CNC machining is a digital manufacturing technology that can create precise products from CAD files. However, the processing cost varies and can impact the entire project budget. To make CNC machining cost-effective, investigate the factors that influence CNC processing, including the CNC parts cost.
Factors that impact the CNC parts cost include the complexity of the part, the material used, required tolerances, machining operations, and order quantity. Early consideration of these factors can help reduce costs without sacrificing quality. In the next section, we’ll explore how you can optimize each factor to lower the CNC parts cost.
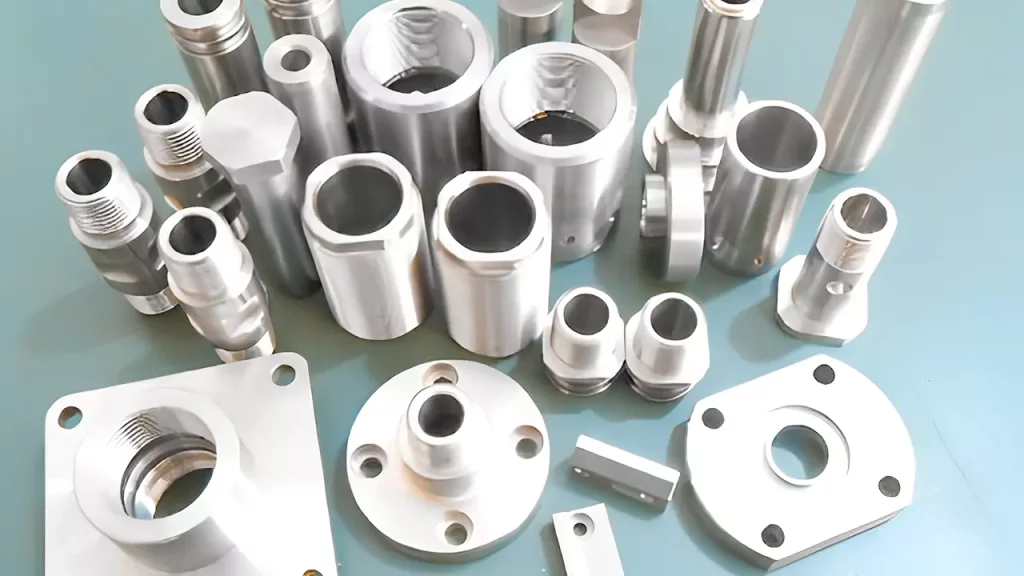
Understanding What Increases the CNC Parts Cost and How To Reduce It:
The Machinery:
Several different machining processes, the majority of which are executed on CNC lathes or CNC milling machines, including drilling, boring, turning, and milling. At a time when productivity is of the utmost importance, extremely modern CNC machines allow for the production of parts at a lower cost than that modern machines.
Nevertheless, the tool’s cost also affects the equipment’s overall cost, and the tool’s material, coating, and geometry are all essential aspects. Carbide tools, for example, are more than twice as expensive as steel tools but are far more durable, heat-resistant, and able to handle severe speeds.
One further thing to remember is that operations can be made more complicated by using more sophisticated moving parts, making the system more difficult to set up, operate, and maintain. Consequently, such machines also have a higher price tag, contributing to the overall expense of the CNC parts during production. Therefore, it is preferable to steer clear of such pricey machinery as much as possible, particularly milling machines.
Machinery Setup:
The cost will include not only the machines themselves but also the labor required to set them up. The expenses incurred before machining are known as “setup charges.” The first step in producing any CNC machined component is always a 3D model. A professional designer makes the 3D model with CAD (Computer Aided Design) software.
A sizeable chunk of the initial investment goes toward the time and materials needed to develop a 3D model of the manufactured good. In addition, there are expenses involved in setting up the model for CAM (Computer Aided Manufacturing), such as optimizing the design.
Parts Design and Geometry:
Another crucial factor that affects the CNC parts cost is the design and geometry of the part. The part geometry and design strongly impact the expenses associated with CNC machining. The more complicated the part, the greater the manufacturing cost since the production process will require more advanced technology, additional machining time, several passes and different setups, additional resources, and more thorough inspections.
When it comes to CNC machining, the characteristics, and designs of specific items, such as sharp inner corners, thin walls, deep cavities, non-standard hole sizes, and writing, invariably lead to increased costs. If possible, it is in your best interest to avoid cost-effective features like these, including the ones you’ve just seen. Additionally, certain design parameters, such as surface roughness or tolerance options, can need numerous passes and inspections, resulting in additional expenses.
In addition, larger parts will have a higher cost associated with their production. After all, larger parts will need a greater investment of time, raw materials, and other resources.
In such situations, you can reduce the CNC parts cost by:
Eliminating Unnecessary Features
Eliminating unnecessary features, such as sharp interior corners, not only helps conserve material but also decreases the time spent on CNC machining since the workpiece is simpler, ultimately resulting in savings in the entire production cost! Before beginning any project, double-check that this consideration has been incorporated into your ideas!
Analyzing Geometric Features
Knowing the geometric features of the parts you’re working with will help you identify the appropriate tolerances for each component, reducing the size of those parts without sacrificing quality in most instances. Thoroughly analyzing these features helps guarantee that your products meet all of the relevant specifications while also saving money on the CNC machining costs connected with those features.
Using CAD/CAM Software
CAD/CAM programs may dramatically simplify shapes while keeping accuracy due to their capacity to build 3D models with fewer points. This feature allows us use the software in the design process. This results in a lower overall cost for machining thanks to the decreased time spent programming tool motions and the shortened tool paths produced due to the increased efficiency.
Minimizing Part Markings
Adding excessive markings or logos to components can lead to longer CNC machining times and directly impact the associated cost. While certain components require specific identification markings, it is important to avoid an excessive number of markings to minimize the complexity of tool paths. Therefore, you should try to use minimal markings wherever it is possible to do so.
Reduced Manufacturing Volume:
The price per component of a large batch of identical parts drops dramatically as the quantity of those parts grows. Completing the CAD design, CAM preparation, and machine setup only once reduces the overall manufacturing cost per part proportionally.
Choosing The Right Production Material:
One of the most important factors determining costs is the material utilized in producing the parts. The materials cost is the essential factor, which frequently depends on their availability, optimum performance, and overall manufacturing costs. The second most important factor is the perfect performance of the materials. Metals, in comparison to other types of materials, are often more expensive.
Now employing materials with low machinability requires additional time and effort to machine, and time is money in the CNC machining industry. The amount of time required to machine a component directly correlates to the associated cost of doing so. Materials that are difficult to machine use more resources, such as cutting fluids, electricity, and cutting tools, than materials that are easier to process.
In such situations, you can reduce the CNC parts cost by:
Choose the Appropriate Tooling and Fixturing
Choosing the appropriate tooling and fixturing can also help reduce the associated costs with each project. This is because tooling and fixturing are relatively inexpensive compared to the costs of materials, machine setups, or special materials, all of which will cost you more. However, the machine shop should ensure that these fulfill the requirements outlined in the component specification to avoid any unpleasant shocks during manufacturing!
Choose Less Expensive Alternatives
Many raw materials used for CNC machined parts, such as steel and aluminum, have cheaper alternatives available in the form of alloys which typically have similar properties but lower cost – opting for these instead can help reduce CNC machining costs without negatively impacting performance in the majority of cases.
Maximizing Material Utilization
To significantly reduce the cost associated with CNC machining, maximize material utilization in component design. Producing more components from a given quantity is possible by minimizing the waste of raw material. Considering this factor before starting any project leads to substantial savings.
Finishing Phase:
CNC-machined components are ready for use after completion. However, post-treatment processes like heat treatment, surface treatment, and coating are necessary for specific applications and drive up the cost of the item by improving its functionality, performance, and aesthetics.
Now to reduce the CNC parts cost in the finishing phase of the part’s production, you can:
Choose Appropriate Materials
Because different applications call for different kinds of treatment or none at all, choosing appropriate materials for components also significantly reduces the costs associated with surface treatment. Before making a choice, it is crucial to carefully consider which material is most suitable for a specific endeavor.
Complete an Appropriate Component Design
Completing an appropriate component design helps reduce the costs of surface treatment CNC machined parts because some materials do not require any additional treatments – understanding the requirements of your component helps determine which treatments should be specified to maintain its integrity while keeping costs to a minimum.
Consider Alternative Finishing Methods
If a particular component needs substantial protection, consider alternative treatments such as anodizing or hardening rather than using traditional methods such as galvanizing or chroming. These options provide better protection for longer periods at a lower cost than the more common methods mentioned above.
Choose Reusability and Long-Term Performance
Considering the number of times a component will need to be reworked throughout its lifetime can significantly reduce the cost of surface treatment. This is because reworking a component requires fewer steps than starting from scratch. Thinking about this before moving forward with any project will help bring about significant cost savings in the long run.
Conclusion:
With the help of this detailed guide, you can better evaluate what leads to increase CNC parts cost and how you can handle these certain processes to reduce the overall production cost.
For more details and queries, feel free to contact us at Prototool.com.