Lorsqu'il s'agit de tooling, there is no room for error in the smallest of details. However, with the large number of factors that have the potential to influence production, it’s easier to avoid mistakes if you are fully aware of every process and its detail. Speaking of which, mold flow analysis is a critical component of the manufacturing process. Now, to better understand it, let’s dive in and find out how to mitigate the risks associated with developing a new mold during the mold flow analysis process.
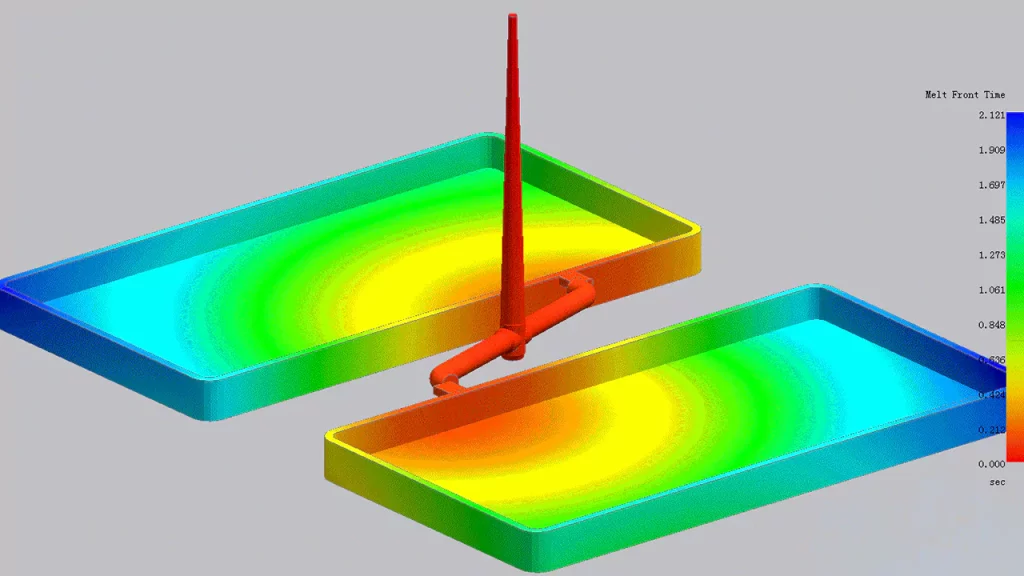
What Exactly is Mold Flow Analysis?
Mold flow analysis is a technique that involves simulating an injection molding cycle with a specific type of plastic and then evaluating the results. Prior to injection molding, moldflow analysis is essential. It involves using specialized software to simulate the design of the component. This should happen. Because the liquid material flows inside the mold significantly impacts how the finished product behaves, this process can help save a lot of time and effort in the long run.
The software generates color maps mirroring design features as they appear in mold flow. It includes features like heating and/or cooling, fill pattern, pression d'injection, potential air traps, shear stress, fiber orientation, and a variety of other features. Mold flow analysis is a meticulous and hands-on process reserved for professionals only.
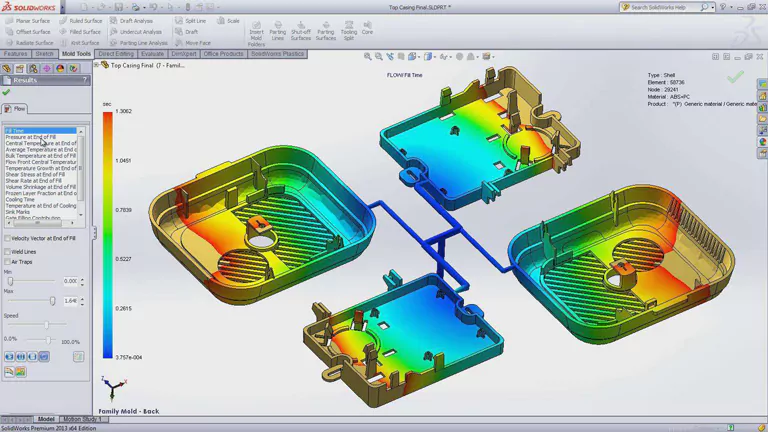
It’s All About the Method:
Moulage par injection is much more involved than simply creating the item and relying on a pre-existing mold to produce goods identical to the design. This may result in certain flaws, which will impact the overall quality of the finished pieces. Moldflow analysis, on the other hand, reduces the likelihood of something like that happening.
A moldflow analysis is used to analyze the design, which generates color maps depicting the various features present in the real mold flow. These parameters include injection pressure, fiber orientation, air bubbles, temperature, and temperature change. The designers can use color maps to adjust the design of the pieces they are creating before beginning the molding process.
When Should a Mold Flow Analysis Be Used?
As you may have deduced from the preceding explanation, the moldflow analysis is performed before the tooling process. It is done so that potential problems or technological flaws can be identified before resources, including time and money, are wasted on producing the final product. It ensures top-quality finished products and minimizes resource wastage in manufacturing. The program can evaluate different outcomes by varying factors such as temperature and pressure.
Professionals like Prototool employ this method to prevent wasteful production and ensure timely order fulfillment. It saves time and eliminates wastage by assessing production viability upfront.
What Are the Benefits of Conducting a Mold Flow Analysis?
Mold flow analysis has numerous benefits for businesses and the end users of the products manufactured by such companies. Take a look at the following list, which details the numerous advantages:
1. Optimize the Position of the Gate:
Any injection molding process must include gate location as an essential step. The gates are the critical points at which the molten plastic enters the mold, where it must cool before producing the finished goods.
If the gates are not correctly positioned, the mold portions are not filled with molten plastic. This can be caused by incorrect gate alignment. If the gate were in the wrong place, the distribution of molten plastic would be uneven, resulting in the production of faulty goods.
On the other hand, Moldflow analysis ensures that gate location can be optimized using plastic flow analysis. Consequently, you can determine the proper place for each gate in your mold and ensure that the molten plastic fills the mold evenly.
2. Identify Potential Issues in Components:
Corrections to an incorrectly designed product may be prohibitively expensive. If not identified, it has the potential to cause costly product flaws. The same components must be recreated from scratch multiple times to produce many defective items, increasing production costs. Moldflow analysis can predict where defects will appear in the production of parts before they occur. As a result, you can correct any flaws before the products are manufactured.
3. Prepare for the Fill Patterns:
Moldflow analysis can identify and anticipate fill patterns and locate the appropriate gate position. Because of the ability to predict fill patterns, design engineers can simulate the flow of molten plastic into a mold. As a result, it allows them to preview the finished product’s appearance before it is manufactured.
Engineers can use plastic flow analysis to make accurate predictions of fill patterns and redesign more efficient molds.
4. Design Modifications:
Mold flow analysis can help keep errors and mistakes to a minimum during conception de moules. As a result, it is possible to produce highly high-quality items. As a result, you’ll be able to create a wide range of brand-new designs. Finding new adjustments and solutions is another simple way to facilitate design enhancements for your project.
5. Enhance Overall Product Quality:
The mold flow analysis is a valuable tool for engineers who want to improve the overall quality of their own products. By forecasting the flow of molten plastic, design engineers can make changes to designs to increase output.
The injection molding procedure allows for the production of a large number of high-quality goods. Engineers can thus use moldflow analysis to maintain efficiency and streamline the injection molding process. As a result, there will be fewer opportunities for errors, and the overall quality of the output will improve.
6. Shorter Lead Time:
The term “lead time” refers to the time that elapses between the start of the injection molding process and the point at which the finished product is ready for distribution to customers. Hence, moulage par injection must opt for a shorter lead time to satisfy customers’ needs and manage the high-volume market distribution of important plastic assembly components.
A variety of factors can influence the lead time. The most common type of flaw occurs during the injection molding process. On the other hand, Moldflow analysis can reduce lead time by allowing for the early detection of potential problems before the start of actual production.
7. Determine the Shrinkage
Companies specializing in injection molding must know the resin shrinkage. This is because the plastic material undergoes temperature changes ranging from high heat to rapid cooling. The majority of items shrink during the cooling process. As a result, you need to have the know-how of mold flow analysis cooling to determine the rate of shrinkage experienced by each material.
Injection molders can determine the rate of shrinkage by using moldflow analysis. Moldflow analysis measures shrinkage rates for all plastic types, including thermoplastics, thermosets, and others. It applies irrespective of the raw material used in plastic production. As a result, manufacturers can use this data to decide the type of resin to use concerning the raw material used and the rate at which their goods shrink.
Do you Perform Mold Flow Analysis on Every Product During the Manufacturing Process?
Only in some cases, moldflow analysis should be used in various ways and at multiple times depending on different criteria. These factors include the product’s scale and geometry, which refers to how intricate the design is. Furthermore, the product geometry comprises the dimensions of the product. Obviously, if the component being tested is simple, has been completed previously, or is required in a low volume, it may not be worth investing the necessary time, software, and human capital to execute the tests.
Furthermore, manufacturing company employees frequently work with different materials. This familiarity allows them to mold these materials even without the specific tool, as they are knowledgeable about the parameters governing each material. On the other hand, the technology will benefit any products that use unusual materials or designs, allowing manufacturers to predict and secure favorable outcomes for their creations more accurately.
Conclusion
Mold flow analysis is used to make the most of available resources and create the best products. This improves the entire injection molding process, and if producing long-lasting products is the goal of the molding process, its benefits are unavoidable. As a result, this article discussed moldflow analysis regarding how it works, its uses, and how it can improve your design. This article has explained that mold flow analysis is one of the most essential processes in injection molding. As a result, to achieve the best possible outcome, designers must incorporate it into their process.