Lorsque les goupilles d'éjection en moulage par injection introduites dans les processus industriels, elles ont permis d'accélérer la production, d'automatiser les procédures et de produire des biens de meilleure qualité. En outre, elle a permis d'uniformiser la conception des produits. La méthode de moulage par injection a encore de nombreuses questions qui doivent être corrigées, comme marques de la goupille d'éjectionBien qu'elle ait amélioré ses procédures de fabrication, elle n'est pas en mesure d'offrir des produits de qualité supérieure. Cela permettra de garantir que les produits finaux sont supérieurs et plus puissants. C'est pourquoi cet article examine les goupilles d'éjection 101 et la manière d'améliorer leur conception pour obtenir des produits plus performants.
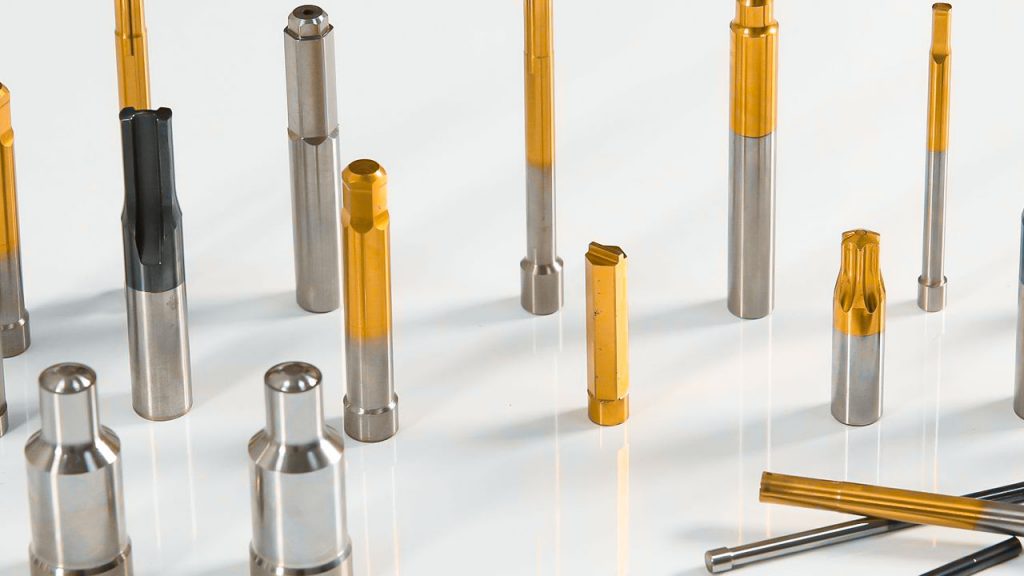
Goupille d'éjection pour le moulage par injection : Qu'est-ce que c'est ?
Les goupilles d'éjection pour moules à injection sont essentielles pour la fabrication de composants. Elles constituent un élément crucial du système d'éjection du processus de moulage par injection dans le moule, qui détermine le résultat des produits finis.
Un moule métallique est injecté avec du plastique en fusion pour prendre la forme du moule au cours du processus de fabrication, connu sous le nom de moulage par injection. Par conséquent, les broches d'éjection servent à retirer les pièces finies des moules mourants. Les faces A et B constituent les deux composantes du moule métallique. Les deux moitiés du moule métallique sont séparées lorsque la substance en fusion dans le moule a refroidi, ce qui permet de retirer le plastique solide. La conception d'un moule d'injection permet de soulever la moitié du côté A lorsqu'il est ouvert, laissant la partie formée et le côté B.
Les marques de la broche d'éjection qui forcent la pièce produite à sortir du moule sont situées sur la partie B du moule. Les produits finis présentent souvent une bosse laissée par la marque de la broche d'un moule à éjecteur.
Différents styles de broches d'éjection :
La qualité du mécanisme d'éjection dans la construction du moule d'injection a un impact direct sur la qualité du produit plastique fini. Une mauvaise conception entraînera plusieurs défauts, tels que des marques de goupilles d'éjection dans le moulage par injection, dans la pièce en plastique, notamment des fissures, des déformations et un blanchiment de la pièce en plastique. Le lien le plus crucial dans la conception de l'éjection est le choix du type d'éjection approprié. Nous utilisons généralement la force d'éjection et la résistance pour maximiser le type, le nombre et la position de l'éjection. Les types d'éjecteurs les plus fréquemment utilisés dans le cadre du processus sont énumérés ci-dessous.
Goupille d'éjection en noir :
Les goupilles en nitrure H13 ne peuvent pas être utilisées à des températures de travail supérieures à 600°C, c'est pourquoi les fabricants ont créé ces goupilles d'éjection. La goupille d'éjection noire est recouverte d'un revêtement noir sur sa surface, ce qui la rend autolubrifiante et lui permet de résister à des températures allant jusqu'à 1000°C. Il s'agit d'un éjecteur de prix qui peut être utilisé avec un mécanisme d'éjection en métal dans les moules de voitures.
Goupilles pour éjecteurs durs traversants :
Le traitement thermique est utilisé sur ces goupilles d'éjection pour moules d'injection afin de maintenir une dureté uniforme sur tout le diamètre de la goupille. La majorité des applications des goupilles dures à cœur sont destinées au système d'éjection du plastique dans les moules, car elles peuvent tolérer des températures de fonctionnement allant jusqu'à 200°C.
Goupille d'éjection avec cémentation :
Ces goupilles sont beaucoup plus résistantes que les goupilles dures et conviennent aux systèmes d'éjection des moules de coulée sous pression. Elles sont également connues sous le nom de goupilles Nitride H13. Nitrées à 65-70 HRCLes goupilles cémentées peuvent supporter des températures de plus de 200°C.
Considérations de conception pour le moulage par injection :
La conception d'un moule à injection doit garantir qu'il fonctionne comme prévu. Un défaut de conception peut entraîner la rupture d'une pièce ou l'apparition de marques de goujon éjecteur de moulage par injection, ce qui serait trop coûteux ou difficile à réparer. Il est donc essentiel de mettre en œuvre une conception bien structurée, et il y a quelques points à prendre en compte.
Epaisseur de paroi égale :
La matière en fusion s'écoule facilement et sans résistance lorsqu'elle est coulée dans un moule avec une épaisseur uniforme. épaisseur de la paroiLa partie la plus fine du matériau fondu se refroidit en raison de l'irrégularité des parois du moule. La partie la plus fine du matériau fondu se refroidit en raison de l'irrégularité des parois du moule. Par conséquent, le matériau se rétrécit au fur et à mesure que la partie plus épaisse refroidit, ce qui entraîne une concentration de la tension et, finalement, une fissuration lorsque la section est retirée.
Le problème peut être résolu par le carottage et l'insertion de goussets, si votre conception ne permet pas d'obtenir une épaisseur de paroi uniforme. Pour maintenir l'uniformité le long de la paroi, le plastique fondu est retiré sur une grande surface à l'aide d'une technique appelée carottage. Les goussets sont des renforts que vous placez sur la paroi en tant que structures de soutien afin d'amincir la paroi.
Le type de substance :
L'utilisation prévue du produit doit déterminer le type de matériau utilisé. L'épaisseur, la flexibilité et la dureté sont autant de types de matériaux différents. L'utilisation prévue du composant et sa conception dépendent du type de matériau choisi. Certains matériaux peuvent être courbés et épaissis. En outre, avant de choisir le type de matériau, vous devez tenir compte des points suivants.
Établir des angles d'attaque :
Un moule d'injectionLes deux côtés du moule peuvent être inclinés, ce qu'on appelle un angle de dépouille. Le plastique peut être facilement démoulé en raison de cette petite déformation de la forme du moule. Lors de l'extraction de l'article du moule, un angle de dépouille doit être présent pour assurer la résistance au frottement.
Le dégagement facile des pièces du système d'éjection dans le moule serait assuré en autorisant davantage d'angles de dépouille. Un manque d'angles de dépouille entraînerait le retrait de l'article avec des marques importantes de la broche d'éjection, ainsi que des éraflures sur la paroi du moule.
Emplacement des portes :
Les points d'entrée du plastique fondu dans le moule sont appelés portes de moulage par injection. Un portillon, cependant, laisse une marque d'épingle lorsque l'article refroidit, et cette marque d'épingle est souvent encore visible même après que la bosse a été enlevée. L'équipe de conception peut utiliser une porte de bord pour résoudre ce problème et rendre les bosses moins visibles. L'extension de la broche d'éjection permet également d'injecter la substance fondue. Après refroidissement, les goupilles d'éjection peuvent pousser la marque de la goupille qui se forme sur la porte lorsque l'article est retiré du moule après refroidissement.
Les contre-dépouilles doivent être réduites au minimum :
Dans la conception du moule, les contre-dépouilles sont des éléments saillants qui empêchent le démoulage de l'une ou l'autre des faces. Comme elles empêchent l'éjection directe des pièces du moule, les contre-dépouilles sont un élément nécessaire et inévitable de la conception des moules. conception de moules.
La création de verrouillages ou de loquets qui permettent un retrait ou un assemblage simple peut toutefois éliminer les contre-dépouilles. Dans un système d'éjection basé sur un moule, les contre-dépouilles doivent être moins nombreuses, dans la mesure des possibilités de l'équipe de conception.
Les bords doivent être arrondis :
Il y a de nombreux avantages à avoir des coins arrondis à l'intérieur et à l'extérieur de la pièce. Ils réduisent la zone de concentration des contraintes et empêchent le composant de se briser. Les arêtes vives empêchent le plastique en fusion de s'écouler librement à travers la matrice et, lorsque le plastique refroidit, il s'appuie sur les arêtes et il est difficile de l'enlever. La formation et l'enlèvement des marchandises sont améliorés et facilités par les pièces à bords arrondis, qui sont également plus abordables à créer.
Erreurs et corrections les plus courantes :
Le moulage par injection qui utilise des broches d'éjection présente certains défauts. Les défauts potentiels et les correctifs nécessaires sont énumérés ci-dessous.
- Marques de la goupille d'éjection :
Les "bosses" sont des marques de la goupille d'éjection. Cette marque d'épingle se produit lors du démoulage de l'article. Cette marque de goupille peut entraîner la rupture des produits lors de leur utilisation. Il est donc essentiel de concevoir un système d'éjection dans le moule afin d'éviter les marques de goupilles d'éjection.
- Les broches d'éjection du moule d'injection doivent être positionnées de manière à ce que la force d'éjection soit continue sur toute la portion.
- Pour éviter les défauts de marquage des broches d'éjection, placez les broches d'éjection sur des éléments durs tels que des inserts métalliques, des piliers et des nervures.
Au lieu de placer les broches d'éjection sur des pentes, concevez la partie avec des surfaces planes.
- Les pauses :
Les goupilles d'éjection se cassent souvent parce qu'il y a un décalage entre la force nécessaire pour éjecter la pièce du moule et la résistance de la goupille. Il faut de la force pour expulser les composants du moule. Parfois, la longueur de la goupille, qui n'est pas soutenue, fait que la force nécessaire est supérieure à la résistance de la goupille, ce qui entraîne sa rupture.
L'utilisation d'un plus grand nombre de goupilles d'éjection de plus grand diamètre est donc le traitement le plus efficace pour les ruptures de goupilles d'éjection. De cette manière, la force nécessaire est répartie uniformément sur toutes les broches, ce qui réduit la probabilité de rupture.
- Jetting :
Lorsque le matériau fondu est injecté dans un moule rapidement ou avec une petite ouverture, il se produit un phénomène de jetting, qui entraîne une déformation de la forme. Pour y remédier, il faut
- Augmenter la taille de la porte et réguler la façon dont le matériau fondu s'écoule dans le moule.
Conclusion
Les goupilles d'éjection jouent un rôle crucial dans le processus de moulage par injection, que les experts en conception ne peuvent ignorer. Il s'agit d'éviter les marques de goupilles d'éjection et autres défauts, ce qui est important pour le produit créé dans le moule. C'est pourquoi il est essentiel de faire confiance à une entreprise qui comprend les principes de base du moulage par injection. Conception pour la fabricationcomprend comment utiliser les goupilles d'éjection et a fait ses preuves en matière de conception de moulage par injection de goupilles d'éjection.
Pour le moulage par injection de vos broches d'éjection, Prototool peut vous garantir des conceptions optimales. Pour obtenir des conseils en matière de fabrication, adressez-vous à leur personnel d'assistance, qui se surpassera pour vous garantir une expérience positive et fiable de l'utilisation de leurs services.