Rubber molding is the process of manufacturing rubber items. But are rubber products that common? In the nineteenth century, rubber was considered an essential raw material used to make various products in different industries. However, the demand and usage of rubber and its products have only grown over time.
But today, rubber goods are found in practically every industry. They are essential in sealing, abrasiveness, insulation, and so on. As a result, in today’s fast-paced environment, they are vital in maintaining high industry standards and progress. For manufacturing these rubber products, multiple advanced manufacturing processes are used. The rubber molding process is one of the most common procedures for making rubber items.
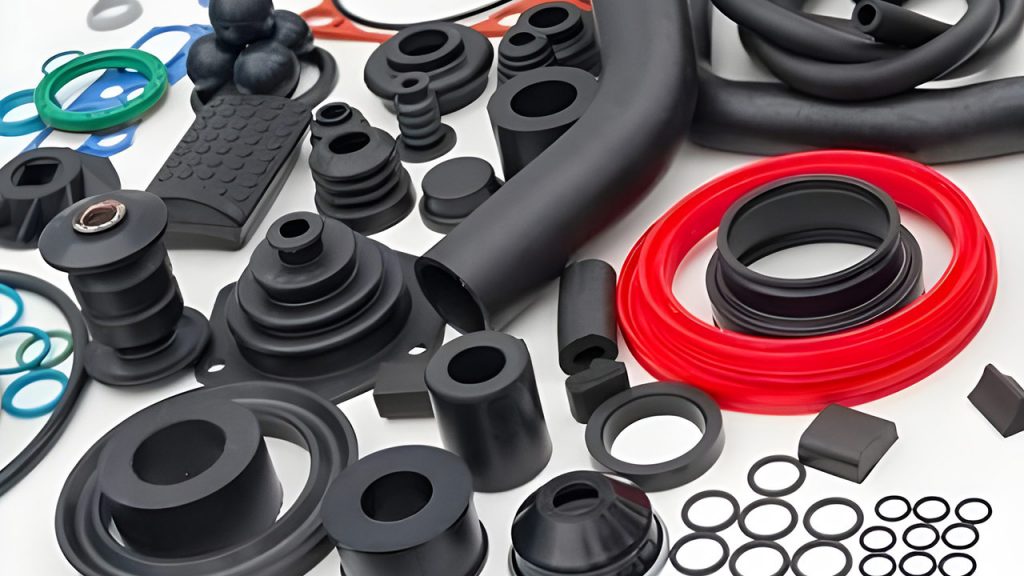
This comprehensive guide will provide all you need to know about rubber molding in 2022, from the types of rubber molding to the rubber products you can use and choosing the right rubber product. So keep reading to explore rubber molding in detail!
What Is Rubber Molding?
Rubber molding is an industrial process that converts raw rubber into a usable product. It is accomplished by various rubber molding process options that involve heating and bending rubber in a metal chamber. Injection molding, compression molding, and transfer molding are the three basic rubber molding methods used today.

Rubber Injection Molding:
Rubber injection molding is quite similar to the popular plastic injection molding process. Heated raw rubber is injected into a mold during injection molding. The rubber remains in the mold for a predetermined amount of time before it slowly melts into its final shape. This rubber molding process gives excellent flexibility to manufacturers to choose from a wide range of rubber products like neoprene, silicone, and EPDM.
Moreover, injection molding is mainly limited to rubber molding, but it may also be employed with various other materials, including metals and glass.
The Benefits of Rubber Injection Molding:
- Precision: The use of pressurized rubber injection, along with the excellent flow qualities of rubber, enables the raw rubber material to fill the mold and reach every corner ultimately. As a result, the outcome is quite precise.
- Excellent Mechanical Strength: The manufactured rubber parts have high strength and durability due to the pressure involved and enough curing time received during the production process.
- No finishing required: Injection molded rubber products contain fewer faults or leftover material that need finishing once removed from the mold.
- Rapid Process: Modern control systems guarantee precise heat and pressure control in injection molding equipment. Optimizing these processes can result in shorter curing cycles, giving a significant time advantage.
- Complex Geometry: This method can create shapes with unique characteristics such as holes, curvature, and sharp outlines. The mold cavity design is highly adaptable, and it can include elements such as cores to enable complicated features in the rubber part.
- Budget-Friendly: Aside from the initial tooling costs, the molding cost per item is relatively modest. So if you’re opting for rubber molding for mass production, it may be the most profitable method.
Disadvantages of Rubber Injection Molding:
- High Processing Cost: The tooling and molding machine are both costly. As a result, low-volume injection molding is not always financially viable.
- Material Restrictions: One disadvantage of rubber injection molding is that it necessitates strong flow qualities. Because not all rubbers have the required qualities, raw material alternatives are limited to flexible, liquid-like rubbers such as silicone rubber, polyurethane, nitrile rubber, and so on. However, apart from raw materials, most rubber materials can be used in rubber injection molding.
Rubber Compression Molding:
When it comes to similarity, compression molding relates to injection molding as it also uses heat and pressure. But when it comes to the process, compression molding is accomplished by inserting prepared shapes of uncured rubber into the cavities of a heated mold, which is then sealed shut with hydraulic pressure. The heated cavity holds the rubber until it is molded to its final shape.
The Benefits of Rubber Compression Molding
- Low Maintenance: Because of the simple design and lack of intricate spruce networks, cleaning and repairing/polishing the mold is straightforward and inexpensive. Furthermore, it requires less time to maintain than more complex mold designs.
- No Gate Vestige: Because the mold lacks a gate, the end product lacks the gate vestige. This also improves the product’s appearance and lowers the finishing cost.
- Multiple Material Usage Ease: Compression molding can handle a wide range of rubbers because it does not rely on material flow.
- Low Cost: Due to its simple design, the tooling involved in rubber compression molding is not very expensive, and production costs fall as the volume of production increases.
Disadvantages of Rubber Compression Molding:
- Dimensional Tolerance: The manufacturing precision is good in this rubber molding process. However, it still doesn’t beat the manufacturing precision of injection molding. Hence, when you opt for this process, the high curvatures and pockets may still have minor deviations due to the mold cavity.
- Lengthy Finishing: Even if there is no gate vestige, the fishing process of rubber compression molding still involves the removal of flashes and separation lines. Moreover, grinding or cutting this process requires both time and money – which adds to the cost and production time.
Rubber Transfer Molding:
This custom rubber molding process involves using a distinct rubber mold design. This process is precisely conducted by loading a measured amount of uncured rubber into a transfer pot. After the rubber is loaded, the ram is closed. Then the pre-form is pushed into the component cavity via the runner and gate system. Finally, the rubber is kept in the heated cavity for a set period to cure it into its final shape.
The Benefits of Rubber Transfer Molding
- High Cavity Count: The pre-form used in this custom rubber molding process is a simple shape that requires little preparation. As a result, the same pre-form can be reused for multiple cycles, saving time and labor.
- Tight Tolerance: This process may produce rubber-molded components with high dimensional tolerance and is ideal for producing precise part geometries.
- Large Parts: The mold design used in this rubber molding approach allows the inclusion of large cavities easily.
- Metal Bonding: A strong point of transfer molding is rubber-to-metal bonding, a highly convenient and preferable method for producing combination parts such as metal-rubber mounts.
Disadvantages of Rubber Transfer Molding:
- High Cycle Period: Unlike other procedures, rubber molding through the transfer process has a long curing time, a crucial concern in many operations.
- High Tooling Cost: The mold includes extra elements such as the pot and spruce. These make design and manufacturing more difficult. In addition, the intricacy raises the initial setup cost.
- Finishing: Because of the spruce, deflashing is always required during the transfer molding process to achieve a complete and ready-to-use rubber product.
Types of Rubber Materials You Can Use for Rubber Molding:
When it comes to materials, the rubber sector is far more diverse. Each rubber type has unique properties that make it suitable for particular uses. This section will go through some of the most common forms of rubber:
- Natural Rubber (NR): Natural Rubber is a well-balanced collection of qualities that is extracted from rubber trees by a process known as lapping. It features a high stretch ratio, excellent strength, and resilience and is water-proof. Its raw form, better known as Latex, is widely utilized in the Rubber business, alone or in combination with other compounds. In addition, this type of rubber is also commonly used in various types of rubber molding processes.
- Styrene-Butadiene Rubber (SBR): SBR is a synthetic rubber with exceptional abrasion resistance. It is suitable for various applications due to its durability, compression set, and water swell resistance. This type of rubber is also popular for usage in various custom rubber molding processes.
- Neoprene Rubber: Neoprene Rubber is a synthetic rubber. It is well-known for its ability to retain mechanical qualities across a wide temperature range, making it ideal for applications such as motor fluid tubing and friction belts. Moreover, its strong chemical stability and corrosion resistance make this rubber suitable for the rubber molding process.
- Nitrile Rubber (NBR): NBR is a high-performance rubber with high compression and mechanical strength. It also resists chemical degradation when exposed to typical machinery fluids such as oil and gas, allowing it to be used in sealing components.
- Butyl Rubber (IIR): IIR is a type of rubber well-known for its flexibility and gas impermeability. Because this is an unusual mix of rubber products, sealant firms greatly value this type of rubber.
- Fluoroelastomer Rubber: This rubber type has a high resistance to fluid permeability, such as water, oxygen, and ozone.
- Silicone Rubber: Silicone rubber has several advantageous qualities. Some characteristics include biocompatibility, fire resistance, ozone impermeability, and color availability. All these advantages make silicone rubber one of the most opted rubbers used in various types of rubber molding approaches.
Choosing the Right Material for Rubber Molding
You may wonder how to select a rubber substance for custom molding processes. The result determines the choice of rubber material, like rubber molding technology. Hence, when making the decision, it’s essential to consider the following:
Ø Rubber Material’s Properties:
When selecting a rubber material for a product during custom rubber molding, consider the multiple properties of the rubber. These properties can include strength, durability, abrasion resistance, impermeability to particular fluids, temperature-bearing capabilities, etc.
Ø Product’s Industrial Usage:
Material selection in different rubber molding processes might vary greatly depending on the final product’s applications. There are rubbers explicitly designed for high temperature, high humidity (not only water but any fluid), chemical exposures, loading type, and total mechanical stress. So it’s crucial to consider rubber products’ industrial usage before making any production decision.
Ø Your Budget:
Your budget is crucial when selecting a rubber material. Some are more expensive with additional benefits, while others are less expensive but significantly lower in quality. Either way, there is always a trade-off between price and quality, and you shouldn’t overlook these factors.
Conclusion:
That’s all to our detailed guide on the rubber molding process, the types of rubber molding processes, and picking the suitable types for your production needs. Of course, if you’re still stuck somewhere, you can always trust professional manufacturers like Prototool to help you proceed with the rubber molding process as per your manufacturing demands.