As we aim to manufacture the ideal products, we need smart ways to handle the challenges that come with it. Now, imagine making parts exactly how you want them. How can you do that? This is where internal and external turning comes in. They’re like problem-solving tools for making products precisely as they should be.
Obviously, we all want to make parts that comply perfectly with our manufacturing requirements, but it’s not easy. The usual ways of manufacturing items sometimes don’t work well, especially when dealing with tight spaces, different materials, and specific measurements.
But guess what? Internal and external turning are like secret weapons that help us solve these problems. They’re special ways of doing things that guide us through the tricky parts of modern making. And, if you’re planning to implement these approaches to make your manufacturing processes more accurate, trust us – you’re making the right decision.
In this guide, we’ll help you better understand the use, mechanism, and potential of internal and outer diameter turning so it’s easier to implement these mechanisms whenever needed. Let’s begin exploring now!
External Turning Mechanism
Exterior turning is a crucial process focused on shaping the outer surface of a part to meet precise dimensional standards and achieve a smooth surface finish.
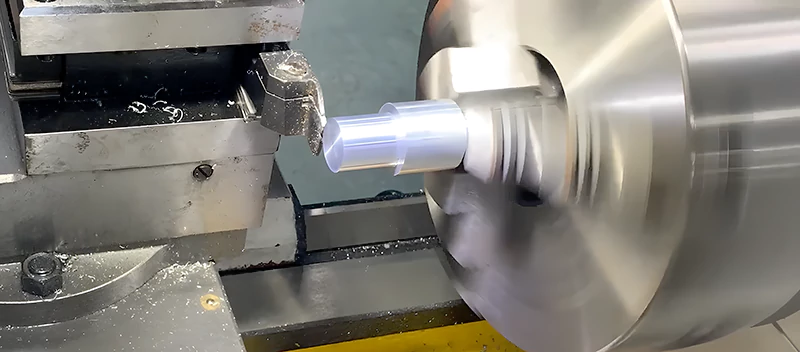
In this mechanism, ordinary cylindrical turning tools come into play, each designed with specific main declination angles to address various turning scenarios.
Tool Selection
- Ordinary Cylindrical Turning Tools: These tools, categorized by main declination angles such as 95°, 90°, 75°, 60°, and 45°, offer flexibility in handling different parts. The choice between 90° and 95° tools is ideal for slender shafts, while 75°, 60°, and 45° tools excel in turning short and thick outer circles. Notably, 45° tools can also perform chamfer turning.
- Negative-Angle Blade Turning Tools: Negative-angle blades, known for their economic efficiency, outshine their positive-angle counterparts. They are particularly beneficial for large back-feeding and processing with substantial feed amounts. The larger size of negative-angle blades enhances their versatility, and their tip strength surpasses that of positive-angle blades.
Considerations
Outer surface turning involves navigating the dynamics of axial and radial forces during cutting. The choice of tool angles becomes critical in determining the efficiency of the process.
The nuanced strengths and lengths of different blade shapes impact the overall performance, making it essential to align the tool selection with the specific demands of each turning operation.
Internal Turning Mechanism
Another turning approach often used in injection molding and CNC manufacturing processes is internal turning. Let’s explore the key considerations of this hole-turning method.
Characteristics
Internal turning or inner diameter turning, distinct in its approach, focuses on shaping inner holes while dealing with unique challenges. The semi-closed nature of the process makes it challenging to observe chip evacuation, influencing the overall processing quality. Deep hole cutting introduces vibrations in the arbor, necessitating specialized strategies.
Tooling Strategies
- Carbide Drill Arbor for Small-Diameter Hole Cutting: To address the challenges posed by small-diameter hole cutting, employing a carbide drill arbor proves effective. This tooling strategy enhances precision and reliability in these scenarios.
- Vibration Arbor for Medium Diameter and Above: Managing vibrations in medium-diameter hole cutting becomes crucial. Here, a dedicated vibration arbor comes into play, mitigating issues related to tool wear and ensuring a smoother cutting process.
Considerations
Internal turning requires a keen understanding of chip evacuation dynamics and the impact of hole depth on tool overhang. The choice of tools is restricted by the hole diameter and part length, necessitating careful consideration based on the specific requirements of each inner diameter turning operation.
Understanding Internal Turning’s Intricacies
Influencing Factors of Internal Turning Operation
- Tool Overhang Challenges: Unlike external turning, the length of the CNC turning part and the size of the toolbar significantly affect tool overhang in hole turning. This dynamic demands careful consideration, as long overhangs may lead to deflection and vibrations.
- Critical Cutting Forces: The direction and magnitude of cutting forces play a pivotal role in internal surface turning. Achieving minimal vibration and enhanced machining quality requires a keen understanding of tangential and radial cutting forces. The tool’s back angle becomes crucial, especially in small-diameter turning holes.
- Chip Evacuation and Clamping Dynamics: Challenges such as poor chip evacuation, improper clamping, and tool-related factors can impact internal diameter turning. Optimal solutions involve strategic tool nose radius selection, effective chip removal methods, and stable clamping techniques.
Considerations for Machining Quality Improvement
- Tool Nose Radius Selection: Choosing a small nose radius is key to minimizing radial and tangential cutting forces. The nose radius should be slightly less than the cutting depth for optimal results, ensuring a stronger cutting edge, improved surface texture, and uniform pressure distribution.
- Tool Groove Influence: The groove type of the cutting tool plays a decisive role in internal turning. Positive rake angle groove types with sharp cutting edges and high strength are preferred for machining inner holes.
- Cutting Edge Angle Consideration: The cutting edge angle significantly affects radial, axial, and composite forces. Selecting an angle close to 90° and not less than 75° is recommended to balance axial and radial cutting forces.
- Tool Treatment Impact: The rounding of the cutting edge influences cutting force. Uncoated tools exhibit smaller rounding than coated ones, impacting flank wear. Considerations for long tools overhanging and machining small holes are crucial.
- Clamping Stability: The stability of cutting tools and turned components relies on effective clamping. Achieving stability involves factors like surface finish, hardness, and clamping methods, emphasizing overall support for optimal results.
- Efficient Chip Removal: Chip removal significantly influences machining effects and safety, especially in deep hole and blind hole processing. Internally cooled tools, right-cutting fluids, and compressed air for through-hole machining are recommended for effective chip control.
Internal Turning’s Precision Paradigm
Hole turning’s meticulous approach achieves tight tolerances and intricate details within workpieces, ensuring the internal features meet specifications. Surface finish and dimensional accuracy are meticulously controlled, catering to industries where microns matter.
External Turning’s Exterior Precision
In surface turning, the focus lies on the workpiece’s exterior surfaces. The cutting tools, positioned outside the workpiece, sculpt the outer contours, ensuring dimensional accuracy and surface finish. Challenges include managing tool wear and optimizing cutting speeds for consistent results across varied materials and geometries.
External Turning’s Backbone Role
External turning is the backbone of manufacturing, catering to various components across industries. Its versatility shines from turning shafts in automotive applications to creating structural elements in construction. Outer diameter turning plays a pivotal role in producing components that form the backbone of various systems.
Advancements in Turning Technologies
The evolution of internal surface turning is a testament to its resilience in adapting to modern challenges.
Advancements in materials, including superalloys and composites, have pushed the boundaries of traditional machining. Internal turning‘s ability to tailor solutions for these cutting-edge materials solidifies its role as a key player in modern manufacturing.
- Adaptability to Superalloys: The rise of superalloys in various industries, particularly aerospace, has necessitated an evolution of machining. Internal turning has demonstrated unparalleled adaptability to these high-performance materials, creating intricate components with superior strength and durability.
- Handling Composite Challenges: Composites pose unique challenges in machining due to their heterogeneous nature. With its precision-focused approach, internal turning has emerged as a reliable solution for crafting components from advanced composite materials. The ability to navigate the complexities of composites underscores its significance in contemporary manufacturing.
External Turning Technological Strides
Embracing technological strides is at the core of the surface turning process. As the industry surges forward, external turning keeps pace by integrating real-time monitoring and adaptive tooling, thus elevating its capabilities to new heights.
- Real-Time Monitoring for Precision Assurance: The integration of real-time monitoring systems ensures that every cut adheres to the predetermined precision standards. Continuous feedback allows for instant adjustments, mitigating deviations and enhancing the overall accuracy of external turning processes.
- Adaptive Tooling for Dynamic Machining: External turning‘s embrace of adaptive tooling signifies a shift from static methodologies to dynamic machining approaches. Tools that can adapt to changing conditions in real-time optimize tool life, reduce wear, and contribute to the efficiency of the entire machining process.
- Predictive Maintenance for Operational Continuity: Predictive maintenance, powered by data analytics and machine learning, has become a cornerstone in outer surface turning. By anticipating tool wear and potential issues, machinists can proactively address concerns, ensuring uninterrupted operations and prolonged tool life.
- AI-Driven Machining for Enhanced Efficiency: Artificial Intelligence (AI) has woven its way into external turning, offering intelligent insights into machining processes. AI-driven machining optimizes toolpaths, cutting parameters, and overall efficiency, maximizing productivity while maintaining stringent quality standards.
Prototool: Your Professional Manufacturing Ally
As manufacturers grapple with the intricacies of modern components, Prototool emerges as the beacon of expertise, offering professional CNC manufacturing solutions that transcend the ordinary.
So, if you’re facing the challenges of chip evacuation, tool accessibility, and intricate geometries, our professionals at Prototool have meticulously honed their craft to address these challenges head-on.
Here, we ensure that your components are manufactured and crafted with precision. Whether it’s mastering internal turning, navigating confined spaces with finesse, or efficiency-driven external turning, our CNC manufacturing and injection molding solutions are tailored to exceed expectations.
Contact us today for more details and assistance.
Turning Method | Milling Method |
Internal Turning & External Turning Taper Turning | Shoulder Milling Side Milling Face Milling Ramp Milling Plunge Milling Peripheral Milling Helical Milling Groove Milling Vertical Milling & Horizontal Milling Conventional Milling & Climb Milling |