Today, the popular injection molding machine brands are endless. Located in different parts of the world, like the USA, Germany, China, Japan, Korea, Canada, etc., the options to choose from injection molding machines manufacturers are endless. Only if we talk about popular Japan-based brands that manufacture different types of this efficient production machine, it includes Nissei, Husky, Fanaco, Sumitomo, Toshiba, etc.
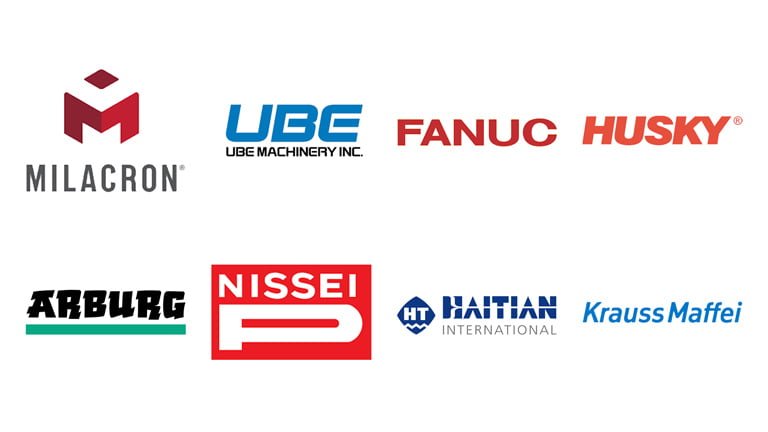
However, being aware of the best and most reliable brand when investing in plastic injection molding machines isn’t enough. Besides picking the suitable machine, having detailed know-how of e everything involved in this manufacturing process is also crucial. If you aren’t an injection molding machinery technician, this guide will take you through every phase and aspect of using the machinery and plastic and carrying out the injection molding machine process effectively. Keep reading to explore all of that!
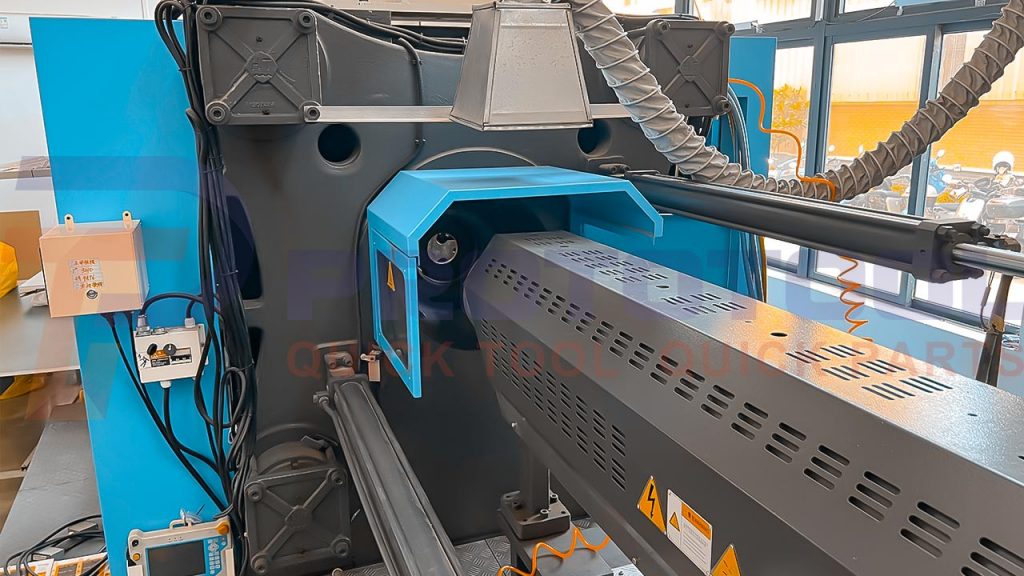
Operating Plastic Injection Molding Machines: A Detailed Summary
Plastic:
When picking the ideal plastic material for the plastic product manufacturing process, it’s essential to consider the following aspects:
According to the causes, various plastic products can be divided into three categories: heat stress, tissue stress, and partial stress. Hence, before you pick the ideal plastic material for your production needs, it’s essential to examine the internal tension of the products. You can do that by using the three methods of
- Instrument
- Impact
- Liquid medicine
Typically, PC, ABS, PA, PBT, and POM are the four engineering plastics most frequently used in resin. These are the primary components of plastic raw materials. However, plastic raw materials can be split into two categories, thermoplastics, and thermosetting plastics, according to how they respond to heat differently.
Machine:
When operating the machinery, keep the following pointers in mind to efficiently use the plastic injection molding machines for effective production.
- The components of injection molding machines can be categorized into the following four systems:
- The injection system
- The opening and closing die system
- The hydraulic transmission system
- The electrical control system
- In terms of the components of the filling system in Plastic injection molding machines, there are 7 different components. It includes; 1. Nozzle, 2. Reverse ring 4. Cylinder 5. Screw 6. Heating ring 7. Cooling ring.
- When using injection molding machinery, there are five different temperature categories. It includes:
- The cylinder temperature
- The mold temperature
- The drying temperature
- The temperature of the hydraulic oil
- The external temperature
- The injection molding machines can clamp in various ways, including the direct pressure type, the curved arm type, etc.
- Adding more to the machine usage, three distinct sections make up the 6 injection molding machine screws. It includes:
- The front section is the cutting section.
- The middle section is the plasticizing section.
- The back section is the metering section.
- The typical setting for screw looseness when molding high-precision goods on an 18.100T machine is 3-5 millimeters. Furthermore, you can separate the screw used in the 23-cavity injection molding machines into three sections:
- The conveying portion
- The compression section
- The metering section.
- So the higher the screw compression ratio, the more compact the particle pressure will be. As a result, it caused a quicker heat transfer between particles and a better effect of powder diffusion. You can achieve all this if the transport resistance is high and there is only a tiny amount of plasticization. Moreover, activating the pressure-holding switch too late can cause the injection pressure to rise, which can even result in the formation of a flying edge.
Production:
Understanding the different measurements, ratios, and other aspects of machine tools and components when using injection molding machines is crucial. The following aspects will help you better understand these aspects of production using such machines:
- When you discuss or consider injection molding, the term “time” can refer to several different aspects, including the injection time, the pressure holding time, the cooling time, the cycle time, the low-pressure protection time, etc. During the manufacturing process, the time spent cleaning the die surface is 2 hours per time. The exact time needed to complete the daily report during the production process. In addition, during injection molding and pressure holding, the stop valve’s primary job is to block the flow of plastic that would otherwise go back into the mold.
- The correct approach for connecting the molded waterway should be the equivalent of one in and one out of the connection method. Moreover, it is vital to change the mold with one that has a longer nozzle. Specifically, you can better decide if the nozzle depth of the mold is greater than 40 millimeters during the process of mold upgrading.
- Moreover, when using the machine in professional settings, it’s important to understand that the terms “sorting,” “rectifying,” “cleaning,” “quality,” “safety,” and “saving” are called “19.7S.”
- In terms of effective material processing, when there is no outside influence acting on the material, this can cause crystallization, orientation, shrinkage, and other forms of stress known as internal stress.
- During the manufacturing process, the kinds of forms that are necessary for mold repair include:
- Sheet for mold repairs
- Report on daily production
- Sheet for managing mold batches at the front.
- Different injection molding machines brands and plastic injection molding machines manufacturers design and create different types of machines. However, in most cases, the main flow channel, a diversion channel, a gate, and a cold feed make up the casting diversion of the mold in a usual injection molding machinery.
- When selecting the ejection distance for the three-plate and four-plate dies with an outer buckle restriction, it’s crucial to pay close attention to those details.
Managing the Production Issues as a Team Leader:
If there is an issue with the product’s quality, the team leader must notify the technician within 10 minutes so that they can fix it. A technician has one hour to diagnose and fix an issue before he/she must notify a foreperson. The foreperson has two hours to fix the problem before he must notify his superior. The supervisor should notify the management if the problem is not resolved within four hours.
Physical Quantities:
Physical quantities like temperature, friction, conduction, etc., are vital in improving or negatively impacting the production process. Hence, it’s important to keep the following points in mind to achieve an efficient production outcome:
- Molding temperatures of 260-320 degrees Celsius and drying temperatures of 100-120 degrees Celsius are needed for the 8 PC material, polycarbonate, sometimes known as bulletproof rubber. It’s because the temperature of PC glass is 140 degrees Celsius, and its rate of contraction ranges from 0.4% to 0.8%. Moreover, the drying temperature is 110 degrees Celsius plus or minus 5 degrees.
- The total heat source of the injection molding measurement process includes heat generated by convection, heat generated by conduction, heat generated by shear, and heat generated by friction.
- Back pressure plays a role that is divided into three distinct categories. These include:
- Plasticizing capacity
- Plasticizing quality
- Plasticizing precision.
- The friction heat and viscous heat generated inside the plastic and the heat generated by the heating element are the sources of heat for the pre-plastic measuring procedure.
- POM, a type of semi-crystalline material, has good dimensional stability. Hence, it is a good option for product selection during the plastic injection molding process. When using POM, you can adjust the melting temperature between 190 and 210 degrees Celsius, and the mold temperature should be higher than 90 degrees Celsius.
- In most cases, you should set the injection volume between 30 and 85 percent of the maximum injection volume the injection molding machines can produce.
- The total heat source of the injection molding measurement process includes heat generated by convection, heat generated by conduction, heat generated by shear, and heat generated by friction.
- Maintaining the hydraulic oil temperature in the hydraulic injection molding machines at a range between 20 and 65 degrees Celsius while it is operational is important.
- In terms of mold temperature, it is not always the same. Moreover, the product luster and mold cavity for the grain surface are also not the same during every production process. Hence, to adjust these physical properties of the product/machine during the production process, it’s better to keep the mold temperature higher and the sol fitting cavity surface tighter. This way, you can ensure that the injection products look more elegant. Otherwise, the mold temperature will remain the same if the luster is consistent.
Faults That Occur During the Production Process:
Whether you’re a beginner or a pro technician familiar with using plastic injection molding machines, sometimes it’s hard to avoid certain flaws that you may overlook during the process. As a result, it’s important to be well aware of the type of flaws that may occur during the production process and how you can solve/prevent them in time before it affects the final result of the produced plastic product.
In case of mistakes during production or injection molding machines operation, the produced product can face various flaws. Injection molded items frequently suffer from a variety of common flaws like batch peak, lack of glue, shrinkage, flow mark, weld mark, deformation, stress mark, and dimension change. Typically, if there is a shrinkage issue caused by production negligence or some other problem overlooked during production, you need to check the minimal residual quantity.
Other than this, there are different flaws/issues and preventive measures you can take during and after the production process is completed to ensure the efficiency of the machine and product. It’s essential to consider the following measures/concerns beforehand:
Silver Thread:
Silver thread or silver leak is common in the injection molding machines process. Moreover, silver streaks are almost always brought on by moisture or other volatile components when the raw material is not completely dried beforehand. Some additional causes include:
1. Cold glue friction production
2. The material is not completely dry
3. The pressure is too small
4. Resin decomposition
5. Mold temperature/low material temperature
6. Slow filling speed, etc.
Cleaning the PL Surface During Normal Production:
It is simple to generate static electricity on the surface of the mold during average production. Moreover, some rubber and iron chips can also fall to the edge of the mold mouth whenever the mold opens or closes due to shock. This reason easily affects the pressing mold. To avoid this negative impact on the machine’s pressing mold and ensure the durability and lasting efficiency of the injection molding machines, cleaning the PL surface is essential.
Instability of Quality and Size:
Even when you consider all the critical aspects of the product, machine, and production process, sometimes the quality of the final product and its size can be unstable. However, when manufacturing large-batch products, it’s crucial to maintain a certain quality and size of plastic products. Therefore, to prevent this issue, one must consider its causes. Typically, what causes this issue is scenarios like:
- The mold temperature is too high.
- The cooling time is short.
- The environmental temperature is unstable.
- The temperature of the cooling water is unstable.
- The temperature of the acting oil is unstable.
- The countercurrent ring is damaged, and the return material is too much.
- The temperature of the barrel is abnormal.
- The cold glue head is too much.
- The resin particle size is uneven.
- The electrical and hydraulic system of the injection machine is unstable.
- The feeding quantity is unstable.
- Uneven plastic particles and unstable shrinkage rate.
- Forming conditions (temperature, pressure, time) change, forming cycle is not consistent.
- A small gate, a varying size of the multi-cavity feed port, and an unbalanced feed.
- The mold accuracy is poor, the movement of the moving parts is unstable, and the positioning is inaccurate.
Restart the Production When the Heating Time of a Hot Runner is Prolonged:
During such situations, as a technician, you must adjust the material tube air shot to 3-4 die. Afterward, adjust the nozzle at the mouth, and then open the die with a piece of cardboard block at the back die. During this phase, it’s crucial to prevent the decomposition of the material shot to the back. Moreover, ignoring the die cleaning difficulties may cause pressure on the die, further affecting the production machinery and quality.
Protecting the Mold:
To protect the mold during and after the plastic injection molding machines usage, you need to:
- Limit switch sensitivity
- Lower pressure mode-locking force
- Lower pressure mode-locking speed
- Lower pressure mode-locking position
- Mode-locking monitoring time set slower/smaller
Plastic Shrinkage:
The process of plastic cooling and size reduction after removing it from the mold is known as shrinkage. Because the cause of this shrinkage is not only the thermal expansion and contraction of the resin itself but also related to various molding factors, the shrinkage of plastic parts after molding is called molding shrinkage. The main factors affecting the shrinkage rate include:
- Plastic variety
- Plastic parts structure
- Mold structure
- Molding process
Preventive Measures (SOPs) When Using Injection Molding Machines:
You can extend the service life of injection molding machines and production safety by adopting excellent operating habits for the machine. A technician must follow these habits to maximize the machine’s potential.
During the Beginning of the Process:
- First, you must thoroughly inspect the interior of the electrical control box to establish whether or not it possesses any water or oil. You should not turn the machine on if there is any indication that it has been exposed to the moisture of any kind. When the service team has finished cleaning and drying the various components, they can be turned back on.
- You must ensure that the voltage satisfies the criteria, generally kept within a range of 15%.
- Check that the “EMERGENCY STOP” button and the switch for the front and back safety doors are operating as they should. It is essential to check that the oil pump and the electric motor rotate in the same direction to ensure they work together.
- First, at the barrel end of the machine, make sure that each of the machine’s cooling channels is clear of any obstructions and has a surface that is as smooth as possible. Then, let coolant into the oil cooler in addition to the water jacket.
- Make sure all the moving parts are greased or oiled. If additional lubrication or greasing is required, add it.
- You may get the heating process underway for each section of the machine barrel by activating the electric heat control system. For achieving a reasonably uniform temperature throughout the machine, it is vital to keep the temperature stable for some time after each segment has been brought up to the proper temperature. This will help you accomplish the intended results. The amount of time necessary to maintain a temperature will vary depending on the type of plastic and the apparatus you use.
- Put in the hopper several plastic ingredients that are sufficient for the job. It is necessary to dry out specific components of the material in the beginning to meet the requirements for plastic injection molding.
- Maintaining a heat shield over the machine barrel will reduce your energy consumption while extending the useful life of the electric heater and the contactor. Use a heat shield to consistently protect the machine barrel and achieve this objective.
During the Procedures:
- You mustn’t minimize the significance of the safety doors in terms of their convenience.
- Always keep a close eye on the temperature of the hydraulic oil, and check to ensure that it does not exceed the allowed limitations at any time. However, the ideal temperature might range from 35 to 60 degrees Celsius. It is better to keep the operating temperature of the hydraulic oil be kept between 45 and 50 degrees Celsius. However, the temperature can be anywhere from 35 to 60 degrees Celsius.
- Check that the travel distance limitation switches on the machine are set up correctly to reduce the risk of a collision occurring while the machine is in operation.
After the Completion of the Procedure:
- Ensure thorough cleaning of the barrel before switching off the machine. Because of this, the residual materials will not experience oxidation or disintegration as a direct result of the extended heating.
- Ensure the elbow-bar mechanism lock is released before opening the mold.
- You need a hoist to lift the equipment that is located in the workplace. During the assembly and disassembly operations, you must handle large mold pieces and components with the utmost attention to keep the production environment risk-free.
Conclusion:
That is all to our detailed guide on helping you understand how to operate, process, and achieve a quality result as a plastic injection molding machines technician.
For more details and queries, feel free to contact our team of professionals!