debe ajustar la temperatura de la boquilla en 10 grados Fahrenheit hasta que se resuelva el problema de deformación.
Problema#7: Caudal insuficiente
Los fabricantes de resinas hacen diferentes mezclas para caudales estándar. Utilizando estos caudales estándar como guía, debe elegir un material que sea fácil de fluir para productos con paredes finas y un material más rígido con paredes gruesas.
Para productos de paredes finas o gruesas, el operario debe utilizar el material más rígido posible, ya que un flujo más rígido mejora las cualidades físicas del molde. Pero cuanto más difícil es empujar algo, más resistente es.
Sin embargo, si es difícil empujar el material, puede que se endurezca antes de que se pueda empaquetar. Esto hace que las moléculas se contraigan a ritmos diferentes, lo que hace que el molde se desplace.
Solución:
Los fabricantes deben trabajar con el vendedor de resina para determinar qué material tendrá la velocidad de flujo más rígida sin provocar alabeos.
Problema#8: Ciclo de tratamiento inadecuado
Si el operario abre la compuerta demasiado pronto y el producto sale antes de que el material haya tenido tiempo suficiente para enfriarse uniformemente, el operario ha acortado el ciclo del proceso. Un ciclo de proceso que no es siempre el mismo puede provocar tasas de contracción que no se pueden controlar, lo que puede hacer que el molde se deforme.
Solución:
Los fabricantes deben utilizar un bucle de proceso que funcione por sí solo y que sólo intervenga en caso de emergencia. Y lo que es más importante, hay que explicar a todos los trabajadores lo importante que es mantener la coherencia de los ciclos del proceso.
Problema#9: Tamaño inadecuado de la puerta
Cuando el tamaño de la compuerta no es el adecuado, se ralentiza la velocidad a la que puede fluir la resina caliente. Si el tamaño de la compuerta es demasiado pequeño, la velocidad de llenado del plástico puede disminuir lo suficiente como para provocar una enorme pérdida de presión desde el punto de la compuerta hasta el último punto de llenado.
Esto puede provocar que las moléculas sufran tensiones físicas. Cuando se elimina esta tensión después de la inyección, se produce la deformación del molde.
Solución:
Los datos de la fuente de resina deben utilizarse para encontrar el mejor tamaño y forma para la compuerta del molde. La mayoría de las veces, la mejor forma de solucionar el alabeo del molde en los productos de plástico es hacer la compuerta lo más grande posible.
Problema#10: Posición incorrecta de la puerta
Además del tamaño de la compuerta, su posición también puede hacer que el molde se deforme.
Si la ubicación de la puerta está en una zona fina de la forma de la pieza y el último punto de llenado está en una zona mucho más gruesa, la velocidad de llenado puede cambiar de fina a gruesa. Esto puede provocar una importante caída de presión. A la larga, esta enorme pérdida de presión puede provocar un relleno corto o insuficiente.
Solución:
Es posible que haya que mover la compuerta, por lo que habrá que rediseñar el molde. Todo ello para que puedan cumplirse las propiedades mecánicas del producto final.
A veces, es necesario añadir más compuertas para reducir la pérdida de aire y reducir la cantidad de tensión que se acumula en el molde.
Problema#11: Eyecciones irregulares
Si el sistema de expulsión del molde y la prensa no se revisan y cambian con regularidad, es posible que no funcionen correctamente y provoquen una fuerza de expulsión desigual o piezas que no estén rectas. Estos problemas pueden provocar tensiones en el molde al intentar evitar que salga la pieza. Una vez que la pieza ha sido expulsada y enfriada, las fuerzas hacen que el molde se deforme.
Solución:
Los operarios deben asegurarse de que el sistema de desbloqueo y la prensa se comprueban y ajustan con regularidad. Todas las herramientas de ajuste deben bloquearse para evitar que las piezas se muevan y asegurarse de que están bien engrasadas.
Problema#12: Geometría incorrecta del producto
La forma del producto también puede provocar el alabeo del molde. La forma de una pieza puede dar lugar a diferentes patrones de llenado, lo que puede hacer que el plástico se encoja de forma diferente en las distintas partes del hueco. Si el diseño hace que el ritmo de contracción sea desigual, puede producirse el alabeo.
Esto es especialmente cierto si hay mucha pérdida de presión en lugares donde la pared es delgada y no gruesa.
Solución:
En este sentido, consultar a proveedores profesionales de servicios de moldeo por inyección de plástico como Prototool puede ayudarle a abordar y resolver el problema a tiempo.
Sugerencia: ¿Por qué debería considerar el prototipado CNC? Necesidades de uso, limitaciones y consejos de expertos
Recapitulación:
El alabeo en el moldeo por inyección o warpage en los productos de plástico puede ser una gran preocupación a la hora de fabricar productos de plástico. No solo afecta al aspecto de un producto o pieza, sino también a su calidad y rendimiento.
Con esta guía detallada, podrá comprender a fondo cómo detectar y resolver los problemas de alabeo de las piezas de plástico.