Erfahrene Produktdesigner kennen sich mit Spritzgussverfahren bestens aus und berücksichtigen zahlreiche Faktoren bei der Gestaltung von Kunststoffteilen. Dieser Artikel konzentriert sich auf wesentliche Elemente wie Wandstärke, Entformungswinkel, Rippen, Löcher, Säulen, Schnapper, Presspassungen und Toleranzen bei der Konstruktion von Kunststoffformteilen.
Wanddicke in Kunststoffteilen Design
Die Bestimmung der richtigen Wandstärke ist entscheidend. Andere Merkmale wie Rippen und Verrundungen beziehen sich auf die Wanddicke. Die Wandstärke eines Kunststoffprodukts hängt von verschiedenen Anforderungen ab, u. a. von den äußeren Kräften, denen es standhalten muss, von der Abstützung anderer Teile, von den Eigenschaften des Kunststoffs, vom Gewicht, von der elektrischen Leistung, von der Maßhaltigkeit, von der Stabilität und von den Montageanforderungen.
Üblicherweise liegt die Wandstärke von thermoplastischen Werkstoffen zwischen 1 und 6 mm, wobei 2 bis 3 mm am häufigsten vorkommen. Bei größeren Teilen können die Dicken 6 mm überschreiten. Tabelle 1 zeigt empfohlene Werte für die Wandstärke verschiedener Thermoplaste.
Materialien | Mindestwanddicke | Empfohlene Werte für kleine Werkstücke | Empfohlene Werte für mittlere Werkstücke | Empfohlene Werte für große Werkstücke |
Nylon | 0.45 | 0.76 | 1.5 | 2.4~3.2 |
PE | 0.6 | 1.25 | 1.6 | 2.4~3.2 |
PS | 0.75 | 1.25 | 1.6 | 3.2~5.4 |
PMMA | 0.8 | 1.5 | 2.2 | 4~6.5 |
PVC | 1.2 | 1.6 | 1.8 | 3.2~5.8 |
PP | 0.85 | 1.54 | 1.75 | 2.4~3.2 |
PC | 0.95 | 1.8 | 2.3 | 3~4.5 |
POM | 0.8 | 1.4 | 1.6 | 3.2~5.4 |
ABS | 0.8 | 1 | 2.3 | 3.2~6 |
Gleichmäßigkeit der Wanddicke
Eine gleichmäßige Wandstärke ist ein wichtiger Grundsatz bei der Konstruktion von Kunststoffteilen. Ungleichmäßige Wandstärken können zu ungleichmäßigem Schmelzefluss und Schrumpfung bei der Abkühlung führen, was Defekte wie Einfallstellen, Hohlräume, Verzug oder sogar Risse zur Folge hat. Außerdem kann es zu Schrumpfungsspuren, inneren Spannungen, Verformungen, Farbabweichungen oder Unterschieden in der Transparenz kommen. Dünnere Wände können die Festigkeit und Steifigkeit während des Gebrauchs und der Montage beeinträchtigen. Aus wirtschaftlicher Sicht erhöhen zu dicke Teile die Materialkosten und die Produktionszeit. Bereiche mit dickerem Kunststoff kühlen langsamer ab, was zu Einfallstellen führt. Abbildung 1 veranschaulicht die Gestaltung einer einheitlichen Wandstärke.
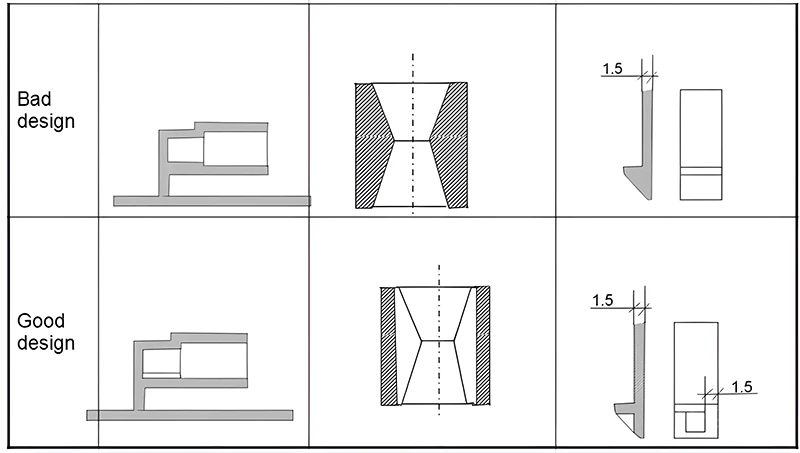
Wenn ein Übergang von dickeren zu dünneren Abschnitten unvermeidlich ist, sollte er schrittweise erfolgen, wobei ein maximales Verhältnis von 3:1 in der Wanddicke eingehalten werden sollte, wie in Abbildung 2 dargestellt.

In vielen Fällen können Konstrukteure mit Hilfe von Rippen die Gesamtwandstärke verändern, was nicht nur Material spart und die Produktionskosten senkt, sondern auch die Kühlzeit verkürzt. Die Abkühlzeit ist ungefähr proportional zur Wanddicke.
Außerdem müssen die Konstrukteure den Fließweg berücksichtigen, d. h. die Strecke, die das geschmolzene Material vom Anschnitt bis zu allen Teilen der Kavität zurücklegt. Im Allgemeinen besteht ein proportionales Verhältnis zwischen Fließweg und Wandstärke. Eine größere Wanddicke bedeutet einen längeren Fließweg. Ist das Verhältnis zwischen Fließweg und Wanddicke zu groß, kann es weit vom Anschnitt entfernt zu Materialmangel oder unvollständiger Füllung kommen. Daher kann es in manchen Fällen notwendig sein, die Wanddicke zu erhöhen.
Scharfe Winkel
Scharfe Winkel führen oft zu Defekten und Spannungskonzentrationen in Teilen. Diese Bereiche sind anfällig für unerwünschte Materialansammlungen bei Nachbehandlungen wie Galvanisieren oder Lackieren. Spannungskonzentrationen können unter Belastung oder bei Stößen zu Brüchen führen. Daher ist es ratsam, scharfe Winkel bei der Konstruktion zu vermeiden. Abbildung 3 zeigt ein Beispiel für ein scharfkantiges Design.
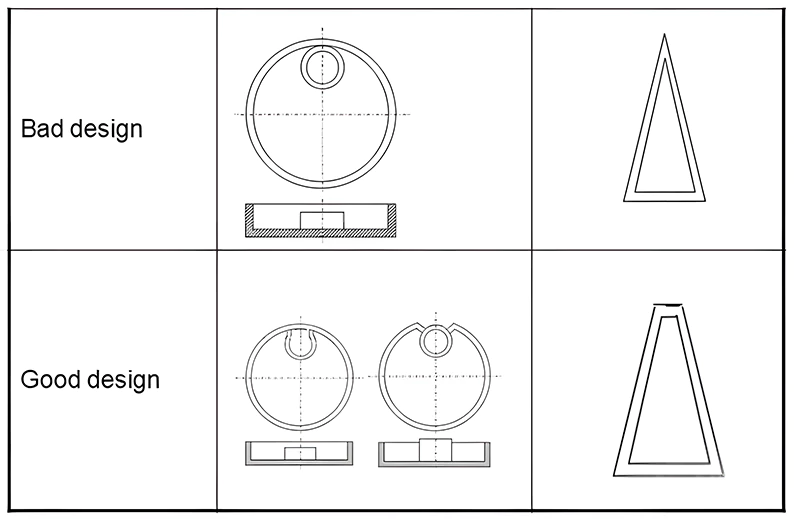
Überlegungen zu Entladungswinkeln und Auswurfrichtung
Auswurfrichtung und Trennungslinie
Zu Beginn der Entwicklung eines spritzgegossenen Produkts ist es entscheidend, die Ausstoßrichtung und die Trennlinie festzulegen. Dies gewährleistet minimale Kernziehmechanismen und reduziert die Auswirkungen von Trennlinien auf das Erscheinungsbild. Sobald die Auswerfrichtung festgelegt ist, sollten Strukturen wie Rippen, Druckknöpfe und Vorsprünge darauf ausgerichtet werden, um Kernzug zu vermeiden, Nahtlinien zu reduzieren und die Lebensdauer der Form zu verlängern. Die geeignete Trennlinie kann dann gewählt werden, um Aussehen und Leistung zu verbessern.
Beim Auswerfen aus der Form muss das Teil Auswerf- und Öffnungskräfte überwinden. Unter Öffnen versteht man das Lösen des Teils aus der Kavität. Wenn das Teil in der Form abkühlt, schrumpft es, wodurch die Lochwände den Kern fest umschließen. Durch die Reibung zwischen dem Teil und dem Kern, die Vakuumhaftung am Lochboden und andere Faktoren sind die Ausstoßkräfte wesentlich größer als die Öffnungskräfte. Übermäßige Ausstoßkräfte können das Teil verformen und Weißfärbung, Faltenbildung und Oberflächenabrieb verursachen.
Entwurfswinkel
Die Entformungsschrägen sind entscheidend für die Größe der Ausstoßkräfte. Da spritzgegossene Teile aufgrund der Schrumpfung beim Abkühlen häufig an der konvexen Form haften, gewährleisten gleiche Entformungswinkel an konkaven und konvexen Formen eine gleichmäßige Wandstärke und verhindern, dass das Teil nach dem Auswerfen an der heißeren konkaven Form haften bleibt. In besonderen Fällen, in denen das Teil nach dem Auswerfen an der konkaven Form haften bleiben soll, kann der Entformungswinkel an dem angrenzenden konkaven Teil verringert werden, oder es kann absichtlich ein Hinterschnitt an der konkaven Form angebracht werden.
Es gibt keinen festen Wert für Entformungsschrägen; sie werden in der Regel auf der Grundlage von Erfahrungswerten ermittelt. Hochglanzpolierte Außenwände können einen Entformungswinkel von nur 1/8 oder 1/4 Grad haben. Bei tieferen oder strukturierten Teilen sollte der Entformungswinkel entsprechend größer sein. Konventionell wird für jede 0,025 mm Tiefe der Textur ein zusätzlicher Entformungswinkel von 1 Grad benötigt.
Auch wenn größere Entformungswinkel im Allgemeinen den Auswurf erleichtern, ist es wichtig, die Maßhaltigkeit zu wahren. Die durch Entformungsschrägen verursachten Maßfehler müssen innerhalb des Präzisionsbereichs bleiben. Bei Teilen mit starker Schrumpfung oder komplexen Formen sollten größere Entformungswinkel in Betracht gezogen werden.
Rippen in der Konstruktion von Kunststoffteilen
Die Festigkeit von Kunststoffteilen hängt nicht nur von einer erhöhten Wandstärke ab. Vielmehr kann eine größere Dicke zu inneren Spannungen aufgrund von Schrumpfung führen und damit die Festigkeit verringern. Der Schlüssel zur Erhöhung der Festigkeit von Kunststoffteilen liegt in ihrer Steifigkeit. Dies wird häufig durch eine Kombination aus dünnwandigen Ausführungen und strategisch platzierten Rippen zur Erhöhung des Widerstandsmoments erreicht.
Überlegungen zum Rippendesign
Das Hinzufügen von Rippen führt jedoch zu einer größeren Dicke an der Verbindungsstelle mit der Hauptwand. Diese Dicke hängt in der Regel vom größten eingeschlossenen Kreis ab, der durch die Rippendicke und den Radius der Fußausrundung bestimmt wird. Bei einer Grundmaterialdicke von 4 mm ändert sich bei einer Änderung der Rippendicke und des Radius der Wurzelverrundung der Durchmesser des größten eingeschlossenen Kreises. Abbildung 4 veranschaulicht, wie eine lokale Zunahme der Wanddicke zu einer Schrumpfverformung auf der Rückseite führen kann, die das Erscheinungsbild beeinträchtigt. Ein geeignetes Design kann die Wahrscheinlichkeit von Oberflächeneindrücken verringern und so die Qualität des Teils verbessern.
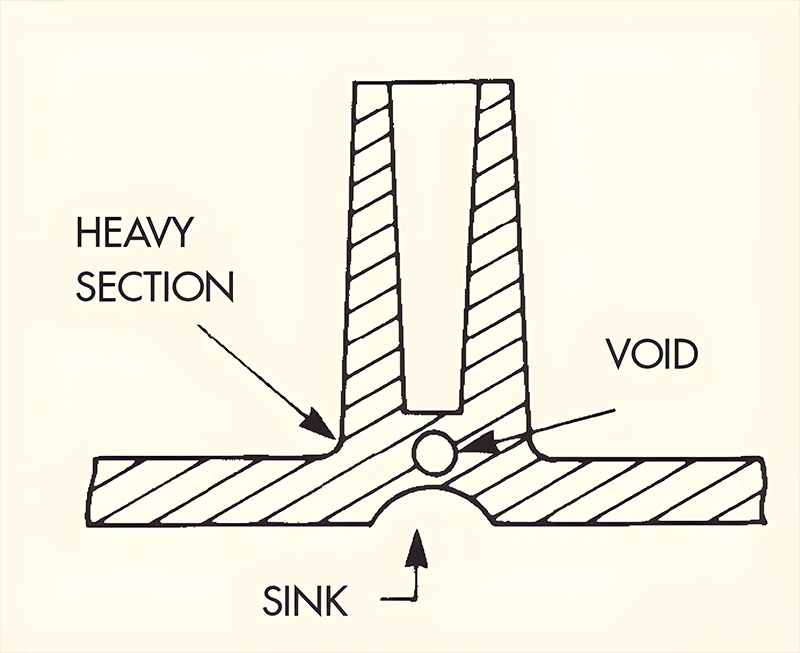
Aus der Analyse geht hervor, dass die Dicke der Rippe innerhalb bestimmter Grenzen minimiert werden sollte. Wenn die Rippe zu dünn ist, muss ihre Höhe erhöht werden, um die Steifigkeit zu erhalten. Zu dünne Rippen können jedoch zu Verformungen unter Druck, Schwierigkeiten beim Füllen während des Formens und zum Verkleben mit der Form führen. Der Radius der Rippenbasis sollte nicht zu klein sein, um Spannungskonzentrationen zu vermeiden.
Im Allgemeinen sollte der Radius der Rippenwurzel mindestens 40% der Rippendicke betragen. Die Rippendicke sollte zwischen 50% und 75% der Wanddicke des Grundmaterials betragen, wobei das höhere Verhältnis auf Materialien mit geringer Schrumpfung beschränkt ist. Die Höhe der Rippe sollte weniger als das Fünffache der Dicke des Grundmaterials betragen. Die Rippen müssen Entformungswinkel aufweisen und in Ausstoßrichtung ausgerichtet sein oder bewegliche Formteile verwenden. Der Abstand zwischen den Rippen sollte mehr als das Doppelte der Dicke des Grundmaterials betragen.
Um eine gleichmäßige Steifigkeit in alle Richtungen zu erreichen, ist die einfachste Methode, Rippen sowohl in Längs- als auch in Querrichtung hinzuzufügen, die sich im rechten Winkel kreuzen. Dadurch kann sich jedoch die Wandstärke an den Schnittpunkten erhöhen, was zu einer größeren Schrumpfung führt. Eine gängige Lösung ist das Hinzufügen eines runden Lochs an der Schnittstelle, um eine einheitliche Wandstärke zu erreichen (siehe Abbildung 5).
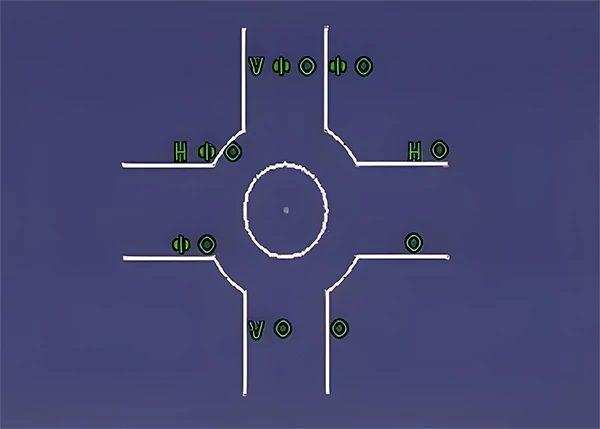
Überlegungen zur Konstruktion von Kunststoffteilen für Löcher
1. Platzierung und Stärke der Löcher
Die Anbringung von Löchern in Kunststoffteilen für den Zusammenbau oder die Funktionalität ist üblich. Die Größe und Platzierung dieser Löcher sollte idealerweise die Festigkeit des Produkts nicht beeinträchtigen oder den Herstellungsprozess komplizierter machen. Zu berücksichtigende Schlüsselfaktoren:
- Der Abstand zwischen benachbarten Löchern oder zwischen einem Loch und der nächstgelegenen Kante sollte mindestens so groß sein wie der Durchmesser des Lochs. Dies ist besonders wichtig für Löcher in der Nähe von Kanten, um Brüche zu vermeiden. Bei Gewindelöchern sollte der Abstand zwischen dem Loch und der Kante des Produkts im Allgemeinen mehr als das Dreifache des Lochdurchmessers betragen.
2. Arten von Löchern
Es gibt verschiedene Arten von Löchern, z. B. Durchgangslöcher, Sacklochbohrungenund gestufte Löcher. Aus Sicht der Montage sind Durchgangsbohrungen häufiger und einfacher herzustellen als Sacklöcher. In Bezug auf die Formgestaltung sind Durchgangsbohrungen strukturell einfacher. Sie können mit Kernen hergestellt werden, die sowohl im beweglichen als auch im festen Teil der Form befestigt sind, oder mit einem einzigen Kern in beiden Teilen. Im ersten Fall entstehen unter der Einwirkung des geschmolzenen Kunststoffs zwei freitragende Balken mit kurzen Schenkeln, was zu einer minimalen Verformung führt.
Letztere bilden in der Regel einen einfach gestützten Balken und weisen ebenfalls eine minimale Verformung auf. Bei der Verwendung von zwei Kernen sollten deren Durchmesser leicht unterschiedlich sein, um eine Fehlausrichtung zu vermeiden und glatte Passflächen zu gewährleisten. Sacklöcher, die mit einem freitragenden Balkenkern hergestellt werden, neigen eher dazu, sich unter dem Aufprall des geschmolzenen Kunststoffs zu verbiegen, was zu unregelmäßig geformten Löchern führt. Im Allgemeinen sollte die Tiefe eines Sacklochs das Doppelte seines Durchmessers nicht überschreiten. Bei Sacklöchern mit einem Durchmesser von 1,5 mm oder weniger sollte die Tiefe nicht größer sein als der Durchmesser. Die Wandstärke am Boden eines Sacklochs sollte mindestens ein Sechstel des Lochdurchmessers betragen, um Schrumpfung zu vermeiden.
3. Seitenlöcher
Seitliche Löcher werden in der Regel mit seitlichen Kernen geformt, was die Werkzeugkosten und den Wartungsaufwand erhöhen kann, insbesondere wenn die seitlichen Kerne lang und bruchgefährdet sind. Falls möglich, kann das Design wie in Abbildung 6 gezeigt verbessert werden, um diese Probleme zu entschärfen.
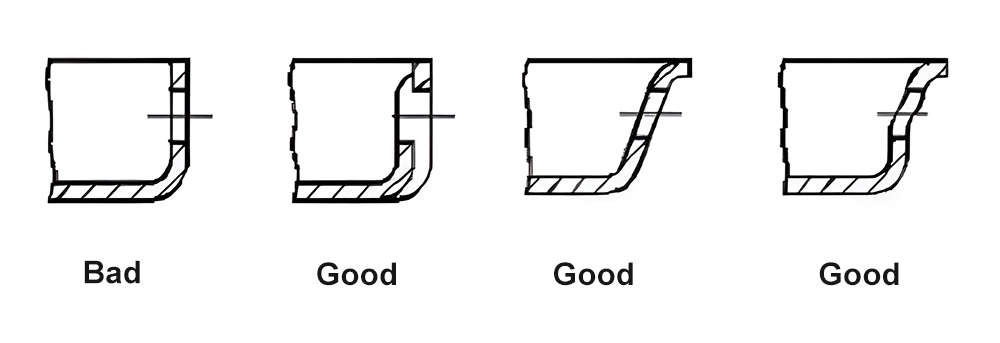
Vorsprünge in der Kunststoffteilkonstruktion
Chefsdie in der Regel aus der Wandstärke herausragen, werden zum Zusammenbau von Produkten, zum Trennen von Gegenständen und zum Halten anderer Teile verwendet. Hohle Vorsprünge können Einsätze aufnehmen oder Schrauben festziehen. Diese Anwendungen erfordern eine ausreichende Festigkeit, um dem Druck standzuhalten, ohne zu brechen. Vorsprünge sind im Allgemeinen zylindrisch, da diese Form leichter zu formen ist und bessere mechanische Eigenschaften aufweist.
Integration mit Struktur
Idealerweise sollten Aufsätze nicht als isolierte Zylinder konstruiert werden. Sie sollten mit den Außenwänden verbunden sein oder in Verbindung mit Rippen verwendet werden. Dieser Ansatz erhöht die Festigkeit des Aufsatzes und erleichtert den reibungslosen Fluss des Kunststoffs. Die Verbindung mit der Außenwand sollte eine dünnwandige Verbindung sein, um Schrumpfung zu vermeiden.
Die Basis der Nabe, wo sie auf das Grundmaterial trifft, sollte einen Ausrundungsradius von 0,4 bis 0,6 mal der Dicke des Grundmaterials haben. Die Wandstärke des Aufsatzes sollte zwischen dem 0,5- und 0,75-fachen der Dicke des Grundmaterials liegen. Die Oberseite des Aufsatzes sollte eine Fase aufweisen, um die Montage der Schrauben zu erleichtern. An den Naben sind auch Entlastungswinkel erforderlich. Diese Konstruktionsanforderungen ähneln denen für Rippen, so dass Vorsprünge eine Variante der Rippen sind. Diese Zusammenhänge sind in den Abbildungen 7 und 8 dargestellt.
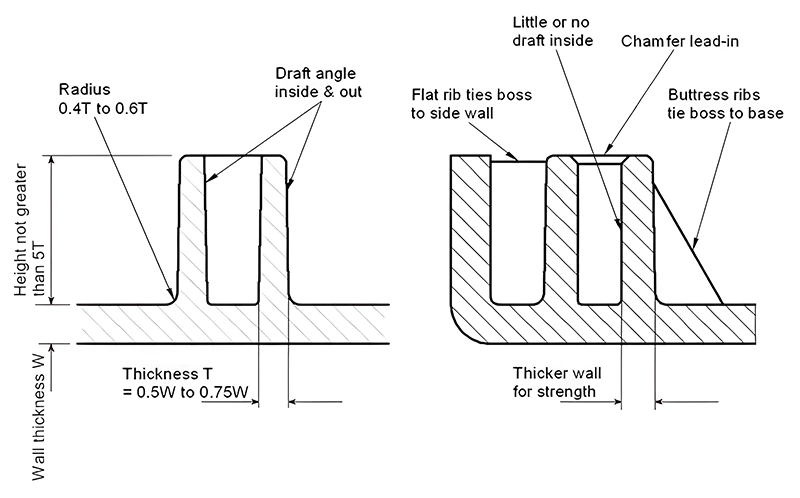
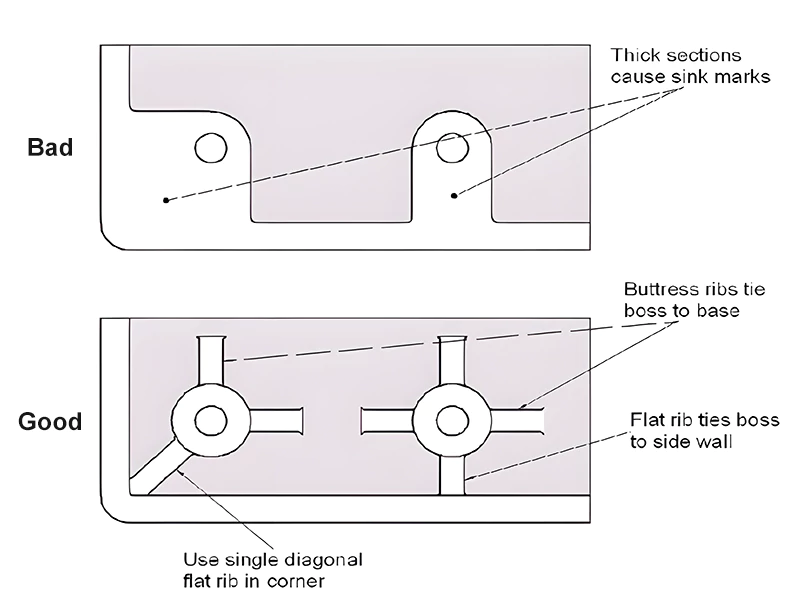
Gewindebuchsen für selbstschneidende Schrauben
Viele Vorsprünge werden für die Verbindung von selbstschneidenden Schrauben verwendet. Die Innengewinde dieser Vorsprünge werden im Kaltfließverfahren hergestellt, bei dem der Kunststoff verformt wird, ohne ihn zu schneiden. Die Größe der Gewindebuchse muss der Einschraubkraft der Schraube und der von ihr getragenen Last standhalten. Der Lochdurchmesser im Gewindezapfen muss gewährleisten, dass die Schraube auch unter bestimmten Drehmoment- und Vibrationsbedingungen fest sitzt.
Der Außendurchmesser der Nabe muss der beim Anziehen der Schraube entstehenden Umfangskraft standhalten, ohne zu brechen. Um das Eindrehen der Schraube zu erleichtern, wird häufig eine Aussparung an der Oberseite des Vorsprungs angebracht, die etwas größer ist als der Nenndurchmesser des Gewindes. Die Berechnung der Abmessungen einer Nabe kann kompliziert sein.
Es wird eine vereinfachte Schätzungsmethode von einer ausländischen Website empfohlen, die auf dem Nenndurchmesser der Schraube basiert. Bestimmen Sie zunächst das verwendete Material und wenden Sie dann den entsprechenden Koeffizienten aus der Tabelle auf den Nenndurchmesser der Schraube an, um die geeignete Größe zu ermitteln.
Schnappverbindungen in der Kunststoffteilkonstruktion
Die Schnappmontage ist eine bequeme, kostengünstige und umweltfreundliche Methode der Verbindung. Die Snap-Fit-Komponenten werden gleichzeitig mit dem Produkt gegossen, so dass keine zusätzlichen Befestigungselemente wie Schrauben benötigt werden. Bei der Montage werden die entsprechenden Teile einfach zusammengesteckt.
Das Prinzip der Schnappverbindung besteht darin, dass ein vorstehender Teil eines Bauteils an einem Hindernis auf einem anderen Bauteil vorbeigeschoben wird. Bei diesem Vorgang kommt es zu einer elastischen Verformung. Sobald das Hindernis überwunden ist, schnappen die Teile wieder in ihre ursprüngliche Form zurück und verriegeln sich, wie in Abbildung 9 dargestellt. Schnappverbindungen können entweder dauerhaft oder lösbar sein.

Strukturell lassen sich Schnappverschlüsse in freitragende, ringförmige und kugelförmige Verschlüsse einteilen, wie in Abbildung 10 dargestellt.
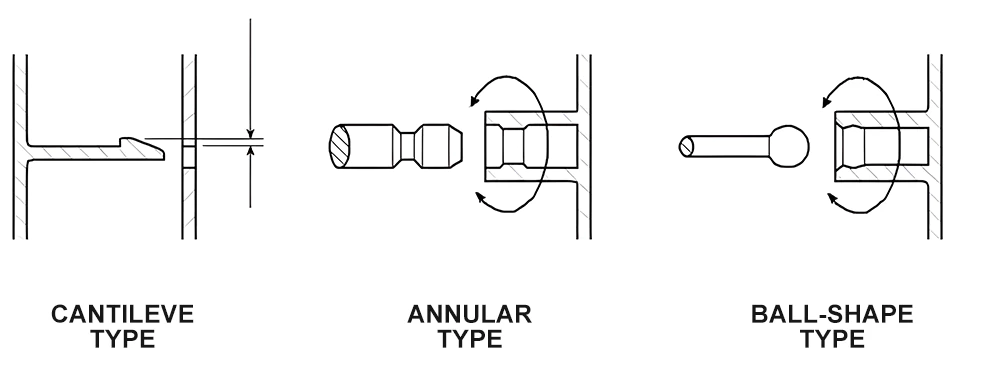
Wichtige Winkel und Berechnungen
1. Kritische Winkel
Zwei kritische Winkel bei der Konstruktion von Schnappverschlüssen sind die Einzugsseite und die Eintrittsseite. Im Allgemeinen wird eine größere Rückzugsseite bevorzugt, um einen sicheren Sitz zu gewährleisten. Wenn sich die Rückzugsseite einem Winkel von 90 Grad nähert, wird der Schnappverschluss dauerhaft, wie in Abbildung 11 dargestellt.
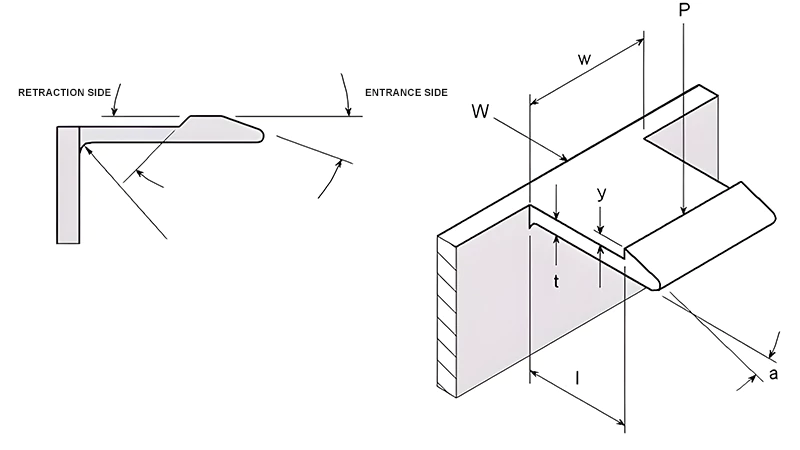
2. Berechnungen für Snap-Fits
Die maximal zulässige Durchbiegung für einen Schnappverschluss mit gleichmäßigem Querschnitt kann wie folgt berechnet werden: Y = el² / (1,5t). Diese Formel geht davon aus, dass die Verformung nur im Schnapphaken stattfindet. In der Praxis tritt eine gewisse Verformung auch in der Nähe des Karabinerhakens auf, die als Sicherheitsfaktor betrachtet werden kann.
Die Kraft, die erforderlich ist, um eine Verformung Y des Schnappverschlusses zu erzeugen: P = wt²Ee / (6l).
Die Montagekraft kann geschätzt werden mit: W = P(μ + tga) / (1 - tga).
Für lösbare Schnappverschlüsse kann die Auslösekraft mit denselben Formeln berechnet werden, wobei der Winkel a durch den Winkel b ersetzt wird.
Tabelle 2 enthält einige für diese Berechnungen erforderliche Koeffizienten.
Materialien | (e)(%) | GPa | Reibungskoeffizient(en) |
PS | 2 | 3.0 | 0.3 |
ABS | 2 | 2.1 | 0.2 |
SAN | 2 | 3.6 | 0.3 |
PMMA | 2 | 2.9 | 0.4 |
LDPE | 5 | 0.2 | 0.3 |
HDPE | 4 | 1.2 | 0.3 |
PP | 4 | 1.3 | 0.3 |
PA | 3 | 1.2 | 0.1 |
POM | 4 | 2.6 | 0.4 |
PC | 2 | 2.8 | 0.4 |
3. Ringförmige Schnappverschlüsse
Ringförmige Schnappsitze verwenden die inneren Vorsprünge eines Rings, um in die Nut einer Welle einzugreifen. Je nach Auslösewinkel können sie entweder lösbar oder nicht lösbar sein. Der Ring dehnt sich beim Einsetzen und Herausnehmen elastisch aus und besteht in der Regel aus Materialien mit guter Elastizität.
In Abbildung 12 ist ein ringförmiger Schnappverschluss dargestellt.
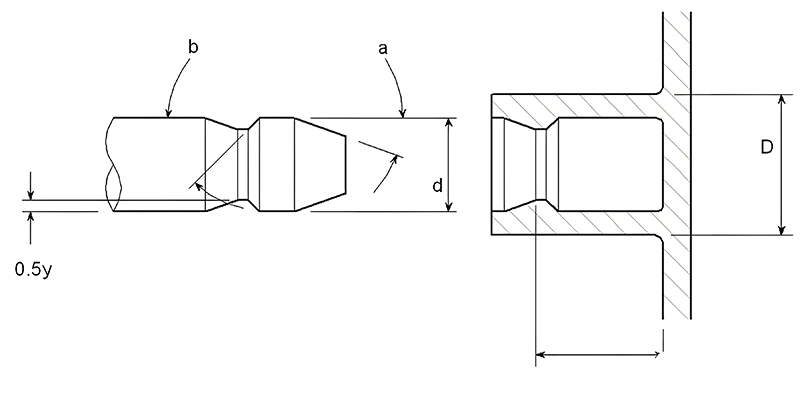
Die maximale Größe des Vorsprungs des ringförmigen Schnappverschlusses lässt sich wie folgt berechnen:
y = Sd((K + v) / E + (1 - v) / E) / K
S ist die Bemessungsspannung, v ist die Poissonzahl, E ist der Elastizitätsmodul und K ist ein geometrischer Koeffizient, der wie folgt berechnet wird: K = (1 + (d/D)²) / (1 - (d/D)²).
Die Expansionskraft auf die Hülse kann mit berechnet werden:
P = (tan a + μ) / Sydlπ / K
Dabei ist μ der Reibungskoeffizient.
In Tabelle 2 sind die Poisson-Zahlen für verschiedene ungefüllte Materialien aufgeführt, wobei die Reibungskoeffizienten in Abbildung 17 dargestellt sind.
Interferenzpassungen bei der Konstruktion von Kunststoffteilen
Presspassungen, die zur Verbindung von Bohrungen und Wellen verwendet werden, eignen sich zur Übertragung von Drehmomenten und anderen Kräften. Diese Art der Verbindung ist bequem und einfach. Die wichtigste Überlegung bei der Konstruktion von Presspassungen ist das Ausmaß des Übermaßes: Ein zu geringes Übermaß führt zu unzuverlässigen Verbindungen, während ein zu großes Übermaß die Montage erschwert und die Gefahr von Rissen erhöht.
Bei der Konstruktion von Presspassungen ist es wichtig, die Toleranzen der Bohrung und der Welle sowie die Betriebstemperatur zu berücksichtigen, da Temperaturschwankungen das Übermaß erheblich beeinflussen können. Die meisten Wellen sind aus Metall, und um eine zuverlässige Verbindung zu gewährleisten, ist es üblich, Rändelungen oder Rillen auf der Gegenwelle anzubringen. Die allgemeine Formel zur Berechnung des Übermaßes lautet:
Y = Sd((K + v) / E) / K
Dabei ist S die Bemessungsspannung, v die Poissonzahl, E der Elastizitätsmodul und K ein geometrischer Koeffizient, der wie folgt berechnet wird:
K = (1 + (d/D)²) / (1 - (d/D)²)
Die Montagekraft kann mit berechnet werden:
W = Sdlπμ / K
Dabei ist μ der Reibungskoeffizient und l die Länge des Eingriffs. Die Poissonzahl ist der Tabelle 3 zu entnehmen.
Materialien | Querkontraktionszahl |
PS | 0.38 |
PMMA | 0.4 |
LDPE | 0.49 |
HDPE | 0.47 |
PP | 0.43 |
PA | 0.45 |
PC | 0.42 |
PVC | 0.42 |
PPO | 0.41 |
PPS | 0.42 |
Stahl | 0.38 |
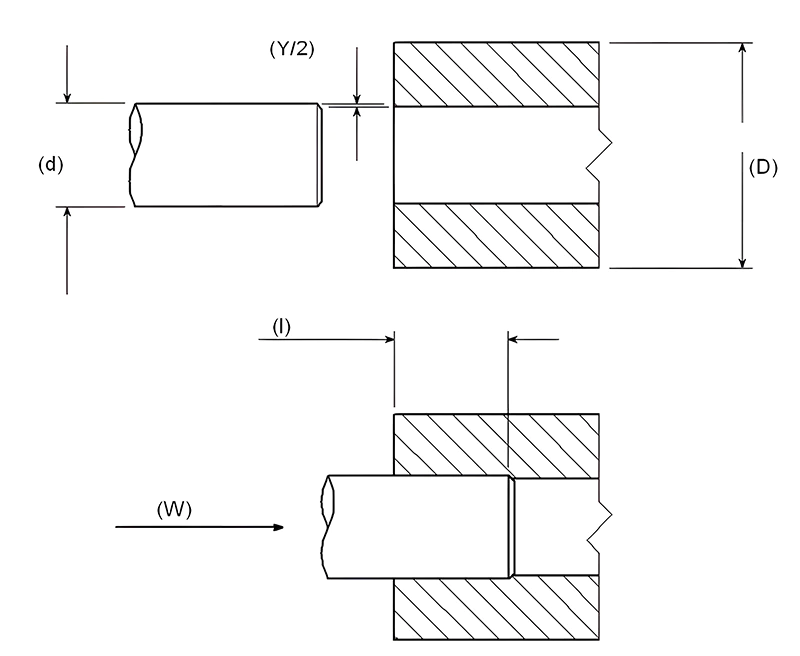
Neben der Presspassung gibt es weitere Verfahren zum Verbinden von Kunststoffteilen, wie z. B. Heißkleben, Schweißen und Ultraschallschweißen. Jedes dieser Verfahren hat seine eigenen Vorteile und eignet sich je nach den Materialeigenschaften und den Anforderungen der Baugruppe für unterschiedliche Anwendungen.
Auswirkungen von Toleranzen und Materialauswahl bei der Konstruktion von Kunststoffteilen
Bei den meisten Kunststoffprodukten lassen sich präzise Maßtoleranzen erzielen. Bei Materialien mit hohen Schrumpfungsraten oder weicheren Materialien kann die Kontrolle jedoch schwieriger sein. Beim Produktdesign müssen die Einsatzumgebung, das Kunststoffmaterial und die Produktform berücksichtigt werden, um angemessene Toleranzen festzulegen. Mit den steigenden Anforderungen der Kunden muss sich auch das Konzept der Passform und des Finishs weiterentwickeln. Ziel ist es, ein Gleichgewicht zwischen Passform, Präzision und Ästhetik zu erreichen.
Das Spritzgießen wird im Allgemeinen in drei Qualitätsstufen eingeteilt: allgemeine, mittelpräzise und hochpräzise.
- Allzweckformteile: Dies erfordert ein geringeres Maß an Qualitätskontrolle, was sich in niedrigeren Ausschussraten und schnelleren Produktionszyklen niederschlägt.
- Mittelpräzises Gießen: Teurer aufgrund höherer Anforderungen an Formen und Produktionsverfahren, die häufige Qualitätskontrollen erfordern.
- Hochpräzises Gießen: Dies erfordert präzise Formen, optimale Produktionsbedingungen und eine kontinuierliche Produktionsüberwachung. Dies wirkt sich auf den Produktionszyklus aus und erhöht die Kosten für die Stückproduktion und die Qualitätskontrolle. Die Konstrukteure müssen ein Gleichgewicht zwischen Präzision und wirtschaftlichen Produktionskosten finden, indem sie häufig die Toleranzen für unkritische Abmessungen lockern und gleichzeitig die Anforderungen an Leistung, Aussehen und Passform erfüllen.
Auswahl des Materials
Es gibt keine von Natur aus schlechten Materialien, sondern nur ungeeignete Entscheidungen für bestimmte Anwendungen. Die Konstrukteure müssen die Eigenschaften der verfügbaren Materialien genau kennen und sie sorgfältig testen, um ihre Auswirkungen auf die Leistung der geformten Produkte zu untersuchen.
Die beim Spritzgießen am häufigsten verwendeten Materialien sind Thermoplaste, die in amorphe und teilkristalline Kunststoffe unterteilt werden. Diese beiden Kategorien unterscheiden sich erheblich in der Molekularstruktur und der Leistung, die durch die Kristallisation beeinflusst wird. Teilkristalline Thermoplaste werden in der Regel für Teile verwendet, die eine hohe mechanische Festigkeit erfordern, während amorphe Thermoplaste, die weniger anfällig für Biegungen sind, häufig für Gehäuse verwendet werden.
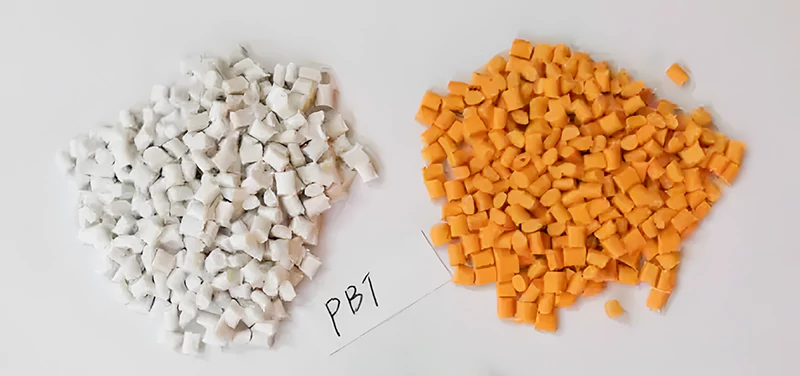
Thermoplaste sind in unverstärkten, glasfaserverstärkten und mit Mineralien oder Glaskugeln gefüllten Varianten erhältlich. Glasfasern erhöhen vor allem die Festigkeit, Steifigkeit und Temperaturbeständigkeit; Mineral- und Glasfasern verringern die Verformung, bieten aber eine geringere Verstärkung. Spezifische Änderungen der Eigenschaften aufgrund von Verstärkungen sollten von den Materiallieferanten oder durch Experimente bestätigt werden.
Einige Thermoplaste, insbesondere PA6 und PA66, sind stark hygroskopisch, was ihre mechanischen Eigenschaften und ihre Maßhaltigkeit erheblich beeinträchtigen kann.
Überlegungen im Zusammenhang mit der Verarbeitung und Montage sind von entscheidender Bedeutung. Die Integration mehrerer Funktionen in ein einziges Bauteil kann kostspielige Montagekosten einsparen. Dieses Prinzip ist für die Kalkulation der Produktionskosten von Vorteil. Hochleistungswerkstoffe (Steifigkeit, Zähigkeit) können dünnere Wandstärken ermöglichen und damit die Produktionszyklen verkürzen. Deshalb ist es wichtig, alle Normen aufzulisten und systematisch zu bewerten.
Verrundungen und abgerundete Ecken bei der Konstruktion von Kunststoffteilen
Scharfe Ecken führen oft zu Defekten und Spannungskonzentrationen in Kunststoffteilen, die bei Belastung oder Aufprall zu Brüchen führen können. Größere abgerundete Ecken (Verrundungen) bieten eine Lösung für dieses Problem. Sie verringern nicht nur die Spannungskonzentration, sondern erleichtern auch das Fließen des Kunststoffs beim Gießen und das Auswerfen des fertigen Produkts.

Wenn die Innenecke abgerundet und die Außenecke scharfkantig ist, ist der Bereich an der Kurve immer noch dicker als die anderen Teile, was zu einer Schrumpfung führt. Eine Lösung besteht darin, sowohl die Innen- als auch die Außenecke abzurunden, um eine einheitliche Wandstärke zu erreichen. In diesem Fall ist der Außenradius die Summe aus dem Innenradius und der Grundwanddicke.
Die Konstruktionsprinzipien für Eckradien gelten auch für freitragende Schnappverbindungen. Bei diesen Schnappverbindungen muss sich der Kragarm biegen und in die richtige Position bringen lassen. Ist der Eckenradius (R) zu klein, kann dies zu einer übermäßigen Spannungskonzentration führen, so dass das Produkt beim Biegen bruchgefährdet ist. Umgekehrt kann ein zu großer Radius zu Lunkerstellen und Lücken führen. Daher gibt es ein bestimmtes Verhältnis zwischen dem Eckenradius und der Wandstärke, das in der Regel zwischen 0,2 und 0,6 liegt, wobei der ideale Wert bei 0,5 liegt.
Schlussfolgerung
Zusammenfassend wurden in diesem Artikel verschiedene kritische Aspekte der strukturellen Konstruktion von Spritzgussteilen behandelt, darunter Wandstärke, Entformungswinkel, Rippen, Löcher, Vorsprünge, Schnappverbindungen, Presspassungen, Toleranzen und abgerundete Ecken. Jedes dieser Elemente spielt eine entscheidende Rolle für die Gesamtfunktionalität, Haltbarkeit und Qualität des Endprodukts.
Es ist jedoch wichtig, sich daran zu erinnern, dass die Tragwerksplanung auch durch Umweltfaktoren, spezifische Bedingungen und einzigartige Anforderungen jedes Projekts beeinflusst wird. Diese Faktoren erfordern eine maßgeschneiderte Herangehensweise an jede Planungsaufgabe.
Ziel dieses umfassenden Überblicks ist es, angehende und praktizierende Konstrukteure mit dem Wissen und den Erkenntnissen auszustatten, die sie benötigen, um in ihrem Fachgebiet zu brillieren. Durch das Verständnis und die Anwendung dieser Prinzipien können Konstrukteure effektivere, zuverlässigere und hochwertigere Spritzgussteile herstellen.
Eine Antwort
Ihr Blog ist immer ein Highlight meines Tages