Previously, CNC milling and CNC turning were carried out on separate machines – a milling machine and a turning machine, respectively. However, as technology advances, these two processes are combined into a single machine. Mill-turn technology combines milling and turning operations. Turning-milling machining uses this technology.
Even with modern technology and a time-saving mill-turn method, knowing the process and application of this technology is critical for part processing. So, without further ado, let’s go through all you need to know about operating such equipment.
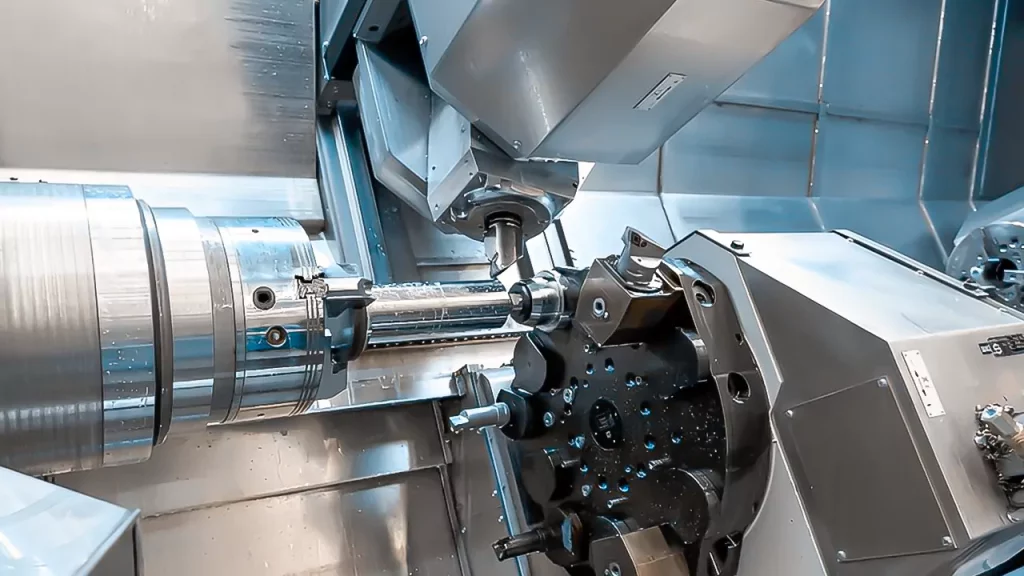
What is Mill-Turn Machining:
To better understand what the CNC turning-mil technology offers, it is helpful to examine the differences between milling and turning.
The CNC milling method involves using computerized controls and spinning cutting tools to remove small pieces of a workpiece in stages. This is accomplished via the procedure. The most common form of CNC machining is the one described here. On the other hand, CNC turning is a type of machining that consists of rotating material bars while holding them in place while a tool attached to the machine removes material to achieve the desired shape. This process is performed on a computer.
Earlier, both of these procedures were conducted in isolation for a significant time. A CNC turning-milling machine, known for its precision and accuracy, can combine the two processes and carry them out simultaneously now. The result of this technique is the creation of a wide variety of geometries and shapes for use with a wide variety of materials, such as metals and polymers.
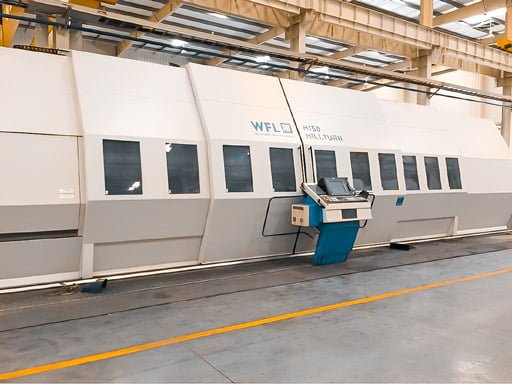
How Does It Process?
Milling Process
It is necessary to have a know-how of both turning and milling before attempting to comprehend the inner workings of a Turn Mill machine. CNC milling is a mechanical method that is used to make parts or components that have been specifically developed. This is accomplished by removing material from the workpiece using rotating multi-point cutting tools controlled by a computer. In most cases, three degrees of freedom are included in these systems.
They are not restricted in any way in their movement along the X, Y, or Z axes, even when the workpiece does not move. Milling is better suited for prototyping and producing small runs of products due to the limited dimensions that are possible with this operation.
Turning Process
Turning is a manufacturing process that entails holding bars of material in a three or four-jaw chuck and rotating them. At the same time, tools are fed to the piece to remove material until the desired shape and dimension are achieved. This continues until the bar of material has been turned into the desired form. All the work can be done from a single side of the CNC turning center when there is just one turret. However, some turning centers feature a main spindle and a sub-spindle for even faster operation.
In this system, the workpiece is machined on the main spindle and then carried to the sub-spindle, where the task is finished on the opposite side of the part in a single setup. The rapidity of CNC turning operations makes this method particularly well-suited for big production runs that must adhere to stringent deadlines.
In a nutshell, a Turn Mill is a hybrid CNC machine that combines milling (the rotation of the tool) and turning (the rotation of the workpiece) capabilities into a single, powerful, and adaptable device that is capable of completing complex operations in a shorter amount of time and with higher accuracy than conventional machining methods.
Understanding Common Configurations for Part Processing in Mill-Turn Machinery:
To effectively handle, run, and process components throughout the manufacturing phase, you must first understand the many parameters and configuration options available on current mill-turn machinery. Among the setup possibilities are the following:
· Vertical:
The spindle of a vertical CNC turning-milling machine is horizontally oriented, and workpieces are held vertically. In this setup, the cutting tools are oriented in the same direction as the holder. Vertical CNC turning-milling centers are stronger and more stable than horizontal counterparts due to gravity.
This design is very effective when cutting large and heavy workpieces since gravity helps to seat these huge items into the holding solidly.
· Horizontal:
This is the most popular configuration in many CNC turning centers. However, it is less prevalent in CNC turning-milling machines. The spindle of the CNC mill-turn machine is horizontal in this case, and workpieces are thus held horizontally. The cutting tools have fallen out of the holder’s side.
This design is weaker than the vertical configuration because gravity does not help secure the holding workpiece. As a result, it is rarely utilized for large, heavy workpieces.
Tips: Learn more about the Comparison between Horizontal Milling and Vertical Milling
Benefits of Using Mill-Turn Technology for Part Processing:
· Better Speed
The speed with which CNC mill turn machines carry out their operations compared to conventional machining equipment is one of the primary selling factors associated with these machines. Machinists were formerly required to set up a workpiece on a lathe and finish turning operations on a part before setting up the workpiece on a mill and beginning milling operations. Today, however, machinists can set up a workpiece directly on a mill and begin milling operations immediately.
On the other hand, the CNC mill-turn machine is capable of doing both processes simultaneously, which means that machinists only need to set up the workpiece once and do not need to relocate the pieces until the process is through. Due to this, manufacturing industries see a corresponding acceleration in production and an increase in productivity.
· Adaptability in Machining Complicated Components
Traditional machining tools can only handle a certain level of geometric complexity before they reach their breaking point. Machinists may also be required to move parts from one machine to another when working on more complicated components.
The CNC mill-turn machine solves this issue since it can make intricate geometric shapes without requiring the materials to be transferred. This results in an improvement in the quality of the product and the manufacturing companies’ ability to develop these complicated products efficiently.
· Improved Preciseness
In general, CNC machines are quite accurate, which is true of the milling and turning processes that may be performed on them. However, CNC turning-milling centers offer an even higher degree of precision than conventional machines. This is partly because the machinist does not have to set up the raw material (workpiece) more than once throughout the operation. In contrast, when milling and turning operations are performed on separate machines, operators must continue to modify and move pieces even after one of the operations is finished.
The high accuracy and reproducibility provided by CNC mill-turn machines are even more beneficial to the manufacturing process when the product’s tolerance values are on the borderline. When working with these types of components, even the smallest mistake made while moving and readjusting pieces might result in the cancellation of the entire CNC machining operation.
· It Offers More Than Two Applications:
CNC turning-milling machines can perform various operations in addition to milling and turning because of their programmability. Due to this feature, industrial firms can put the machines to work in various machining projects.
Additionally, machinists would ordinarily be responsible for several duties, such as loading workpieces, removing parts, and probing, which can be totally automated and performed by the machine instead. The end consequence is that the operator has more time to devote to other responsibilities, and the industry sees a rise in overall production.
Where Are Mill-Turn Machining Used?
Today job shops with 25 or more people are the most likely to purchase a turn-mill machine. Precisely because smaller firms are often concerned about the expense and seek out less expensive turning centers or lathes with milling and drilling capabilities, while many huge corporations appear to be sluggish to adopt the new technology, this is beneficial for job shops that utilize turn-mill machines since it allows them to produce parts more cheaply.
A single turn-mill machine may execute procedures that previously required three, four, or five machines – lathes, milling machines, and machining centers. Furthermore, once they start down the road to turning-mill, shops can employ a machine to expand their business.
They can further grow their manufacturing business and expand their services using the presence of additional and efficient machinery. Note: a turning-mill machine can help small shop owners get work orders for processing parts that require a lot of milling or secondary procedures.
For more details and queries, feel free to contact us at Prototool.