Anyone planning to adopt the MIM technology may be curious to explore ‘what is metal injection molding.’ Being a modern technology, MIM is an ideal solution serving as metal manufacturing technology. In addition, this technology is relatively standard among the advanced and updated metal manufacturing factories and businesses out there.
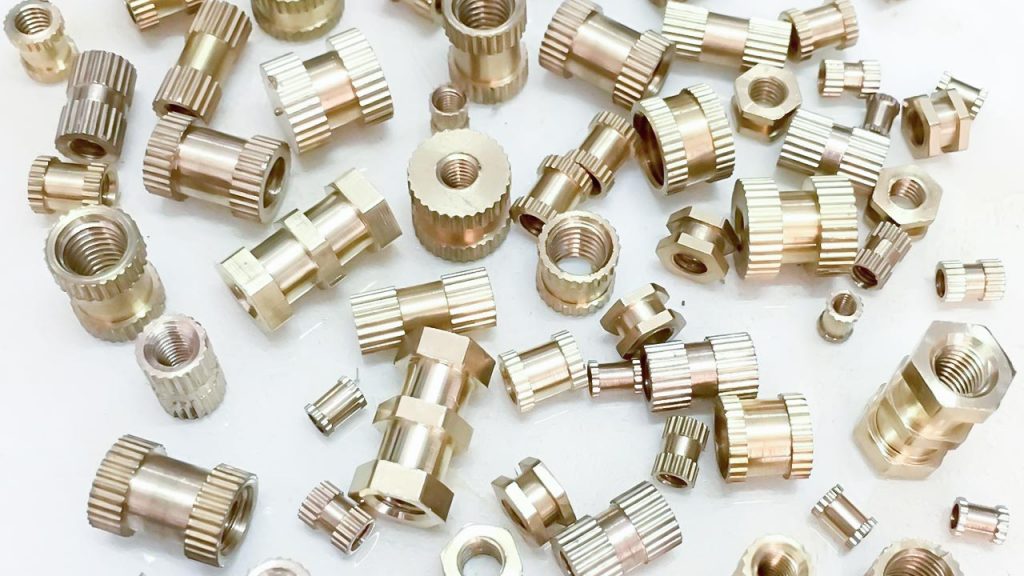
Fortunately, with plenty of unique capabilities and design aspects offered by the MIM, it serves as an ideal metal manufacturing machinery that can be used in today’s high-demanding and quality-focused fast-paced industry metal industry.
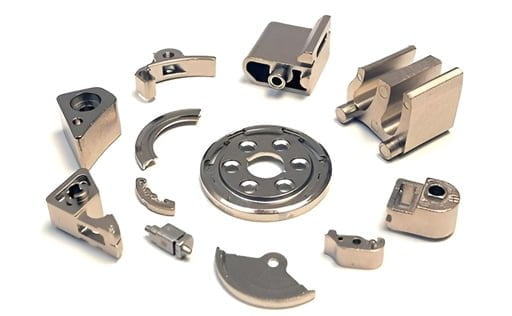
Now let’s dive into the details of the metal injection molding technology’s guidelines for a more precise overview of how it works and what makes it exceptional.
Definition: What Is Metal Injection Molding?
The metal injection molding machine is a type of metal manufacturing technology that is used nowadays as a form of advanced metalworking technology. To be more precise, this technology is ideal for the mass production of complex-shaped metallic parts. This is done with the usage of metal powders in the process of metal manufacturing.
These powders are combined with organic binders with the help of injection molding technology. Afterward, the machine successfully ends up producing complex structured metal components using this working method by molding the forming the metal feedstock into the desired shape.
Once the highly complex structured metal components are produced, the machine then subsequently processes and centers the parts on sintering them into pure metal products. In this way, they become capable of yielding high strength through their intricate shape – making them quality metal parts.
With the efficient and time-saving metal manufacturing method promoted by a metal injection molding machine, the machine’s simplified production and its complex metal parts are used in both large-scale metal industries and a wide-scale manufacturing market. Ranging from the aerospace market to medical, electronics, agriculture, automotive, and many other large-scale and high-in-demand markets utilize MIM parts today.
In a nutshell, it can be evidently said that metal machine molding technology is one of the significant manufacturing equipment and methods used in advanced and complex metal product development. And hence, the demand for this machine in the metal injection molding market is also quite extensive in its relevant manufacturing industries and markets.
Metal Injection Molding Process:
Although we have discussed how the basic process of the metal injection molding machine works, it’s essential to be well aware of the detailed guideline before you invest in this technology. Besides, like any other manufacturing machine, the metal injection molding process is also focused on a particular guideline.
Hence, gaining efficiency and specific outcomes from this machine is only possible if you use it accordingly.
What to Consider?
Firstly, let’s start with understanding what needs to be considered when using MIM technology. While the usage and process may seem simple and easy, it isn’t always the case.
Instead, the metal injection molding process is mainly focused on certain aspects that, once considered, only then the process of complex structured metal production can be efficient and quality-based.
As shown in the image below, this process includes:
- Material Performance: The capability and the quality of the materials/powders you are using in the metal injection mold process.
- Shape Complexity: What type of complexity in the metal parts do you demand or desire for further accompanying your targeted production market, i.e., agriculture or aerospace, etc. Varying on this factor, you can analyze what type, size, and model of the MIM machine is ideal for your metal production business – and whether it’s cost-efficient in the end or not.
- Component Cost: the cost of the components and the overall business/manufacturing budget that you hold. Do they match, or are they affordable or not?
- Production Quantity: Once again, is the type of MIM machine you are purchasing capable of handling the production quantity of your business/company or not?
The Process Of Metal Injection Molding:
Once you’re done analyzing and asking yourself whether you are ready to become another competitive and top-rated metal injection molding company for metal production and considered it a sure-short ‘YES,’ it’s time to move on to the next step, i.e., the working of the metal injection molding machine.
As one of the metal injection molding companies, it’s essential to be well aware of the technical issues and/or complications that you may need to consider before you begin applying the process of metal injection mold industrially. To avoid these complications, you should ensure that:
- The viscosity of the homogenous powered-binder mix should be sufficient for the metal injection molding process.
- The economical binder removal method should be able to provide debinded geometry retention of the parts.
- The MIM machine is able to handle the sintering process on high-density metal parts while offering high dimensional accuracy too.
Once you can ensure that any technological complication doesn’t affect the above-mentioned aspects of metal production, you are ready to use the MIM technology.
The primary process of using this technology efficiently involves:
Step 1: Feedstock Preparation
The first step is to prepare the feedstock, which is mainly the combination of raw materials that are later used for metal injection molding. The feedstock comprises a composition of thermoplastic binders and metal powders.
During this process, the properties present in the metal powders are what mainly determine the properties of the final metal injection molded products. In contrast, the binder is used to inject the molding, which is later removed from the final products after the MIM injection molding is completed.
In a nutshell, it is the metal powder that remains in the metal parts that are products in the end.
When preparing this MIM feedstock, its granulation size is considered several millimeters. To make the process straightforward and quality-focused, you can purchase the feedstock from reputable metal injection molding companies that manufacture this machinery, like the Prototool.
In this way, you can maintain quality and assurance of the ideal properties of the feedstock for the metal parts production process.
Step 2: Metal Injection Molding Process
This second phase of the metal injection molding process is quite similar to the one of plastic injection molding. Using the feedstock, you can operate the MIM technology to produce a variety of geometrical metal parts.
Once the process is completed, the machine ends up forming green MIM parts, likewise to the forming of plastic parts.
Step 3: Debinding
In this process of using a metal injection mold technology, various methods are utilized to remove the binder materials from the metal parts or injection molded MIM parts, as mentioned earlier.
As the parts are green in color and in their initial stage, the debinding process or easier to perform. Afterward, an interconnected pore network that doesn’t involve any geometry destroys these binder components, resulting in a yellow color outcome of these MIM parts.
While this debinding process removes most of the substantial binder material, some of it still remains in the parts. This remaining binder material holds the metal powders together. However, in the initial phase of sintering (the next step), the residual binder material starts to evaporate from the pores of metal parts.
In contrast, the sintering neck starts growing between the metallic particles to maintain the geometrical structure of the parts consistently.
Step 4: Sintering
Last but not least, in this process, most of the pore volume that the binder material occupied will be eliminated. As a result, the yellow metal injection mold parts will start shrinking at a linear rate of 15%-20% as soon as the sintering process completes.
In the end, the sintered parts are fully prepared to be processed by conventional metalworking methods, similar to the ones used on the cast, wrought, and forged metal parts, to attain a particular final finishing as desired for usage and supply in different types of metal injection molding markets that use the MIM parts.
The Advantages of Metal Injection Molding Technology:
Lastly, before we conclude this article, let’s explore some sure-shot benefits that metal injection molding companies avail of using this efficient metal-producing technology. These benefits specifically include the following:
- Unique Capability: The MIM machine is able to offer smaller size, higher geometry complexity, higher strength, higher surface finish, and higher dimensional tolerance in all of its parts – making them ideal for usage in different types of advanced and complex metallic markets and machinery.
- Cost-Efficient Process: The MIM machine itself avoids demanding high-cost machining operations, making the overall processes conducted by the machine to be competitive and budget-friendly.
- Modern Performance: With the new designs available in the metal injection molding machinery, the machine and its technology are now capable of combining multiple parts. The machine then assembles these parts into one single component – making it ideal for the more complex and large-scale metal equipment demanding markets like agricultural, aerospace, etc.
Conclusion:
That’s all to our detailed guidelines on the basics, usage, and advantages of a MIM machine. If you have any further queries, we are always available to help you out.