Vous craignez de passer à côté de certains des défauts de moulage par injection les plus courants au cours de la production ? L'une des approches les plus bénéfiques pour la production de composants consiste à moulage par injection. Parmi les avantages, citons la productivité élevée, la rapidité de production, l'adaptabilité à différentes tailles et formes et l'automatisation des procédures. De plus, les dimensions des produits moulés par injection sont souvent constantes. Cependant, plusieurs défauts de moulage par injection menacent encore la qualité des produits.
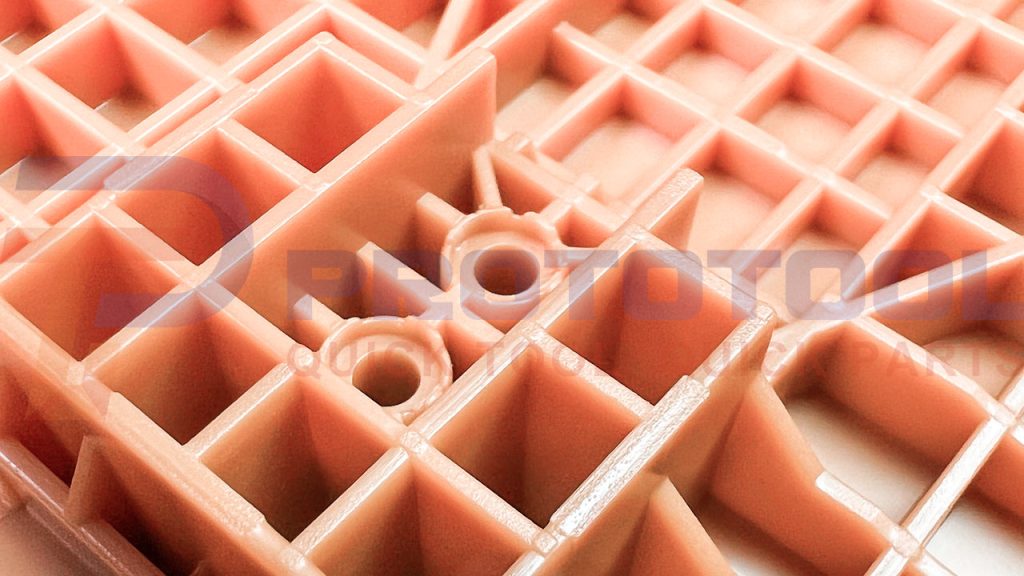
Cet article met en lumière les nombreux défauts des pièces moulées par injection et les facteurs qui contribuent à leur apparition. Il clarifie également les nombreuses solutions que vous pouvez mettre en œuvre pour éviter que ces défauts de moulage par injection n'affectent la qualité du produit.
Défauts de moulage par injection les plus courants :
1. Marques de brûlure :
L'un des défauts les plus courants du moulage par injection est la "brûlure". Sur les pièces en plastique moulé, les marques de brûlure sont des décolorations noires ou de couleur rouille. Les marques de brûlure n'affectent pas l'intégrité de la pièce, à moins que le plastique ne soit endommagé.
Les causes :
Les marques de brûlures moulées par injection sont généralement causées par air emprisonné ou surchauffe de la résine pendant l'injection. Surchauffe est souvent causée par vitesse d'injection élevée ou chauffage des matériaux.
Solutions :
- Pour éviter la surchauffe, abaissez les températures de fusion et de moulage.
- Réduire la vitesse d'injection pour éviter la formation d'airlock dans le moule.
- Développer les vannes de gaz et portes pour évacuer l'air emprisonné.
- Réduire la durée du cycle de moulage afin d'éviter la surchauffe de l'air et de la résine.
2. Lignes d'écoulement :
Les lignes d'écoulement sur les zones plus fines des composants moulés apparaissent sous la forme d'un motif ondulé, souvent d'une couleur différente de celle de la zone environnante. Elles peuvent également prendre la forme de bandes en forme d'anneau à la surface d'un produit, près des "portes" du moule. Les marques d'écoulement n'affectent pas l'intégrité des composants. Elles peuvent être inesthétiques et désagréables sur les lunettes de soleil haut de gamme.
Les causes :
Des lignes d'écoulement se forment lorsque la vitesse de refroidissement du matériau varie dans le moule. Le matériau peut également refroidir de manière irrégulière en raison épaisseur de la paroi, en quittant les lignes d'écoulement.
Le plastique fondu se refroidit rapidement pendant l'injection, et des marques d'écoulement se forment lorsque la vitesse est trop lente. Lors du remplissage du moule, la pièce en plastique durcit et se gomme, ce qui donne lieu à un motif ondulé.
Solutions :
- Augmenter la vitesse d'injection, la pression et la température pour remplir le moule avant le refroidissement (remède courant pour les lignes d'écoulement des produits moulés par injection).
- Pour maintenir le débit et éviter les lignes d'écoulement, arrondir les coudes lorsque l'épaisseur de la paroi augmente.
- Le déplacement des portes du moule permet d'éviter que le matériau ne refroidisse trop rapidement pendant l'écoulement.
- L'augmentation du diamètre de la buse permet d'accroître le débit et d'éviter un refroidissement prématuré.
3. Vides d'air :
Dans les pièces moulées, les vides sont des défauts de moulage par injection qui se réfèrent à des bulles d'air piégées. Les vides sont considérés comme un "petit" problème de contrôle de la qualité. Des vides plus importants ou plus nombreux peuvent affaiblir l'article moulé car de l'air est présent là où la substance moulée devrait l'être.
Les causes :
Une cause fréquente des vides est une pression de moulage insuffisante. Lorsque le matériau situé près de la paroi du moule se refroidit trop rapidement, il se solidifie et tire vers l'extérieur, ce qui provoque un abcès. Des vides peuvent apparaître lorsque la densité du matériau passe de l'état liquide à l'état solide. Les produits moulés présentent davantage de vides d'une épaisseur supérieure à 6 mm.
Solutions :
- Pour éviter les vides, augmenter la pression d'injection pour éliminer l'air emprisonné.
- Pour réduire les bulles d'air, utilisez un matériau à faible viscosité.
- Pour éviter un refroidissement prématuré, placez les portes près des parties les plus épaisses du moule.
4. Déformation :
Lorsque les composants moulés par injection se rétractent de manière inégale, un gauchissement se produit. Si un retrait inégal sollicite différentes zones du composant moulé, le plastique et d'autres matériaux peuvent se déformer pendant le processus de refroidissement. Lorsque l'élément surcontraint refroidit, il se plie ou se tord. Lorsqu'il est posé à plat, un composant qui est censé être plat laisse un espace.
Les causes :
Le plastique moulé par injection et d'autres matériaux comparables se déforment sous l'effet des facteurs suivants refroidissement rapide. Une surchauffe ou un matériau fondu à faible conductivité thermique peuvent exacerber le problème. Le gauchissement peut se produire lorsque les parois du moule ne sont pas uniformément épaisses, car le retrait augmente avec l'épaisseur de la paroi.
Solutions :
- Veillez à ce que le matériau refroidisse suffisamment lentement pour éviter des tensions inégales.
- Réduire la température du matériau ou du moule.
- Envisager l'utilisation d'un matériau qui ne rétrécit pas, comme les thermoplastiques chargés de particules qui rétrécissent beaucoup moins que les matériaux semi-cristallins ou les qualités non chargées.)
- Pour assurer la stabilité du refroidissement, il faut revoir la conception du moule en veillant à ce que l'épaisseur de la paroi soit continue et à ce que la pièce soit symétrique.
5. Marques d'évier :
Marques d'évier sont de petites dépressions sur la surface lisse d'un objet moulé. Lorsque la moitié intérieure d'un composant moulé se rétracte, elle aspire la matière de l'extérieur vers l'intérieur.
Les causes :
Les marques d'évier produisent l'inverse des vides. Le matériau se refroidit trop lentement près de l'extérieur de la pièce. Le rétrécissement force le matériau extérieur à l'intérieur avant qu'il ne refroidisse, ce qui provoque une dépression. Les marques d'enfoncement, comme les vides, sont plus fréquentes dans les pièces plus épaisses.
Solutions :
- Pour refroidir le matériau de surface, augmentez la pression de maintien et la durée.
- Le refroidissement minimise le rétrécissement.
- Des parois de moule plus minces accélèrent le refroidissement de la surface.
6. Jetting :
Le jet est un autre défaut courant du moulage par injection causé par une pression d'injection excessive. Le polymère fondu injecté à haute pression à travers une petite porte gicle souvent à travers la porte au lieu de remplir progressivement la cavité du moule. Lorsque cette première ligne de matériau durcit contre les parois du moule, le reste du matériau du moule la repousse, laissant des empreintes sur l'article fini.
Les causes :
Le jetting est une déformation d'un composant moulé qui se produit lorsqu'un "jet" initial de matériau fondu se solidifie avant que le trou ne soit rempli. Le jetting se produit sur le composant fini sous la forme d'une ligne sinueuse, généralement à partir de la porte d'injection. Un écoulement visible peut affaiblir un composant.
Solutions :
- Réduire la pression d'injection pour éviter que le matériau ne gicle trop rapidement dans les moules.
- Augmentation de la température du matériau et du moule pour empêcher une solidification précoce du jet.
- Fabriquer le moule de manière à ce que le matériau soit injecté transversalement plutôt que longitudinalement.
7. Lignes de soudure :
Les lignes de soudure apparaissent lorsque la matière en fusion converge dans un moule après avoir été fendue. La ligne de soudure en forme de cheveu est causée par mauvaise adhérence des matériauxce qui réduit la résistance des pièces.
Les causes :
Les fronts de polymères ou de matériaux fondus qui entrent en collision doivent conserver une température spécifique. Dans le cas contraire, ils se solidifient partiellement et ne se lient pas suffisamment, ce qui entraîne l'apparition de lignes de soudure.
Solutions :
- Les hausses de température empêchent la solidification partielle dans les lignes de soudure des pièces moulées.
- Retarder le refroidissement du moule en augmentant la vitesse et la pression d'injection.
- Enlever toute barrière contre les moisissures.
- Pour un écoulement plus rapide et un refroidissement moindre, utiliser un matériau à point de fusion ou à viscosité plus bas. Jetting
8. Discoloration
Un article moulé est décoloré lorsqu'il n'est pas de la bonne couleur. La décoloration se limite souvent à quelques stries sur un article moulé. Cette déformation n'affecte pas la résistance.
Les causes :
La décoloration, qui est l'un des défauts du moulage par injection, peut être causée par restes de granulés ou la résine d'un cycle de production précédent. Parmi les autres difficultés, on peut citer mauvaise stabilité à la chaleur de l'ingrédient colorant ou mélange inadéquat de mélanges-maîtres.
Solutions :
- Veiller à ce que la trémie, la buse et le moule soient nettoyés entre chaque production.
- Utilisez un produit de purge pour nettoyer la machine.
- Assurez-vous que vous ou votre fournisseur utilisez un colorant fiable.
- Mélanger uniformément le mélange maître pour obtenir une teinte homogène.
9. Coup court :
A coup court se produit lorsque la matière en fusion ne remplit pas le moule. La pièce moulée incomplète refroidit. Dans le cas d'un tir court, des étagères en plastique incomplètes ou des dents de fourche manquantes peuvent apparaître. Les tirs courts constituent un défaut important qui peut avoir un impact sur la fonction ou l'apparence de la pièce.
Les causes :
La plupart des tirs courts sont dus à des contraintes de débit dues à des vannes étroites ou bloquées. Lorsque la substance est trop froide ou trop dense, il n'est que parfois possible de la remplir avant refroidissement. Des poches d'air peuvent obstruer le flux et la pression d'injection peut être minimale.
Solutions :
- Pour améliorer l'écoulement des moisissures, élargir les canaux ou les vannes.
- Augmenter la vitesse d'injection, la pression ou l'épaisseur du matériau de base pour améliorer le débit.
- Augmenter la température du moule pour ralentir le refroidissement du matériau.
- Pour évacuer l'air emprisonné, ajoutez ou prolongez les évents d'évacuation des moisissures.
10. Décollement
Le prochain défaut de moulage par injection sur notre liste est le décollement. Le décollement désigne les fines couches d'un article moulé qui se séparent ou se détachent de la substance sous-jacente. Le délaminage est un défaut d'écaillage, similaire à l'écaillage du mica. Ce défaut a un impact substantiel sur la résistance du composant.
Les causes :
La cause la plus fréquente de délamination est la contamination des granulés de résine ou du matériau de base. Deux matériaux non liants s'écaillent. Le décollement peut également se produire lorsque ABS et polypropylène combiner. Dans un tel scénario, la perte de résistance des matériaux est dangereuse pour les pièces critiques pour la sécurité.
Les agents de démoulage utilisés pour extraire les composants du moule peuvent également être une source d'infection. Le décollement peut également être induit par un séchage inadéquat avant utilisation.
Solutions :
- En cas d'humidité extrême, augmenter la température du moule ou pré-sécher le matériau.
- Le personnel doit stocker et manipuler avec précaution les granulés de résine ou le matériau de base afin d'éviter toute contamination.
- Envisager de changer la buse d'injection pour utiliser un agent moins libérateur.
11. Flash :
A flash est un autre des défauts du moulage par injection, à savoir l'excédent de matériau de moulage qui forme une fine lèvre ou une protubérance sur le bord d'un composant. Le matériau s'écoule en dehors des voies d'écoulement définies dans les plaques d'outillage ou la broche d'injecteur. La bavure est généralement mineure, mais elle peut constituer un problème important si elle est visible. L'élimination de la bavure est souvent effectuée dans le cadre du retraitement d'un produit moulé.
Les causes :
Les moules mal conçus ou endommagés provoquent la bavure. La température du moule ou la pression d'injection peuvent également provoquer une bavure. Lorsque la force de serrage entre les plaques est insuffisante, la matière peut passer entre elles.
Solutions :
- Réoutillage ou reconception si les plaques du moule ne s'adaptent pas ou si le matériau déborde.
- Augmenter la force de serrage pour diriger le flux de matériau.
- Régler la température du moule, la pression d'injection et la ventilation pour améliorer le flux de matière.
Conclusion :
Les défauts mentionnés ci-dessus sont les plus courants dans le domaine du moulage par injection. Leur apparition est plus ou moins liée au choix des matériaux ou aux problèmes de production que vous pouvez rencontrer. En suivant les mesures préventives évoquées pour chaque défaut, vous pouvez faire en sorte qu'aucun de ces défauts ne se produise pendant la phase de moulage par injection.