La conception du moule de la télécommande ne dicte pas seulement sa fonctionnalité, mais aussi son attrait esthétique et l'expérience de l'utilisateur dans le domaine de l'électronique grand public. Le parcours de Prototool dans la création d'un moule de télécommande en plastique allie innovation et précision. Cela donne un aperçu du processus méticuleux qui permet de donner vie à un gadget simple mais essentiel.
Exigences du client en matière de produits de télécommande
Le boîtier de la télécommande comprend généralement une coque supérieure et une coque inférieure, comme illustré à la figure 1. Les dimensions maximales de la coque supérieure sont de 100,00 mm x 50,00 mm x 10,00 mm, avec une épaisseur moyenne de 1,50 mm. Fabriquée en ABS, la coque supérieure a un taux de rétraction de 1,005 et pèse 10,55 grammes. Il est impératif que les pièces en plastique soient exemptes de défauts tels que lignes de soudure, coups courts, marques d'écoulement, poches d'air, gauchissements, stries argentées, limailles froides et jetting, et qu'elles soient conformes aux normes environnementales ROSH.
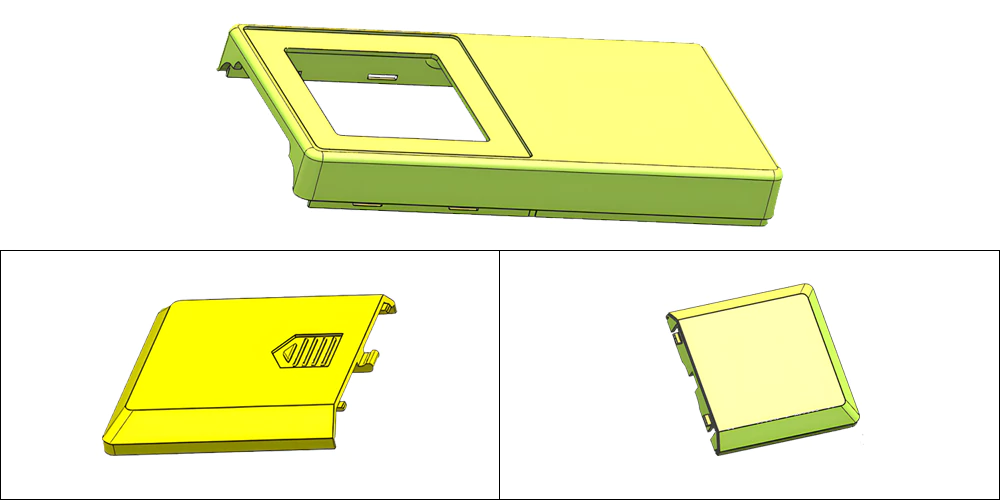
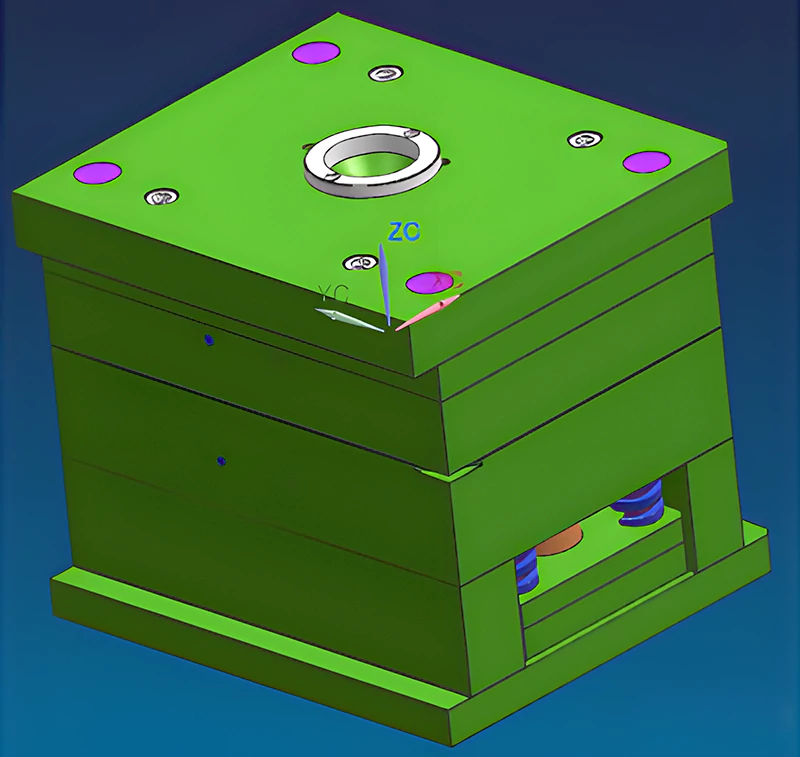
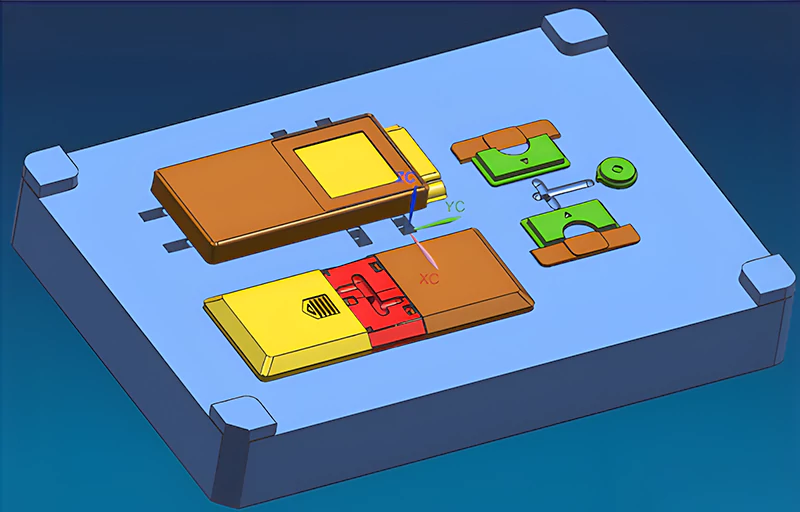
Analyse de la structure et conception du moule du produit télécommandé
Les coques supérieure et inférieure de la télécommande sont constituées de trois pièces en plastique. La coque supérieure est d'une seule pièce, tandis que la coque inférieure comprend un couvercle de batterie. La conception globale de ces pièces est une structure de cadre plat, reliée le long du périmètre par des boutons-pression. Ces encliquetages nécessitent la conception d'élévateurs angulaires ou de curseurs latéraux pour les mécanismes de traction du noyau.
Comme le montre la figure 3, la disposition du moule adopte une conception de moule familial. Ce modèle comprend la coque supérieure, la coque inférieure, le couvercle de la batterie et trois petits composants internes. Les moules familiaux sont avantageux pour les prototypes ou la production à petite échelle en raison de leur rentabilité. Cependant, ils posent des problèmes pour les produits de haute précision, car il est difficile d'obtenir des systèmes de canaux équilibrés. Cette complication rend le processus de moulage par injection plus complexe. Pour la production en série, les composants des commutateurs de débit peuvent être conçus pour ajuster les quantités produites en fonction de la demande.
Assemblage et précision des moules
La figure 3 montre la disposition des six pièces en plastique afin d'obtenir un système de glissières équilibré. La conception du moule utilise une base de moule standard simplifiée FCI3040 A60 B90 avec S136 pour la cavité et NAK80 pour le noyau. Nous positionnons la cavité et le noyau à l'aide d'une méthode d'interverrouillage à quatre coins. Cette méthode doit s'aligner sur la structure du noyau du moule afin d'économiser de l'acier et de réduire le temps d'usinage. Parfois, le sens de l'emboîtement tient compte de la résistance de la cavité. Dans ce cas, le côté de la cavité est en retrait et le côté du noyau est en saillie pour serrer et empêcher l'expansion de la cavité sous la pression d'injection. L'angle latéral de l'interverrouillage, généralement compris entre 5° et 10°, a un impact significatif sur la résistance de la cavité. fermeture du moule la précision. Plus l'angle est petit, plus la précision est élevée.
Mécanisme d'encliquetage latéral et d'éjection
Les encliquetages latéraux des coques supérieure et inférieure sont résolus à l'aide de releveurs angulaires pour l'éjection. Il existe différentes structures de releveurs angulaires, qui utilisent généralement des rainures en T ou des entraînements à rouleaux. En raison de la petite taille des pièces en plastique et de l'espace limité, le bloc de guidage pour le petit releveur angulaire est conçu au dos de la plaque B. Les figures 6 et 7 illustrent respectivement le siège du releveur angulaire de type T et le siège du releveur angulaire à structure de goupille. Le diamètre de l'axe doit être d'au moins 4 mm et la dureté du siège du coulisseau doit être supérieure à HRC40.
Innovations dans la conception de l'élévateur angulaire
La figure 8 montre une structure de siège de releveur angulaire vissée. Dans cette structure, le siège du releveur est vissé au bas du releveur angulaire, avec une rondelle élastique en dessous pour empêcher le desserrage. L'ajout de blocs d'usure à la plaque de poussée facilite l'entretien et le remplacement après usure. La figure 9 présente une version améliorée du siège du releveur angulaire à structure à broches. Le diamètre de l'axe est d'au moins 4 mm et la surface inférieure plate du releveur angulaire supporte la pression d'injection, ce qui améliore considérablement les conditions de force par rapport à la conception de la figure 7.
Conclusion
Lors de la conception de moules pour télécommandes en plastique, il est essentiel de prêter attention aux détails de chaque composant, de la disposition du moule au mécanisme d'éjection, pour produire des pièces en plastique de haute qualité et exemptes de défauts. En adhérant à ces principes de conception et en exploitant des techniques innovantes, les fabricants peuvent assurer une production efficace et répondre à des normes environnementales et de qualité rigoureuses.