Da es sich um ein Herstellungsverfahren handelt, werden beim Stanzen spezielle Geräte und Werkzeugmaschinen verwendet, um Ausgangsmaterial in einzigartige Formen und Designs zu schneiden, zu formen und zu scheren. Das Stanzverfahren ist vielseitig und lässt sich an verschiedene Materialien anpassen, darunter Metall, Kunststoff, Holz und Verbundstoffe. Es wird auch in verschiedenen Sektoren zum Stanzen von Neopren, Dichtungen, Papier, Verpackungen, zum Stanzen von Stoffen und zur Herstellung von gestanztem Schaum verwendet. Heute stehen zahlreiche Stanzverfahren zur Verfügung, darunter Flachbett-, Rotations- und digitale Stanzverfahren. Unabhängig vom Verfahren müssen jedoch immer spezifische Verarbeitungsgeräte verwendet werden, die den Verarbeitungsanforderungen und dem von Ihnen gewählten Stanzwerkzeugverfahren entsprechen.
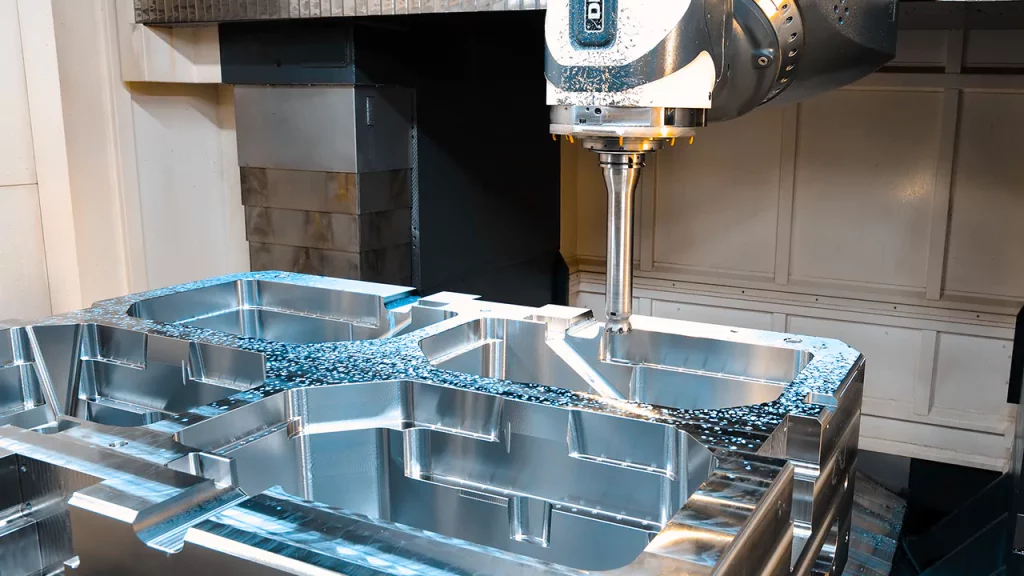
In diesem Leitfaden finden Sie alles, was Sie über den Werkzeugbau wissen müssen, wenn Sie noch keine Erfahrung haben. Lassen Sie uns also ohne Umschweife in die Details eintauchen.
Arten von Werkzeugen für die Bearbeitung von Werkzeugen:
1. CNC-Maschine:
Eine CNC-Maschine steuert präzise das Schneiden, Bohren, Schleifen und andere Bearbeitungsvorgänge eines Metallwerkstücks mit Hilfe spezieller Software und Hardware. CNC-MetallbearbeitungMetallumformung und fräsenund andere Metallbearbeitungen werden auf dieser Anlage durchgeführt.
Arten von CNC-Maschinen:
Anders Arten von CNC-Maschinen können je nach Verwendungszweck und Art des zu bearbeitenden Produkts während des Werkzeugbaus eingesetzt werden. Einige der gängigen Arten und Merkmale von CNC-Maschinen, die häufig während dieses Prozesses verwendet werden, sind:
- Vertikale CNC-Maschine
- Horizontale CNC-Maschine
- CNC-Graviermaschine
- CNC-Fräsmaschine
Je nach der Maschine, die Sie beim Werkzeugbau verwenden, können Sie Hochgeschwindigkeits- oder mehrachsige Bearbeitung Zentren, um das Material mit anderen Werkzeugen weiterzuverarbeiten.
2. Kanonenbohren:
Bohren von Waffen ist eine Tiefbohrtechnik, bei der mit einem langen, dünnen Schneidinstrument Löcher in Metall mit einem hohen Verhältnis von Tiefe zu Durchmesser erzeugt werden. Sie funktioniert gut in Größen von 1 bis 50. Die charakteristische Kopfform eines Tieflochbohrers unterscheidet ihn von einem normalen Spiralbohrer; ein normaler Tieflochbohrer hat eine einzige wirksame Schneide, die Späne abträgt, während sie in ein Metallwerkstück eindringt.
Durch den Einsatz von Hochdruck-Kühlmittel für eine saubere Späneabfuhr auch bei extremen Tiefen im Tieflochbohrverfahren können tiefere Löcher gebohrt werden als mit herkömmlichen Maschinen und Geräten wie Spiralbohrern.
Merkmale und Verwendung von Kanonenbohrern:
- Das Tieflochbohrverfahren wird verwendet, um tiefe, gerade Löcher zu erzeugen. Im Vergleich zum traditionellen Spiralbohren ist dieses Verfahren spezieller.
- Die herkömmliche Geometrie eines Tieflochbohrers weist eine einzige wirksame Schneide auf. Im Gegensatz zum Spiralbohrer schneidet der Tieflochbohrer exzentrisch durch das Metall und steuert sich selbst, sobald er im Bauteil ist. Die Führungsleisten schleifen das Loch weiter, so dass ein präzises, rundes Loch mit gleichbleibender Geradheit entsteht. Das Kühlmittel tritt durch die Kühlmittelbohrung in das Werkzeug ein, und die Späne treten durch das V-förmige Profil am Tieflochbohrer aus.
3. EDM-Maschine:
Elektroerosive BearbeitungEDM ist ein Zerspanungsverfahren, bei dem weniger Material abgetragen wird als bei der herkömmlichen Bearbeitung, das Ergebnis aber genauer und feiner ist. Oberflächengüte.
Beim Funkenerodieren wird Metall von einem Werkstück entfernt, indem ein elektrischer Strom von einer Elektrode zu einer entgegengesetzt geladenen Elektrode geleitet wird, die in das Werkstück implantiert ist. Danach wird das Metall verdampft oder weggeschmolzen.
EDM-Maschinentypen und Verwendung:
Erodiermaschine mit Senkerodiermaschine oder Stößel
Diese Art von Erodiermaschine erzeugt Hohlräume in einem Werkstück, die u. a. für die Herstellung von Werkzeugen und Matrizen, Metallstempeln und verschiedenen Kunststoffformen wichtig sind.
- EDM-Loch-Bohrmaschine
Wie der Name schon sagt, wird das Erodieren von Löchern zur Bearbeitung verwendet. Im Vergleich zu herkömmlichen Bohrverfahren können mit diesem Verfahren jedoch extrem kleine und tiefe Löcher hergestellt werden, die nicht entgratet werden müssen.
- EDM-Maschine für Draht
Eine Drahterodiermaschine funktioniert wie ein Käseschneider oder eine Bandsäge, nur dass sich der Draht und nicht das Werkstück bewegt. Elektrische Hochspannungsentladungen werden über einen Metalldraht (in der Regel Messing oder Kupfer) geleitet, so dass er die gesamte Materialstärke durchschneiden kann. Das Schneiden erfolgt von der Kante her, oder es wird ein Loch in das Werkstück gebohrt, damit der Draht hindurchgeführt werden kann, wenn Teile von innen herausgeschnitten werden müssen.
4. Flachschleifer:
Die Flachschleifmaschine ist die häufigste Form der Schleifmaschine in jeder Werkstatt. Sie ähnelt einem Fräser mit vielen Zähnen, aber die Flachschleifmaschine hat eine Schleifscheibe und ist damit ein abrasives Schneidwerkzeug. Die Schleifscheibe entfernt kleinste Metallteile (sogenannte Späne). Sie arbeitet mit Tausenden von Schneiden an der Scheibe.
Diese Flachschleiftische werden für eine Vielzahl von Aufgaben eingesetzt, unter anderem für die Entfernung von übermäßigem Material. Sie eignen sich hervorragend für harte Materialien (wie Stahl und Diamanten), um eine hochwertige Endoberfläche zu erzielen.
Merkmale und Verwendung von Flachschleifmaschinen:
Sobald der Tisch das Werkstück etwas weiter in die Scheibe gehoben hat, dreht sich das Spannfutter der Flachschleifmaschine hin und her. Mit dieser Maschine können Sie Intervalle einstellen (z. B. 0,001 Zoll / 0,0254 mm) bei jedem Durchgang.
Bei jeder Umdrehung der Schleifscheibe mit ihren Schleifpartikeln werden kleine Teile der Substanz des Objekts abgetragen, um eine glatte Oberfläche zu schaffen.
Daher wird das Flachschleifen in der Regel als Endbearbeitungsschritt eingesetzt, um ein Objekt auf eine bestimmte Toleranz zu bringen. Dennoch folgt häufig eine Poliertechnik während des Schleif- und Läppprozesses.
5. Fräsmaschine:
A Fräsmaschine is equipment that rotates a circular tool with several symmetrically aligned cutting blades along its axis, and the workpiece is often held in a vise or similar device secured to a table that may move in three perpendicular directions.
Milling machines often machine irregular and flat surfaces in solid materials such as metal, plastic, and wood. In contrast to a lathe, where the workpiece rotates during the cutting operation, the cutter is designed to rotate.
Milling machines are powered machine tools used to cut or carve material. Mills employ various cutting instruments, such as revolving blades, drills, and even abrasives.
Milling Machine Characteristics and Usage:
- The greatest mills have high-quality cast iron structures, variable speed engines, power feeds, and cutting tools that move along the x- and y-axes. Milling machines are used in various applications, from woodworking to metallurgy.
- Self-contained electric drive motors, coolant systems, digital readouts, variable spindle speeds, and power-operated table feeds are common features of milling machines. They can also drill, bore, cut gears, and create slots and pockets.
- A milling machine is designed to securely hold material in a vise or otherwise secure to the mill’s bed. The cutting tool commonly moves horizontally or vertically, giving rise to the two basic types of milling machines: horizontal and vertical.
- Vertical mills employ a spinning cutting tool similar to a drilling machine or drill press. The drill chuck is lowered into the workpiece after being positioned on a gantry above the mill’s bed.
- A single-pointed milling cutter is commonly used as a cutting tool. Milling machines have tool heads that spin at speeds ranging from 500 to 50,000 RPM, depending on the model.
- A horizontal milling machine works the same way as a vertical mill, except it has a rotating table instead of a gantry, and its main cutter is usually three or four points. The cutting speed of these mills varies according to specifications, although it can reach 20,000 RPM.
6. Die Spotting Press Machine:
A die-spotting hydraulic press machine is a type of hydraulic press designed to improve mold (die) precision and placement capabilities. It is commonly used for mold assembly, adjustment, inspection, and maintenance, including low-pressure injection molds. It verifies dimensional accuracy by checking the mold’s contact surface and its components.
The hydraulic die spotting press is one of the most dependable and safe machines for inspecting the butt joint of the mold core and cavity. Matching mold elements and verifying mold creation becomes easier and more ergonomic. The basic die spotting press model enables convenient loading, unloading, and customization to meet customer requirements with its spacious table and open height. Metal, plastic, and other synthetic materials can make molds. Different material qualities necessitate various inspection and testing methods.
Die Spotting Press Characteristics and Usage:
- To meet the needs of various industries, the die spotting press can be equipped with an inclined platen, rolling pad, 180-degree rotating platen, automatic clamping and lifting packaging, servo-controlled slider parallelism control system, information request, and other devices.
- Die spotting presses are used for various purposes, the most common of which are mold placing, finishing, and inspection. It plays a key role in the metal forming and plastics industries.
- Due to their versatility, these machines are found in various industries, including household appliances, automobiles, and aerospace.
7. Turning Machine:
A Drehen machine is a machine that molds workpieces into different shapes. A part is rotated while a single-point cutting tool moves parallel to the axis of rotation. The technique can be carried out on the workpiece’s external or internal surface. Most of the time, the beginning material is a workpiece generated by another process. Some portions, however, may necessitate further operations like polishing or platonic solids.
Turning activities are often performed by machining the workpiece. The movement axes can be axisymmetric or curved. A Turned Part or a Machined Component is a component that has undergone turning operations. This method is used to create prototypes and limited runs. It’s also a popular choice for fine-tuning features on parts. Due to its tight tolerances and high surface finishes, a turning machine is popular for precision rotational features.
Turning Machine Characteristics and Usage:
- Turning machines are used for the rough and finished machining of metal workpieces.
- These machines, which can create end surfaces and internal apertures, are widely utilized in various sectors. They can make small and large pieces, prototypes, and tools. This machine can achieve the highest levels of accuracy and precision, making it excellent for adding rotational elements to items. However, many of these machines are prohibitively expensive, making them only appropriate for small and medium-sized organizations.
- A turning machine’s main components are a bed and a spindle.
- A machine’s bed contains all components, including the motor and driving system. The headstock assembly is the machine’s front part, which includes the headstock assembly and the spindle, both of which support the workpiece.
- Depending on the material, the turning machine can conduct various tasks.
—-
For more details and queries about die tooling, contact our professionals at Prototool.