Molding done with injection molding plastics undergoes a process known as shrinkage, which contracts as it cools after being injected. Most of the shrinking happens inside the mold while it is cooling, but there is still some shrinking after the part has been ejected since it continues to cool.
It indicates the extent to which the size of the plastic component is reduced after it is removed from the mold and allowed to cool. Plastic kinds, molding conditions, the construction of the mold, and other factors all play a role in the shrinkage of plastic.
There is a wide range of shrinking rates between the various polymer materials. Second, the rate at which the contours of the plastic component strongly influence plastic contracts, the degree of difficulty of the component’s internal structure, and the presence or absence of inserts.
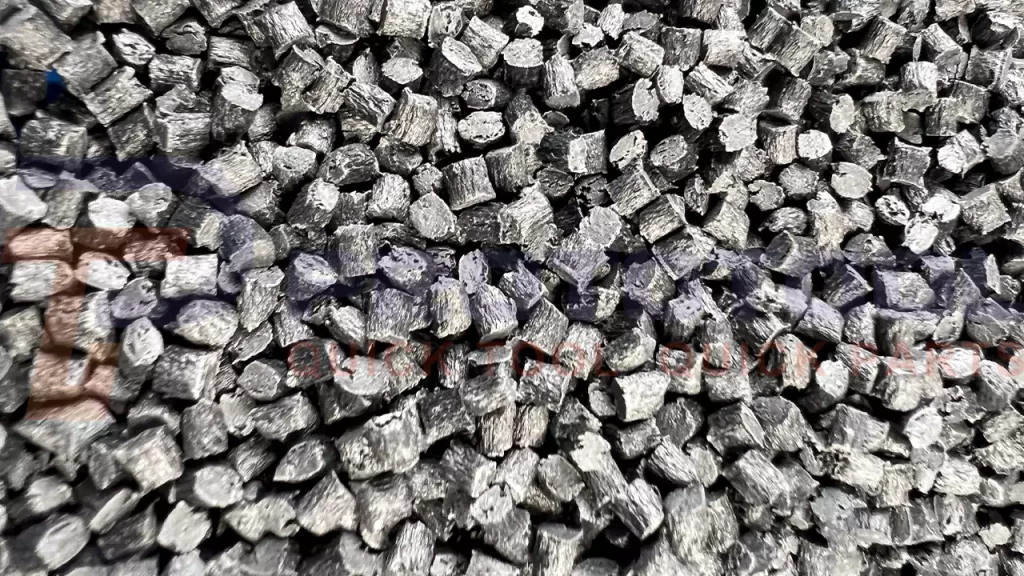
According to these factors, it’s essential to understand what shrinking is, how it occurs in different injection molding plastics, and how it happens. Understanding these aspects can help you understand the process and its importance. Still, it can also help maintain practical shrinkage that doesn’t impact the final product size demands, leading to faulty products. So keep reading to learn about plastic shrinking in injection molding.
Types of Plastics That Shrink and How?
The material shrinking during and after the production process contributes to the warping in injection-molded plastic products significantly. Before we delve into the topic of warpage in components, it is vital to grasp how and why matières plastiques contract. To accomplish this, we need to begin our investigation at the molecular level by taking a detailed look at the processes that occur when polymers are melted and then cooled. The properties of melting and cooling are determined, for the most part, by the kind of polymer and, if any filler or fiber reinforcement is present, by the presence of it as well.
1. Materials that are only partially crystalline
Semi-crystalline materials, as opposed to amorphous materials, feature highly organized sections with firmly grouped molecular structures. They behave similarly to amorphous polymers in that the crystalline structures become looser when they melt, and the molecules align themselves in the flow direction.
However, the materials only get more relaxed once they have cooled. Instead, they keep their orientation in the direction that the flow is going, and the molecules begin to recrystallize, resulting in substantially faster rétrécissement rates. In this particular instance, the effect is significantly more pronounced in the opposite direction of the flow.
2. Amorphous Materials
Amorphous polymers are a form of polymer and contain various materials. Some examples of amorphous polymers include ABS, polystyrene, and polycarbonate. Unlike a bowl full of spaghetti, they exhibit a disordered and twisted molecular orientation when found in their natural state. As a result of the melting of these materials, the forces that hold the molecules together become weaker, and the molecules drift farther apart.
Shear, which is like friction, happens during the injection phase. This causes the molecules to separate and line up with the flow direction. When the flow stops, the molecules become relaxed and return to their original condition, random orientation. They are pulled closer together by intermolecular forces until the temperature lowers to a point where it is cold enough to freeze them in place. These pressures cause a uniform shrinking, but the effect of relaxation makes the shrinking happen more in the direction of flow.
3. Materials that are Reinforced with Fiber
Fibers are frequently mixed in with polymer compounds to improve the material’s strength and its other qualities. When fibers are included in the plastic, they have the potential to mitigate the consequences of shrinkage caused by the molecular orientation discussed above. Because fibers do not expand or contract in response to changes in temperature, materials that are filled with fibers will often have less shrinking in the direction that their orientation runs.
Injection Molding Plastics Method of Shrinking:
Variations in shrinking are the root cause of warpage, which may sound complicated but is quite straightforward. To put it another way, when a component is shrunk equally in all directions, it not only gets smaller but also keeps its original shape. On the other hand, if one part shrinks at a different rate than the others, the difference will cause tensions inside the part. When the part is ejected from the mould, it will become misshapen if the forces placed on it exceed its capacity to maintain its structural integrity.
There are four primary types of shrinkage, which are as follows:
- Regional
This happens when the rate at which each part shrinks is different than the regions that are closest to the gate and the regions that are closest to the end of fill (EOF); typically, this variation occurs between the areas of the part that are thicker (the gate area) and areas that are thinner (the EOF area). One region is contracting at a faster rate than another.
- Away from the Dense Substance
This difference in shrinking happens when the shrinking on the top of the part differs from the shrinking on the bottom when the part is cut in half. Because of this difference, the component has the potential to bow because one side can contract more than the other and, as a consequence, will be smaller than the other side.
- In a directional sense
Differences in shrinking can occur both parallel to and perpendicular to the orientation of the material, often known as the direction of flow. The alignment of molecules or fibers can cause this. As was said before, an amorphous material tends to contract more in a direction parallel to the flow direction. The shrinkage of crystalline solids is typically greater perpendicular to the flow direction.
- Comparing the In-plane to the Thickness
More often than not, polymers shrink in the direction of their thickness rather than in the direction of their surface plane. This effect is caused by mold prevention. The presence of a difference between how much something shrinks in the in-plane direction and the thickness direction can lead to warping. It often happens in the part’s corners, which are sometimes thicker than the nominal thickness of the wall.
Reasons Behind the Shrinking:
1. The difference in length caused by thermal expansion and cold contraction in polymers
When the mold for the injection molding needs to be made, it is essential to melt the raw components for the plastic. At this point, the temperature of the melting process rises to between 200 and 300 degrees, and the raw components for the plastic are heated and expanded. The temperature of the injection mold will drop as it goes through the cooling process, resulting in a probable reduction in its volume.
2. Variations in the atomic and molecular composition of plastics
For instance, during the molding process for thermosetting plastics, the structure of the molecules that make up the resin transforms from linear to body form. Since the volume mass of the body, the structure is more than that of the linear structure, and since the linear structure’s total volume decreases, the body structure gets smaller.
3. A shift in the residual stress
The sheer force of molding pressure, anisotropy, uneven mixing of additives, and mold temperature can all impact the tooling while it is being used to make injection molding plastics.
After molding, the moule d'injection will still have some residual stress. This residual stress will progressively reduce and redistribute itself as time goes on. As a direct consequence, the injection mold will become smaller once more. This type of shrinking is sometimes referred to as post-shrinkage.
4. The size of the gate section
There is a wide range of cross-sectional sizes available for injection molds. A large gate raises cavity pressure and lengthens gate closure time, enabling more molten material to flow into the cavity. This is accomplished by increased melt flow.
5. Plastic variety
Crystalline polymers, such as polypropylène (PP) and polyamide (PA), have a bigger shrinkage after demoulding and a more comprehensive shrinking range than non-crystalline plastics, such as polycarbonate (PS) and acrylonitrile butadiene styrene (ABS).
Conclusion :
In most circumstances, multiple impacts may be counteracting or amplifying each other, making it impossible to separate each effect’s contribution. Understanding how and why injection molding plastics shrinks gives engineers a competitive advantage when analyzing through simulation to build an appropriate plastic product that fits within their budget and time frame.