Wire EDM (Electrical discharge machining) has been used for many years to make complicated parts and materials that can’t be made with other methods or are needed by design. This peculiar method is among the most productive and inexpensive production techniques. It is highly accurate and precise. It works on any part that conducts electricity, no matter how hard. Titanium, tool, stainless steel, and other hardened alloys can be used in EDM’s complex form fabrication. There are three types of EDMs: fast hole drilling EDM (also called “Hole Poppers“), sinker EDM (also called “Sinkers“), and EDM-wire (Wires). But in this article, we will look at Wire EDM and how it is used in die processing in depth.
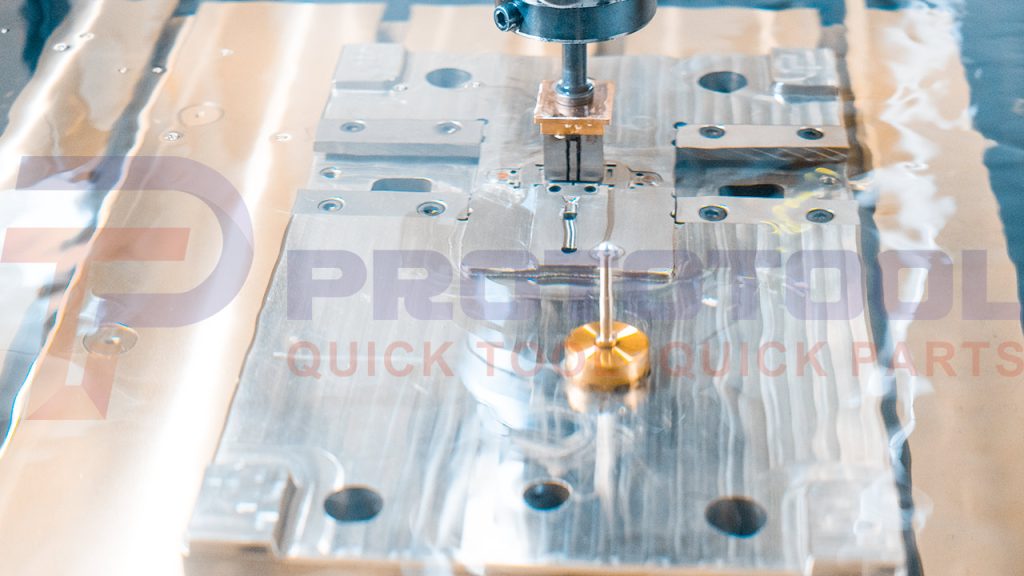
What Exactly is EDM-Wire?
Its name also knows as wire EDM of spark eroding or spark machining. This is a form of machining in which an electrically charged single-strand wire is continuously passed through a dielectric fluid (usually deionized water). The resultant discharge cuts conductive materials when the CNC brings it close to the grounded workpiece. Bringing the wire closer to the workpiece produces sparks that cut or erode the metal. They are typically cleaned and immersed in deionized water to remove dirt, cool the wire to prevent it from snapping, and prevent sparks from flying.
EDM Technology Characteristics:
The machining mechanism of EDM differs from standard cutting processes in the following ways:
- Any conductive material can be processed using EDM technology. The ability of a material to be processed is mainly determined by its electrical conductivity and thermal characteristics and is unaffected by its hardness.
- Pulse discharges only last for a fraction of a second, so there isn’t much of a temperature difference, and very little heat is transferred to the material around it.
- The EDM surface has greater hardness compared to the machined surface, providing enhanced protection for the lubricating oil. Surface lubricity and wear resistance are better than machined surfaces under the same surface roughness, making them particularly appropriate for die manufacturing.
- During processing, the tool electrode does not touch the material being worked on, and the force between the two is minimal. The material of the tool electrode does not have to be more challenging than the material of the workpiece. As a result, the tool electrode is simple to produce.
- It is appropriate for processing low-rigidity workpieces as well as micro-processing. Besides, it is especially appropriate for cutting workpieces with complex surfaces because it helps replicate the shape of the tool electrode to the workpiece. It is effective for working with challenging materials or intricate shapes that are difficult to handle using traditional machining methods.
Advantages:
- No Need for Mechanical Force:
Wire EDM is different from many other ways of making things because it uses heat discharges instead of blows to cut through materials. The finished product remains deformation-free, without warping or any adverse effects from raw force during material removal.
- Formation of Complex Parts:
Creating elaborate or intricate forms and patterns can be created using finely focused electrical discharges. EDM-wire devices can create curves and holes in various materials, including the most rigid and brittle.
- Cost-Effectiveness:
Even the stiffest materials can be sliced with minimal effort using EDM-wire. Furthermore, because the process only removes the desired particles, you will reduce material waste. Your cutting kerf (cut width) is typically less than 0.015″. Furthermore, the procedure produces exact and accurate cuts. As a result, no additional machines are required for post-processing.
- High Tolerance:
A further advantage of Wire EDM is its ability to produce high tolerance independent of the material being processed. Using machinery with tolerances as small as a few microns, you can quickly achieve a tolerance of +/- 0.0005″.
- Accuracy and Efficiency:
The most significant benefit of EDM-wire is that the end product does not require other processes such as grinding, honing, etc. The method achieves high levels of accuracy and precision, especially when working with small components.
Wire EDM Application in Processing:
· EDM Perforation Techniques:
The most common kind of electrical discharge machining (EDM) is perforation. It is frequently employed in processing shaped holes (such as round holes, square holes, polygon holes, and special-shaped holes), curved holes, micro holes, and so on. Spark discharge gap and tool electrode size are crucial factors affecting dimensional accuracy in perforation.
· EDM Machining of the Cavity:
Forging dies, extrusion dies, die casting dies, plastic dies, and other types of dies are all included in the EDM cavity processing category. The machining of cavities is a more challenging process. Meanwhile, the cutting area varies widely, and because the cavity is so intricate, the electrode loss is not uniform. This significantly affects the machining accuracy, which is why it is essential. Pure copper and graphite with strong corrosion resilience should be used as electrodes if the goal is to increase the machining accuracy of the cavity. Graphite should also be utilized because it has high corrosion resistance.
· Convoluted Mechanization:
Powder mixing enhances electric discharge machining with fast and glossy surface results. This technique is utilized most frequently in the precision machining of complex die processing, particularly the processing of complex curved surfaces that do not lend themselves well to polishing procedures. It reduces surface roughness, eliminates manual polishing, and enhances overall component performance.
The multi-axis rotary system coordinates with various linear motions combined into various compound motion modes. As a result, This combination can help adapt to the requirements of processing various workpieces. These compound motion modes can be coupled in a variety of ways. By utilizing multi-axis linkage, the CNC EDM machine makes it possible to effortlessly complete the processing of intricate dies or minute parts, both of which are challenging for conventional EDM machines to accomplish.
During the processing, continuously shaking the electrode can be utilized. This is done so that the consistency of the discharge gap can be maintained despite the process’s high efficiency while maintaining a high level of stable processability. The shaking method is used in processing to obtain more uniform surface roughness on the side and bottom surfaces. Additionally, it makes it easier to control the processing size, which helps to ensure high-precision and high-quality processing. Shaking can obtain more uniform surface roughness on the side and bottom surfaces.
How Accurate is Wire EDM?
Your EDM-wire cut machine has adequate accuracy and can give an accuracy of up to 0.0025 mm and surface quality of up to 1.5 Ra (with a multi-pass and specified parameters).
Along the cutting path, this method creates a continuous slot. Theoretically, the slot’s width equals the wire diameter plus two times the spark gap, but in practice, it may be slightly larger. Sparks continue to fly between the exterior of the wire and the workpiece’s surface, allowing your EDM-wire-cutting machine to cut. Your machine’s manufacturer may provide a formula for determining the precise slot width based on the factors used in the process. When configuring the wire cutting, you need to consider the width of this slot.
Because your EDM-wire cut technique generates such intense heat, there is always a possibility of a heat-affected zone and recast layer. You will need to implement secondary processes to remove the recast layer.
You can use EDM-wire to cut complicated profiles with tight tolerances, even on small-size workpieces, which are unattainable with a standard machining technique. This is made feasible by the use of electrical discharge machines.
Pros and Cons of Wire EDM:
Pros
- Wire EDM can be used on hard and relatively soft materials without deformation or distortion. This is because the EDM machine has no contact with the material being worked on.
- Wire EDM machines are typically self-threading, allowing for quick continuation of the cutting process even if the wire breaks.
- Machinists can use the procedure to make intricate forms and patterns that would be difficult to achieve using traditional machining processes.
- The method produces pieces with fine and smooth surfaces compared to other fabrication procedures.
- EDM-wire machines have fewer fixturing needs than other conventional machines.
Cons
- Although wire EDM machines can be equipped with CNC and Automatic Wire Threading (AWT) capabilities to increase production speed, they are often much slower than conventional methods.
- This machining technology is exclusively applicable to conductive materials.
- While Wire EDM machines are generally simple to use, they may necessitate more attention than other types of machines. Their consumables might be costly, and professionals to operate the devices may need more supply.
Conclusion:
This is all to our detailed guide on Wire EDM and its applications in the production industry. If you have more questions or queries, feel free to contact our professionals at Prototool.