Die Konstruktion von Zahnradformen, insbesondere für Kunststoffzahnräder, unterscheidet sich erheblich von herkömmlichen Formen. Schlüsselparameter wie Zahndicke (die Bogenlänge zwischen zwei Seiten eines Zahnradzahns), Modul (ein Parameter zur Messung der Zahnradgröße) und Eingriffswinkel (der spitze Winkel zwischen Kraft- und Bewegungsrichtung, ohne Reibung) erfordern Anpassungen auf der Grundlage empirischer Daten.
Im Gegensatz zu anderen Verfahren können Zahnradformen nicht direkt auf der Grundlage von Schwindungsraten bearbeitet werden. Professionelle Zahnrad- und Getriebehersteller haben auf der Grundlage ihrer langjährigen Erfahrung und in Zusammenarbeit mit Computersoftwareunternehmen spezielle Software für die Berechnung der Hohlraumparameter von Zahnrädern entwickelt. Diese Software kann direkt Zahnradparameter und -profile generieren, die bei der Modifizierung von Zahnrädern helfen und die Zahngenauigkeit verbessern. Lassen Sie uns einen Blick auf die Feinheiten der Konstruktion von Kunststoffzahnrädern werfen.
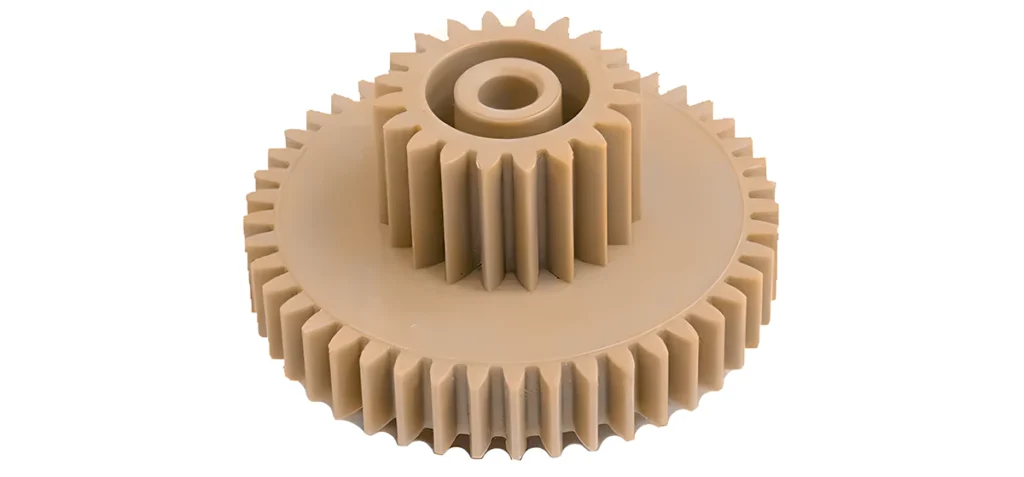
Hohlraumdesign für Kunststoffgetriebeformen
Die Gestaltung der Kavität eines Kunststoffzahnradwerkzeugs ist seit jeher eine technische Herausforderung in der Formenbauindustrie, vor allem aus zwei Gründen:
1. Präzision bei Kunststoff-Schrumpfungsraten:
Beim Gießen von Kunststoffzahnrädern geht das Kunststoffgranulat unter großer Hitze in einen geschmolzenen Zustand über und kühlt dann ab, um feste Kunststoffzahnräder zu bilden. Die Schrumpfungsrate des Kunststoffs während dieses Prozesses liegt in einer gewissen Bandbreite, so dass es schwierig ist, genaue Schrumpfungsraten zu bestimmen.
2. Nichtlineare Schrumpfungsberechnung für Formhohlräume:
Bei evolventenförmigen Kunststoffzahnradwerkzeugen mit kleinen Modulen stellt der Formhohlraum im Wesentlichen ein imaginäres Zahnrad dar. Dieses imaginäre Zahnrad unterscheidet sich sowohl von geschobenen Zahnrädern als auch von Innenzahnrädern. Nach der Schrumpfung wird es zu dem gewünschten Kunststoffzahnrad. Die Schrumpfung des Evolventenzahnprofils dieses imaginären Zahnrads ist nicht gleichmäßig wie die isotrope Schrumpfung, die man bei allgemeinen Kunststoffteilen sieht. Auf der Zahnradebene ist die Schrumpfung in x- und y-Richtung ungleich, was zu einer nichtlinearen Schrumpfung führt, wie in Abbildung 1 dargestellt. Diese Nichtlinearität erhöht die Komplexität der Konstruktion von Evolventenformen für Zahnräder aus Kunststoff erheblich.
Die richtige Art und Weise, einen Zahnradformhohlraum zu entwerfen
Angesichts dieser technischen Herausforderungen führt die Verwendung der isotropen Schwindungsmethode für die Auslegung von Formhohlräumen oft zu suboptimalen Ergebnissen. Auf der Grundlage jahrelanger praktischer Erfahrung und einer präzisen Schätzung der plastischen Schwindungsraten empfehlen wir die Verwendung der Methode der variablen Module für die theoretische Auslegung von Zahnradformkavitäten, gefolgt von einer Zahnprofilkorrektur, um die Genauigkeit und Rationalität der Formkavität sicherzustellen.
Bei der Methode der variablen Module wird davon ausgegangen, dass der Grundkreisdurchmesser, der Teilkreisdurchmesser, der Kopfkreisdurchmesser und der Fußkreisdurchmesser eines Zahnrads während der verschiedenen Bearbeitungsstufen konstant bleiben und sich proportional vergrößern oder verkleinern, ähnlich wie die radialen Maßänderungen bei einfachen hülsenförmigen Teilen. Der Teilkreisdurchmesser eines Zahnrads, der durch die Formel d=mz bestimmt wird, ist nur vom Modul m und der Anzahl der Zähne z abhängig.
Da die Anzahl der Zähne eines bestimmten Zahnrads konstant ist, können wir die Änderung des Teilkreisdurchmessers während der Bearbeitung als eine Änderung des Moduls betrachten. Dieses Prinzip impliziert, dass der Raum, den die Kavität des Kunststoffzahnrads einnimmt, ein imaginäres Zahnrad mit konstanter Zähnezahl und Eingriffswinkel ist, dessen Nuten das Zahnprofil der Kavität bilden.
Wir können den Modul dieses imaginären Zahnrads mit einer proportionalen Methode berechnen. Die Formel für diese Berechnung lautet m' = (1 + η%)m. In dieser Formel steht m' für den Modul des Zahnprofils des Formhohlraums, m ist der theoretische Modul des entworfenen Zahnrads und η% ist die Schrumpfungsrate des Kunststoffs. Durch Einsetzen des Moduls m' in die entsprechende Zahnradberechnungsformel stellt das resultierende Zahnrad das imaginäre Zahnrad des Formhohlraums dar. Die Praxis hat gezeigt, dass die Methode der variablen Module das Problem der nichtlinearen Schwindung bei Evolventenzahnprofilen wirksam löst, wie das in Abbildung 2 gezeigte Formhohlraumprodukt zeigt.
Anschnittdesign für Kunststoffzahnradformen
Beim Formen von Kunststoffzahnrädern wirkt sich die Lage des Anschnitts erheblich auf die Präzision der Zahnräder aus, insbesondere auf ihren Rundlauf. Die Verteilungsform des Anschnitts wirkt sich auch entscheidend auf die gesamten mechanischen Eigenschaften der Kunststoffzahnräder aus. Bei der Konstruktion von Anschnitten für Kunststoffzahnradformen wird, sofern das Zahnradprodukt dies zulässt, die Verwendung eines Dreipunkt-Anschnittsystems empfohlen. Idealerweise sollten diese drei Punkte auf dem gleichen Kreisbogen liegen und gleichmäßig verteilt sein, wie in Abbildung 3 dargestellt.
Bei einem ausbalancierten Dreipunkt-Anschnittsystem fließt die Kunststoffschmelze radial von den Anschnitten weg und konvergiert an den Fließfronten, um drei Schweißlinien zu bilden. An diesen Bindenähten sind die Fasern tendenziell parallel zur Fließfront ausgerichtet. Bei Zahnrädern führt dies dazu, dass die Fasern an den Bindenähten radial verteilt sind, während sie in anderen Teilen des Zahnrads unregelmäßig verteilt sind. Dadurch entstehen Bereiche mit geringer Schrumpfung entlang der Schweißnähte. Der Unterschied in der Faserorientierung zwischen den Schweißnähten und dem Rest des Zahnrads ist weniger ausgeprägt als bei Zahnrädern mit einem einzigen Anschnitt, was zu einer höheren Präzision des Zahnrads führt. Abbildung 4 zeigt einen schematischen Vergleich der Faserausrichtung und der Füllmuster bei Verwendung eines einzelnen exzentrischen Anschnitts im Vergleich zu einem gleichmäßig verteilten Dreipunktanschnitt.
Entlüftungsdesign für Kunststoffgetriebeformen
Die Entlüftung ist ein entscheidender Aspekt, der bei der Konstruktion von Kunststoffformen zu berücksichtigen ist. Bei Kunststoffzahnradformen ist die Gestaltung der Entlüftung an den Zahnflächen besonders wichtig. Wir bearbeiten die meisten Oberflächen von Zahnradformen mit einer Schleifmaschine. Dieses Verfahren gewährleistet eine gute Passung von Oberfläche zu Oberfläche. Es führt jedoch dazu, dass die letzten Bereiche während des Einspritzvorgangs nicht ausreichend gefüllt werden. Um Lufteinschlüsse zu beseitigen, ist es notwendig, Entlüftungsnuten auf den Zahnoberflächen anzulegen. In der Regel werden diese Entlüftungsrillen auf den Zahnoberflächen wie in Abbildung 5 dargestellt gestaltet.
Strukturelle Auslegung von Kunststoffgetrieben
Da beim Kunststoff-Spritzgießen von Zahnrädern häufig Punktanschnitte verwendet werden, ist die Formstruktur in der Regel eine Drei-Platten-Konstruktion. Abbildung 6 zeigt das Konstruktionsdiagramm einer Zahnradform, und Abbildung 7 zeigt die tatsächliche Zahnradform. Das Funktionsprinzip des Zahnradwerkzeugs ist wie folgt:
Nach Abschluss des Spritzgießvorgangs beginnt sich der bewegliche Teil der Form unter dem Antrieb der Spritzgießmaschine zu öffnen:
- Erste Phase des Abschieds: Durch die Wirkung der Feder 1 beginnt sich die Abstreifplatte von der Platte A zu lösen. Der Stift des Angussabziehers fixiert den Hauptkanal auf der Abstreifplatte und bewirkt, dass sich der Anschnitt vom Produkt löst.
- Zweite Stufe der Verabschiedung: Nachdem sich die Form 95 mm geöffnet hat, beginnt sich die Abstreifplatte unter der Einwirkung der Holmbaugruppe von der Frontplatte zu lösen und gibt den Hauptkanal von der Angussbuchse frei.
- Dritte Stufe der Verabschiedung: Während sich die Form weiter öffnet, beginnt sich die Platte A unter der Einwirkung der Holmbaugruppe von der Platte B zu trennen. Nach einer Öffnung von 90 mm beginnt sich die Auswerferplatte zu bewegen und wirft das Produkt aus. Während dieses Vorgangs werden die Führungssäulen der Auswerferplatte benutzt, um das Gleichgewicht des Auswurfs zu verbessern. Die Auswerferplatte wird durch die Wirkung der Feder 2 zurückgesetzt. Damit ist der gesamte Öffnungs- und Auswurfvorgang abgeschlossen.
Herstellung von Formen für Kunststoffgetriebe
Bei der Herstellung von Kunststoffzahnrädern ist die Zahnradform die wichtigste Ausrüstung für die Formgebung der Kunststoffzahnräder und die Gewährleistung ihrer Präzision. Die Kunststoffzahnradform kann in zwei Hauptteile unterteilt werden: den Zahnradhohlraum und den Formrahmen. Der Zahnradhohlraum, der auch als Zahnkranz bezeichnet wird, ist der kritischste und präziseste Teil des gesamten Herstellungsprozesses der Zahnradform.
1. Bearbeitung von Zahnradhohlräumen
Die Bearbeitung der Zahnradkavität ist der Schlüssel zur Herstellung von Kunststoffzahnradformen. Das Formen von Kunststoffzahnrädern ist eine Form der "Nachbildung". Bei diesem Verfahren ist das Zahnprofil des Hohlraums eine verformte Vorlage der Zahnradform. Daher ist es wichtig, die Maßgenauigkeit und die Oberflächenrauheit der Kavität streng zu kontrollieren. Defekte wie Grate, Exzentrizität und Oberflächenkratzer sind unbedingt zu vermeiden. Daher muss ein strenges Verfahren für die Bearbeitung von Zahnradkavitäten eingeführt werden, um die Präzision der Kavitätenherstellung zu gewährleisten.
Es gibt im Wesentlichen vier Methoden zur Bearbeitung des Zahnradhohlraums: Drahterodieren, Funkenerosion (EDM), Galvanoformung und Gießen aus einer Berylliumkupferlegierung. Jede dieser Methoden hat ihre Vor- und Nachteile bei der Bearbeitung von Zahnradhohlräumen. Die Hersteller verwenden in der Regel das Drahtschneiden für geradlinige Evolventen-Zahnräder und bevorzugen das Funkenerodieren für Schrägzahnräder. Außerdem können sie Elektroden, die für das Erodieren von Zahnradkavitäten verwendet werden, mit dem Drahtschneiden bearbeiten. Für schrägverzahnte Elektroden mit kleinem Schrägungswinkel (β≤6°) ist das Drahterodieren nach wie vor geeignet.
2. Bearbeitung des Formrahmens
Der Formrahmen, der auch als Formboden bezeichnet wird, ist ein Hilfsformteil der Zahnradform. Das Verfahren zur Bearbeitung des Formrahmens ähnelt dem von herkömmlichen Kunststoffspritzgussformen. Daher wird in diesem Artikel nicht näher darauf eingegangen. Abbildung 8 zeigt das aktuelle Bild der Bearbeitung des Zahnradformrahmens.