Spritzgießen ist ein Eckpfeiler der Herstellung von Kunststoffteilenund spielen eine zentrale Rolle in verschiedenen Branchen. Von medizinische Ausrüstung zu Automobilinnenräume, Elektronikgehäuse zu alltägliche Haushaltswarenund darüber hinaus ist die Allgegenwart von Spritzgussteilen unbestreitbar.
Das Verfahren umfasst das Schmelzen von Rohkunststoff in einem SpritzgießmaschineDas Material wird dann in einer Form geformt, abgekühlt und verfestigt, so dass kompliziert geformte Bauteile entstehen.
Die Komplexität der Konstruktion von Kunststoffteilen erfordert eine sorgfältige Beachtung verschiedener Faktoren, einschließlich funktionaler Anforderungen, Materialauswahl und struktureller Überlegungen. Zu den Schlüsselelementen, die für diesen Entwurfsprozess entscheidend sind, gehören Wandstärke, Entwurf, Texturen, Rippen und vor allem, Chefs.
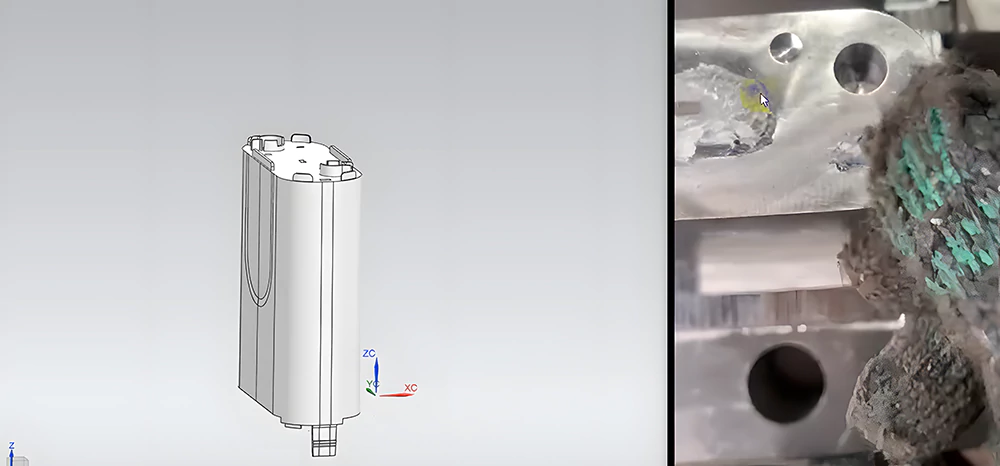
Naben, die als Befestigungs- und Montagepunkte dienen, sind in der Regel zylindrische Vorsprünge mit strategisch platzierten Löchern für Schrauben oder Gewindeeinsätze. Die Gewährleistung eines effektiven Designs ist von größter Bedeutung und erfordert großzügige Basisradien für die Festigkeit und einen ausreichenden Durchzug für die nahtlose Entnahme der Teile aus der Form.
Dieser Blog befasst sich mit den grundlegenden Leitlinien für Chefdesign in Spritzgussteilen mit dem Ziel, die Formbarkeit zu verbessern, die Lebensdauer der Form zu verlängern, die Lebensdauer der Teile zu erhöhen und die Herstellungskosten zu senken.
Chefdesign: Ein kurzer Überblick
Aus Kunststoff FormteilkonstruktionEin entscheidendes Element, das Aufmerksamkeit erfordert, ist das Konzept der Chefdesign. Was genau ist ein Vorsprung in Formteilen? Im Kern ist ein Vorsprung ein Strukturmerkmal - ein zylindrischer Vorsprung mit strategisch platzierten Löchern in Formteilen.
Die Hauptfunktion von Vorsprüngen besteht darin, Befestigungspunkte für Schrauben, Befestigungselemente oder andere wichtige Montageteile bereitzustellen. Diese Merkmale spielen eine entscheidende Rolle bei der Erleichterung reibungsloser Montageprozesse und gewährleisten gleichzeitig die strukturelle Integrität des Endprodukts.
Das Verständnis und die Beherrschung der Nabenkonstruktion sind für die Optimierung der Funktionalität und der Herstellbarkeit von Kunststoffformteilen unerlässlich.
Boss Designelemente
Ein effektives Nabendesign ist von zentraler Bedeutung für die strukturelle Integrität von Gussteilen. Um eine optimale Festigkeit ohne Beeinträchtigung des Gesamtdesigns zu erreichen, müssen mehrere Schlüsselelemente sorgfältig berücksichtigt werden:
Dicken-Verhältnis
Die Wandstärke von Aufsätzen sollte 60 % der Hauptwandstärke des Teils nicht überschreiten. Dieses Gleichgewicht ist entscheidend, um die Festigkeit des Aufsatzes zu gewährleisten, ohne die strukturelle Gesamtintegrität des Formteils zu beeinträchtigen.
Basis-Radius-Verhältnis
Die Stabilität und die Vermeidung von Verformungen während der Herstellung hängen stark vom Verhältnis des Basisradius ab. Der Bodenradius sollte mindestens 25 % der Hauptwanddicke betragen, um eine stabile Grundlage zu schaffen. Dies entspricht einem Bodendurchmesser von mindestens 50 %, was zur Gesamtbelastbarkeit der Nabe beiträgt.
Verbindung zu angrenzenden Wänden
Aufsätze sollten immer durch Rippen oder Zwickel mit den angrenzenden Wänden verbunden werden. Diese strategische Verbindung trägt dazu bei, die Entstehung dicker Abschnitte zu vermeiden und das Risiko des Verziehens während des Herstellungsprozesses zu minimieren. Ein durchdachtes Design gewährleistet eine nahtlose Integration der Aufsätze in die Gesamtstruktur des Teils.
Filetierverhältnis an der Basis
Als Befestigungspunkt zwischen zwei Oberflächen erfordert die Basis von Aufsätzen eine Filetierverhältnis für zusätzliche Festigkeit. Diese Präventivmaßnahme schützt vor potenziellen Spannungen, die durch das Einsetzen von Schrauben oder anderen Beschlägen verursacht werden, und sorgt für Elastizität und minimiert das Risiko von Brüchen.
Die Einbeziehung eines Verrundungsverhältnisses ist ein entscheidender Schritt, um die Langlebigkeit und Zuverlässigkeit des Vorsprungs im Formteil zu erhöhen.
10 kritische Boss-Designrichtlinien für geformte Kunststoffteile
1. Mindestradius an der Basis des Aufsatzes
Die Einführung einer Verrundung mit einem bestimmten Mindestradius an der Basis eines Vorsprungs ist zwingend erforderlich, um die Spannungskonzentration zu verringern. Dieser Radius wird strategisch an der Stelle platziert, an der sich die Aufkantung mit der Nennwand überschneidet, wodurch Spannungen effektiv reduziert und die strukturelle Integrität insgesamt verbessert werden.
Der Radius sorgt zwar für Festigkeit, sollte aber sorgfältig kontrolliert werden, um dicke Abschnitte zu vermeiden und ein Gleichgewicht zwischen struktureller Unterstützung und Herstellbarkeit herzustellen. Der empfohlene Bereich für diesen Basisradius ist das 0,25- bis 0,5-fache der nominalen Wandstärke, um eine optimale Leistung während des Formprozesses zu gewährleisten.
2. Abstände zwischen den Bossen
Die strategische Platzierung von Vorsprüngen ist entscheidend, um die Entstehung von dünnen Bereichen zu verhindern, die den Kühlprozess erschweren. Die Einhaltung eines angemessenen Abstands zwischen den Vorsprüngen, der idealerweise mindestens das Zweifache der Nennwandstärke beträgt, ist für eine effiziente Kühlung und Qualitätsverbesserung unerlässlich.
Die Nähe zwischen den Chefs kann zu Schwierigkeiten bei der Kühlung führen, was sich auf die Produktivität und Formstabilität. Der richtige Abstand ist der Schlüssel zur Gewährleistung einer gleichmäßigen Kühlung und zur Verbesserung der Langlebigkeit der Form.
3. Radius an der Basis des Lochs im Aufsatz
Die Einführung eines Radius an der Basis des Lochs in einem Aufsatz dient mehreren Zwecken, unter anderem der Vermeidung von scharfe Ecken und Spannungskonzentration. Dieses Konstruktionsmerkmal unterstützt den Formgebungsprozess und trägt zur Spannungsreduzierung bei, wodurch die Langlebigkeit des Formteils gewährleistet wird.
Der empfohlene Radius an der Basis des Lochs in der Nabe liegt im Bereich des 0,25- bis 0,5-fachen der Nennwanddicke, wodurch ein Gleichgewicht zwischen Herstellbarkeit und Spannungsabbau erreicht wird.
4. Minimaler Tiefgang für Boss OD
Um ein leichtes Ausstoßen aus der Form zu gewährleisten, ist ein geeigneter Luftzug am Aufsatz erforderlich. Außendurchmesser (OD). Dieser Zug, der in der Regel größer oder gleich 0,5 Grad ist, erleichtert einen reibungslosen Entformungsprozess.
Ein angemessener Verzug an der Außenfläche des Aufsatzes vereinfacht nicht nur die Herstellung, sondern trägt auch zur Effizienz des Spritzgießprozesses bei und minimiert die Produktionsprobleme.
5. Mindestentwurf für Boss ID
Konstruktive Überlegungen erfordern häufig eine Mindestkonizität des Innendurchmessers (ID) eines Nockens, um einen ordnungsgemäßen Eingriff mit den Befestigungselementen zu gewährleisten.
Es wird empfohlen, an den Innenwänden der Nabe eine Verformung von mindestens 0,25 Grad vorzusehen, um eine nahtlose Entformen und die Herstellung eines sicheren Sitzes für Verbindungselemente. Dieser Entwurf auf der Innenseite trägt sowohl zur Herstellbarkeit als auch zur Funktionalität des fertigen Formteils bei.
6. Verhältnis von Aufsatzhöhe zu Außendurchmesser
Das richtige Gleichgewicht zwischen der Höhe der Nabe und dem Außendurchmesser (OD) ist entscheidend für die Vermeidung unerwünschter Werkstoffmasse und dicke Bretter an der Basis.
Mit einer empfohlenen Höhe von weniger als dem Dreifachen des Außendurchmessers unterstützt diese Konstruktionsrichtlinie eine effektive Kühlung, reduzierte Zykluszeitund Maßgenauigkeit für Kernbohrungen. Eine richtige Verhältnis Höhe zu Außendurchmesser ist für eine optimale Leistung des Teils unerlässlich.
7. Minimaler Radius an der Spitze des Aufsatzes
Um unterschiedlichen Belastungen unter Betriebsbedingungen standhalten zu können, ist eine Verrundung mit einem bestimmten Mindestradius an der Spitze eines Vorsprungs unerlässlich. Dieses Konstruktionsmerkmal reduziert effektiv die Spannungskonzentration und erhöht die allgemeine Haltbarkeit und Lebensdauer des Formteils.
Der empfohlene Mindestradius an der Spitze trägt zur Gesamtbelastbarkeit der Nabe unter verschiedenen Belastungsszenarien bei.
8. Fase an der Oberseite des Aufsatzes
Die Einbeziehung einer Fase an der Oberseite eines Vorsprungs ist eine vorteilhafte Einführung für Befestigungselemente während des Montageprozesses. Dieses Konstruktionsmerkmal gewährleistet ein reibungsloses Einrasten und Ausrichten während der Montage und rationalisiert den Fertigungsprozess.
Die Fase an der Oberseite des Vorsprungs trägt zur einfachen Montage und zur Gesamtqualität des fertigen Formteils bei.
9. Wanddicke des Aufsatzes
Unter Beibehaltung einer idealen Wanddicke für Naben, etwa 60 Prozent der Nennwandist entscheidend für die Vermeidung von Problemen wie entfällt, Einfallstellenund verlängerte Zykluszeiten.
Während eine Überschreitung dieser Dicke zu Problemen bei der Herstellung führen kann, kann eine Anpassung der Wanddicke für Vorsprünge in nicht sichtbaren Bereichen in Betracht gezogen werden, um eine höhere Belastung durch selbstschneidende Schrauben zu ermöglichen. Das richtige Gleichgewicht bei der Wanddicke ist für eine optimale Leistung des Teils entscheidend.
10. Eigenständiger Chef
Es wird empfohlen, Aufsätze und andere dicke Abschnitte zu entkernen, um einen gleichmäßigen Materialfluss und eine gleichmäßige Lastverteilung zu gewährleisten. Die Befestigung des Vorsprungs an der Seitenwand erhöht die Steifigkeit und den Materialfluss und trägt so zur strukturellen Integrität des Formteils bei.
Diese konstruktive Überlegung ist entscheidend für eine bessere Leistung und Herstellbarkeit der Teile.
Herausforderungen und Lösungen beim Boss-Design
Die unsachgemäße Gestaltung von Aufsätzen birgt Herausforderungen, die sich erheblich auf die Ästhetik und Funktionalität von Formteilen auswirken können. Worin bestehen diese Probleme? Wie können Sie sie lösen? Das wollen wir im Folgenden erkunden.
Verursachung von Sinkspuren und Verzug
Herausforderung
Eine der größten Herausforderungen bei der Konstruktion von Naben ist die Gefahr von Einfallstellen und Verwerfungen. Wenn Aufsätze unzureichend konstruiert sind - entweder zu dick oder ohne angemessene Verstärkung - kühlen sie anders ab als die umliegenden Bereiche.
Diese Temperaturunterschiede können zu unansehnlichen Einfallstellen, zu Vertiefungen auf der Oberfläche und zu Verzug führen, wodurch das Teil von seiner vorgesehenen Form abweicht.
Lösung
Um diese Herausforderung zu meistern, muss die Wandstärke der Naben optimiert und Verstärkungsrippen eingearbeitet werden. Die richtige Wandstärke gewährleistet eine gleichmäßige Kühlung und minimiert das Risiko von Einfallstellen und Verzug. Verstärkungsrippen sind entscheidend für die gleichmäßige Verteilung der Spannung über die Nabe, verhindern lokale Verformungen und verbessern die Gesamtintegrität des Teils.
Auswirkung auf Abkühlzeit und Zykluszeit
Herausforderung
Vorsprünge haben einen direkten Einfluss auf die Kühl- und Zykluszeiten während des Formgebungsprozesses. In Fällen, in denen Vorsprünge übermäßig dick oder schlecht konstruiert sind, können sie Wärme speichern, was zu verlängerten Kühl- und Zykluszeiten führt.
Dies verlangsamt nicht nur den Herstellungsprozess, sondern führt auch zu erhöhte Produktionskosten.
Lösung
Um die Auswirkungen auf die Kühlung und die Zykluszeiten zu minimieren, sind strategische Anpassungen der Kühlkanäle in der Form erforderlich. Durch die Optimierung des gesamten Werkzeugdesigns, mit besonderem Augenmerk auf die Platzierung der Vorsprünge, können die negativen Auswirkungen auf die Kühlung und die Zykluszeiten minimiert werden.
Eingeschränkte Materialauswahl und Kompatibilität
Herausforderung
Das für die Formteile gewählte Material hat einen erheblichen Einfluss auf die Gestaltung der Naben. Die Wahl eines inkompatiblen Materials kann den Aufsatz einer übermäßigen Belastung aussetzen, was zu Rissen oder Versagen führen kann.
Lösung
Bei der Bewältigung dieser Herausforderung geht es um die Auswahl der richtiges Material für Chefdesign. Entscheiden Sie sich für ein Material mit der erforderlichen Festigkeit, Steifigkeit und chemischen Beständigkeit, um sicherzustellen, dass die Nabe den Belastungen und Umgebungsbedingungen standhalten kann.
Die Auswahl des Materials ist entscheidend für dauerhafte und zuverlässige Aufsatzkonstruktionen bei Formteilen.
Schlussfolgerung
Vorsprünge in Spritzgussteilen sind von entscheidender Bedeutung, da sie als Verankerungen, Stützen und Erleichterungen für eine zuverlässige Montage dienen. Diese Komponenten spielen eine entscheidende Rolle bei der Gewährleistung der strukturellen Integrität und der optimalen Leistung des Endprodukts.
Die Einhaltung grundlegender Konstruktionsrichtlinien ist unerlässlich, um Kunststoffteile mit robusten, funktionalen und optisch ansprechenden Aufsätzen herzustellen.
Für alle, die qualitativ hochwertige Formteile mit einer zuverlässigen Nabenausführung suchen, Prototool als die optimale Wahl herausstellt. Unser Spritzgießdienstleistungen werden von einem erfahrenen Team unterstützt, das auf Ihre spezifischen Anforderungen eingeht. Möchten Sie mehr erfahren? Nehmen Sie noch heute Kontakt auf!