In cosmetic packaging, molds hold a unique place, especially when it comes to the aesthetic and functional requirements of containers and lids. Among these, the molds for cosmetic cream jar lids are particularly prevalent. This article delves into the detailed mold design for cosmetic cream jar lids, exemplified in Figure 1. The lid, with its maximum dimensions of ø65.66 mm X 12.90 mm and an average wall thickness of 2.31 mm, weighs 14.7 grams. Made from ABS material with a shrinkage rate of 1.0055, it’s imperative that the final product is free from defects like weld lines, bubbles, deformations, color variations, flash, and other injection molding flaws.
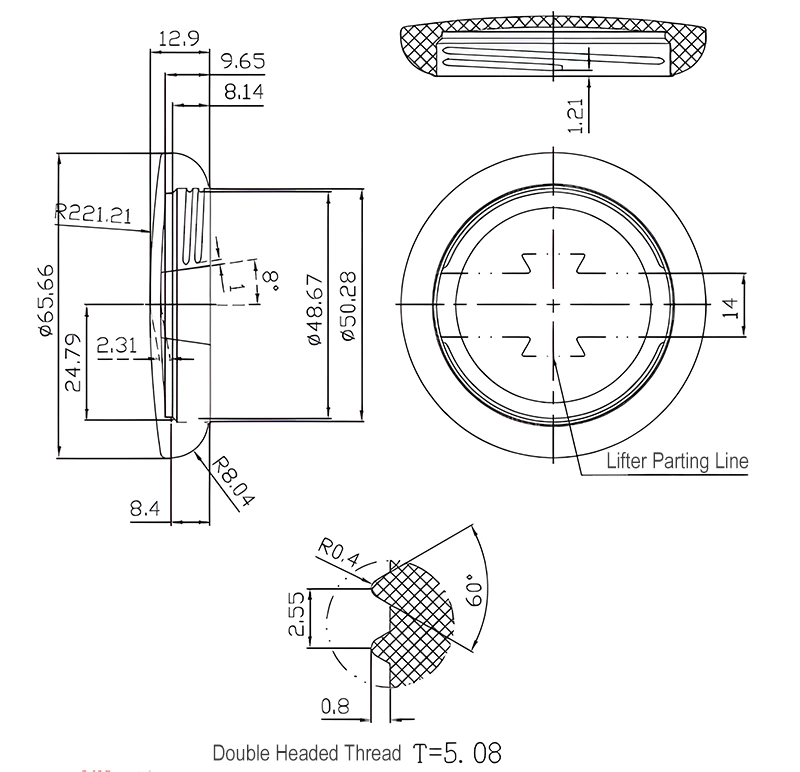
Key Considerations in Cosmetic Mold Design
The design of cosmetic cream jar lids in molds requires meticulous attention. A critical aspect is the appearance of the plastic part. Any small gate marks should be strategically placed, preferably on the back of the product or inside the lid, concealed by liners or other components. The aesthetic features, such as ribs, logos, and other decorative elements, must be visually appealing. The surface should have uniform etching patterns, and polished surfaces must be free from reflective waves or defects. Control the parting line differences to below 0.03mm to ensure sharp angles and consistent radii at corners. During injection molding, strict standards must be in place to control defects like black spots on the surface.
Mold Design for Cosmetic Cream Jar Lids
Cosmetic cream jar lids are often circular, with some based on modified circular designs. A notable characteristic of these parts is their small size, often featuring internal threads. Multi-start threads are commonly used for their quick opening and closing, requiring less than two turns to tighten or loosen. Material selection is crucial for achieving the desired texture, sometimes necessitating thicker wall sections in certain areas.
Given the high market demand for cosmetic cream jar lids, the production volume is substantial, leading to the design of multi-cavity molds. Current technology allows for 2 to 124 cavities per mold. The mold design presented here features 8 cavities arranged in two rows in a straight-line configuration, as illustrated in Mold Design Figure 2.
Advanced Features of the Cosmetic Cream Jar Lid Mold
The mold structure, as seen in Figure 1, features a curved top surface and a circular arc-rotating surface on the side. The internal threads are discontinuous, designed as double-start threads. Due to the size and structural characteristics of the part, these threads require an angled lift for demolding. The mold uses a three-plate mold system with point gates and is an inverted mold structure. The mold base is a non-standard 4050, with four stages of parting. Secure each stage with screws to limit movement during the molding process.
The mold opening process for a three-plate mold involves several steps. The first step separates the runner system from the part. Subsequent steps involve stripping the runner material from the pins and separating the sliding blocks for demolding the double-start threads. The final step opens the parting line to eject the part.
Another characteristic of the cosmetic cream jar lid mold is the small diameter of the circular cavity. To enhance mold life, the cavity material is heat-treated to above HRC50. For multi-cavity molds, it’s crucial to maintain high precision in cavity processing, keeping dimensional tolerances within 0.015 to ensure interchangeability. The machining precision of the mold base is also critical, with center distances between cavities controlled within ±0.015.
Each cavity requires a designed cooling circuit, using high-temperature seals to prevent leakage during injection. The cooling circuit in circular inserts is typically located around the circumference or on the top, ensuring uniform cooling.