El moldeo por inyección es una tecnología de fabricación común y adaptable que permite a las empresas generar producción de gran volumen funciona a un coste barato por pieza sin perder calidad. Es extremadamente reproducible y capaz de crear componentes resistentes que cumplen especificaciones mecánicas y dimensionales precisas. Moldeo por inyección de pared delgada puede utilizarse cuando una empresa tiene que fabricar una pieza de plástico con paredes finas, como ciertas piezas de automóvil o carcasas de teléfonos móviles. Aun así, debe extremar la precaución cuando desarrolle productos con paredes finas, ya que el moldeo por inyección de paredes finas presenta obstáculos adicionales.
En este artículo, repasaremos los fundamentos del moldeo por inyección de pared delgada, sus aplicaciones más comunes y algunos consejos de diseño de moldeo por inyección que le ayudarán a garantizar que sus productos de plástico corporativos de pared delgada se fabrican a la perfección.
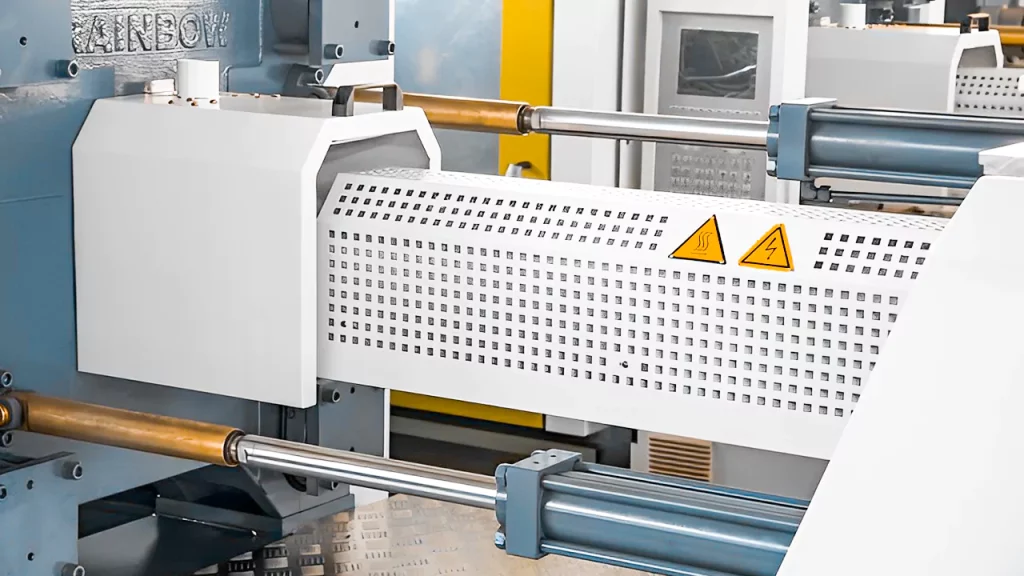
Breve descripción del moldeo por inyección de pared delgada
El moldeo por inyección de pared delgada es un subconjunto del moldeo por inyección convencional que se centra en la producción en masa de piezas de plástico delgadas y ligeras para ahorrar dinero en materiales y mantener la duración de los ciclos lo más corta posible. La reducción de la duración de los ciclos implica un aumento de la producción y un abaratamiento de los costes por pieza.
La definición de pared delgada se refiere al tamaño de la pieza en relación con su espesor. La fabricación de cualquier objeto de plástico mediante la técnica de moldeo por inyección es más difícil a medida que disminuye el grosor de la pared. El tamaño de una pieza limita la cantidad de grosor de pared que puede utilizarse. En el caso de los envases, una pared fina significa menos de 0,025 pulgadas (0,62 mm) de grosor de pared con una relación longitud de flujo/grosor de pared superior a 200.
Esta técnica de moldeo por inyección incluye plazos de entrega más cortos y tiempos de ciclo más rápidos debido a que hay menos material que enfriar. De hecho, una gran reducción del grosor de las paredes puede reducir a veces los tiempos de ciclo a la mitad, lo que permite a las empresas poner los productos en manos de los clientes con mayor rapidez y ahorrar dinero en costes operativos.
Ahora, las paredes más finas también implican menos plástico, lo que significa que su organización puede ahorrar dinero en materiales y ofrecer más espacio libre para el producto en envases y embalajes. Sin embargo, el moldeo por inyección de paredes finas tiene algunos inconvenientes. Por un lado, el proceso de inyección es más difícil. Se necesita más presión y velocidades de moldeo más rápidas para llenar las delgadas cavidades con material fundido, evitar la congelación y garantizar que el artículo salga correctamente.
Ventajas del moldeo por inyección de pared delgada
Aunque la elección del método de fabricación de moldeo por inyección de pared delgada conlleva múltiples ventajas, algunas de las principales de este proceso son:
- Componentes de plástico de bajo coste, seguros e higiénicos.
- El moldeo de paredes finas ahorra recursos y disminuye el peso, lo que reduce el consumo de combustible y las emisiones de carbono en el transporte y contribuye a los esfuerzos de sostenibilidad.
- En las aplicaciones automovilísticas, las piezas más ligeras reducen las emisiones de combustible.
Moldeo por inyección de pared delgada: Consideraciones importantes
Consideración de la maquinaria ideal:
La maquinaria de moldeo estándar moderna cuenta con capacidades avanzadas que superan las de hace una década, lo que las hace adecuadas para una amplia gama de aplicaciones de pared delgada. Las capacidades integradas en las máquinas estándar modernas superan con creces las de hace diez años. Los materiales, la tecnología de inyección y las mejoras de diseño amplían aún más la capacidad de una máquina típica para llenar piezas más finas.
Sin embargo, a medida que disminuye el grosor de las paredes, puede ser necesaria una prensa más especializada con mayor velocidad y capacidad de presión. No es raro que un componente electrónico portátil de menos de 1 mm de grosor tenga tiempos de llenado inferiores a 0,5 segundos y presiones de inyección superiores a 30.000 psi. Los acumuladores se utilizan a menudo en el moldeo de paredes delgadas máquinas hidráulicas para accionar los ciclos de inyección y sujeción. También se están comercializando modelos totalmente eléctricos o híbridos eléctricos/hidráulicos con capacidades de alta velocidad y presión.
Además, en este proceso, la fuerza de sujeción debe ser de al menos 5-7 toneladas/pulgada cuadrada de área prevista para soportar las altas presiones requeridas. Asimismo, las platinas extrapesadas reducen la flexión cuando disminuye el grosor de las paredes y aumentan las presiones de inyección. Las máquinas de pared delgada suelen tener una relación entre la distancia del larguero y el grosor de la platina de 2:1 o menos. El control en bucle cerrado de la velocidad de inyección, la presión de transferencia y otras variables del proceso también puede ayudar a conseguir llenar y envasar con paredes más finas a altas velocidades y presiones.
Además, los cañones grandes tienden a ser demasiado grandes en cuanto a capacidad de disparo. Recomendamos aspirar a un tamaño de disparo de 40% a 70% de la capacidad del cañón. El tiempo de ciclo total considerablemente reducido que se encuentra en las aplicaciones de pared delgada puede permitir una reducción de 20%-30% en el tamaño mínimo de disparo, pero sólo si las piezas se evalúan adecuadamente para la pérdida de propiedades debido al probable deterioro del material.
Dicho esto, los operarios de las máquinas deben tener cuidado, ya que los tamaños de granalla pequeños pueden hacer que la sustancia permanezca más tiempo en el barril, lo que provocaría una degradación de las propiedades.
Selección de los mejores materiales:
A la hora de decidir qué material utilizar para su pieza, recuerde que el material adecuado depende de la geometría de su pieza y de las necesidades de su aplicación.
Algunos materiales, como los termoplásticos:
- polietileno de alta densidad (HDPE)
- polietileno de baja densidad (LDPE)
- polipropileno (PP)
- nylon, fluye suavemente por zonas finas (PA)
Ahora bien, todos ellos son productos ideales para piezas con una bisagra viva, una sección delgada que debe doblarse. Otra sustancia termoestable es el caucho de silicona líquida (LSR), que se llena con extrema facilidad, tanto que puede suponer un riesgo de flash en las líneas de separación. Si incluimos características adicionales en el diseño del molde, podemos ayudar a evitar las rebabas.
Por el contrario, los policarbonatos son pegajosos y tienen dificultades para rellenar geometrías con paredes finas. El grosor de las paredes de las porciones debe tenerse en cuenta a la hora de decidirse por un material.
Sugerencias de diseño:
He aquí una lista de consejos a tener en cuenta a la hora de desarrollar y seleccionar un material para piezas moldeadas con paredes:
- En general, mantener un grosor de pared uniforme de 1,5 a 3 mm (0,060 a 0,120 pulg.) en todo el diseño garantizará que las piezas se enfríen uniformemente y evitará el alabeo.
- Considere la posibilidad de añadir refuerzos (costillas de soporte transversal) para proporcionar una pared de costilla fina más duradera sin hacer la costilla más gruesa.
- Las costillas deben tener aproximadamente 50-60% del grosor de la cimentación principal, como se indica en la foto de la derecha. Las costillas con el mismo grosor en toda su longitud pueden dejar material adicional en la base de la costilla.
- Aunque las líneas de separación (la costura donde se unen dos mitades del molde) son normales en la mayoría de los artículos moldeados, cambiar la ubicación de la línea de separación puede suponer una diferencia visual significativa. En su presupuesto se especificará la ubicación de la línea de separación, y podemos sugerirle que modifique la forma para que sea menos prominente.
- Además, la incorporación de canales de flujo con radios a geometría delgada puede ayudar a que el material fluya más libremente en costillas o secciones delgadas.
Sobre todo, el envío temprano de su archivo CAD nos permite aportar información sobre su diseño y guiarle a lo largo del proceso de fabricación por moldeo por inyección. Si prevemos algún problema con el grosor de las paredes o la geometría de los componentes en general, podemos aconsejarle cómo resolverlo lo antes posible para que reciba sus piezas acabadas a tiempo.
Consejos adicionales de diseño:
Aparte de lo básico, puede sugerir a los profesionales de la fabricación y el diseño de moldeo por inyección de pared delgada que está aquí para tener en cuenta los siguientes consejos durante el proceso:
- Para aplicaciones agresivas de pared delgada, utilice aceros más resistentes que el P20, especialmente si se prevé un desgaste y erosión considerables. Los aceros H-13 y D-2 han demostrado su eficacia en insertos para compuertas.
- Los enclavamientos del molde pueden evitar ocasionalmente la flexión y la desalineación.
- Los núcleos telescópicos pueden ayudar a reducir el desplazamiento y la rotura del núcleo.
- Debajo de las cavidades y el bebedero, utilice placas de soporte más resistentes (normalmente de 2 a 3 grosores) con pilares de soporte (normalmente precargados 0,005 pulg.).
- Para reducir el empuje de los pasadores, utilice más pasadores eyectores y de mayor tamaño que con los moldes estándar.
- Concéntrese en la disposición estratégica de los knockouts de manguitos y cuchillas.
- El pulido con diamante n.º 2 de núcleos y nervaduras puede eliminar los problemas de adherencia de las piezas. Los tratamientos de la superficie del molde, como el níquel-PTFE, también pueden mejorar el desprendimiento de la pieza.
- El venteo es crucial y puede facilitarse mediante pasadores de núcleo venteados, pasadores eyectores y venteo a lo largo de hasta 30% de la línea de separación. Los orificios de ventilación tienen una anchura aproximada de 0,200 a 0,0400 y una profundidad de 0,0008 a 0,0012. Aunque normalmente no es esencial, algunos procesadores han utilizado una junta tórica para sellar la línea de separación y hacer el vacío en la cavidad para una rápida evacuación del gas.
- Cuando aumentan las velocidades de inyección, las compuertas con paredes más grandes que las nominales ayudan a reducir el cizallamiento del material y el desgaste de la compuerta, a la vez que evitan la congelación antes de que se alcance el empaquetamiento adecuado.
- Los insertos de compuerta con una dureza Rockwell (Rc) superior a 55 se emplean habitualmente para soportar altas presiones de inyección.
- Utilice los pozos de inyección para reducir la tensión en la inyección, ayudar al llenado y reducir los daños en la pieza al delegar cuando se inyecta directamente en una pared fina con un bebedero, punta de alfiler o gota caliente.
- Los colectores calientes pueden ayudar a reducir la pérdida de presión en los sistemas de canalización, pero requieren canales interiores con un diámetro mínimo de 0,5 pulgadas y sin esquinas afiladas ni zonas muertas. En los colectores deben utilizarse calentadores externos en lugar de interiores. Si se utilizan compuertas de válvula, deben ser no restrictivas y estar diseñadas para soportar altas presiones.
Resumen
Los componentes de plástico de pared delgada tienen una gran demanda en todo el mundo debido a su durabilidad, tiempos de ciclo más rápidos y menores requisitos de material de origen. En el proceso de moldeo de pared delgada, los plásticos pueden satisfacer la mayoría de las demandas de los clientes. El moldeo de plásticos de pared delgada es una de las tecnologías clásicas de moldeo por inyección utilizadas para crear plásticos de bajo peso, resistentes, fiables y rentables.
Con moldeo por inyección de pared delgada cada vez más popular en todas las industrias, es hora de que lo tenga en cuenta también para las necesidades de fabricación de sus productos.