SMED (Single Minute Exchange of Die) ist ein Verfahren zur Minimierung der Umstellungs- oder Einrichtungszeit. Dabei werden alle nicht benötigten Aspekte des Umstellungsprozesses identifiziert und eliminiert. Wenn ein industrielles Gerät ersetzt werden muss, kann die Ausfallzeit kostspielig und unerwartet sein. SMED ist für die schlanke Fertigung von entscheidender Bedeutung, da es Verschwendung beseitigen, die Produktivität steigern und Kosten senken kann.
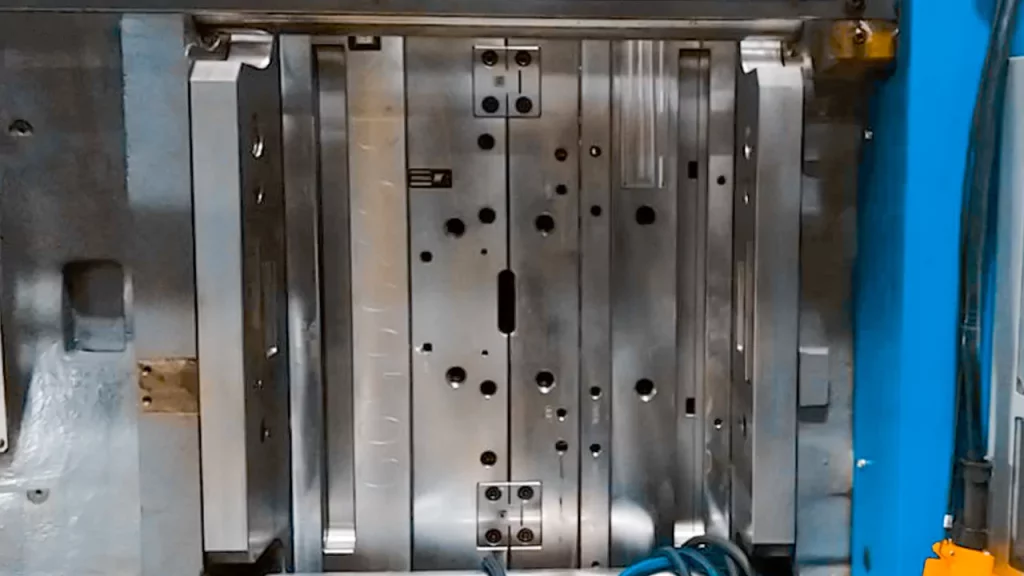
Es steckt jedoch viel mehr dahinter, was diese Strategie ist, was sie bringt und wie sie sich auswirkt, als eine einfache, vollständige Bedeutung, wenn es darum geht, sie zu übernehmen. Schauen wir uns alles im Detail an.
Die Grundlagen des Single-Minute Exchange of Die:
Das SMED-System ist ein Lean-Manufacturing-Prinzip, das mit weniger mehr erreicht und dem Kunden einen maximalen Wert bietet. Sein Ziel ist es, die Zeit zu verkürzen, die für die Umrüstung von Maschinen benötigt wird. Dies ist ein Anreiz für das Werkspersonal, so viele Prozesse wie möglich vor der Umstellung abzuschließen, Teams parallel arbeiten zu lassen und einen standardisierten und optimierten Arbeitsablauf zu haben.
Ziel ist es, die Umrüstzeit von Stunden auf weniger als zehn Minuten zu verkürzen, also den einminütigen Austausch von Werkzeugen. Matrizen sind spezielle Fertigungswerkzeuge, die bei einem Wechsel der Produktionsmodelle neu eingerichtet werden müssen, was zu Ausfallzeiten führt. Shigeo Shigo, ein japanischer Wirtschaftsingenieur, gilt als Erfinder des SMED-Systems. Mit dieser Strategie konnte er die Umrüstzeiten in den von ihm betreuten Unternehmen um 94% reduzieren. Es ist nur manchmal möglich, die Maschinenwechselzeit auf weniger als 10 Minuten zu reduzieren, aber in den meisten Fällen ist dies erreichbar.
Warum ist SMED wichtig?
Die schlanke Produktion zielt darauf ab, Verschwendung zu minimieren und die Effizienz innerhalb eines bestimmten Systems zu steigern, wo immer dies möglich ist.
Nach der Lean-Methode ist die Verschwendung einer der drei Schlüsselbereiche, die angegangen werden müssen: der Verlust von Muda, Muraund Muri. Single Minute Exchange of Dies ist für diese drei Arten von Abfall verantwortlich. Das Hauptproblem ist jedoch die Beseitigung von Mura (Unebenheiten).
Um die Erwartungen der Kunden zu erfüllen, muss jede kleinere Charge verarbeitet werden können, um einen reibungslosen und vorhersehbaren Prozessablauf zu gewährleisten. Die ständige Notwendigkeit, die Ausrüstung zu aktualisieren, ist das Haupthindernis für die Herstellung kleinerer Mengen. Diese Änderungen sind zeitaufwändig und kostspielig und müssen auf praktische Weise wieder hereingeholt werden, um rentabel zu sein.
Da die Umrüstungszeit für einige Maschinen mehrere Stunden oder sogar Tage dauern kann, ist es notwendig, die Produktion bestimmter Maschinen in Bezug auf ihre produktive Zeit zu maximieren. Da die Losgröße maximiert wird, führt dies zu einer möglichst effizienten Nutzung der verfügbaren Ressourcen. Erst wenn der Prozess geändert werden muss, werden Ineffizienzen sichtbar.
Geringere Rüstzeiten bei jeder Umstellung sind eine wesentliche Voraussetzung für die wirtschaftliche Produktion kleinerer Chargen. Daher muss das interne Rüsten so weit wie möglich minimiert werden, damit sich die Umrüstzeit so wenig wie möglich auf den Fertigungsprozess auswirkt.
Seine Bestandteile:
Bei SMED (Single Minute Exchange of Dies) werden Umrüstungen durch eine Reihe von Prozessen vorgenommen, die als Elemente bezeichnet werden. Die Komponenten werden in zwei Typen unterteilt:
- Interne Komponenten
Diese Elemente müssen angewandt oder aktualisiert werden, nachdem das Gerät ausgeschaltet wurde. Beispiele hierfür sind:
- Beseitigung veralteter Werkzeuge.
- Sie zu ersetzen.
- Einstellen des Materialvorschubs.
- Ändern der Programmparameter.
Stellen Sie sich dies wie einen Boxenstopp in der Formel 1 vor. Das Auto fährt in die Boxengasse, hält an und die Crew-Mitglieder wechseln die Reifen.
- Externe Faktoren
Wenn das Gadget in Gebrauch ist, können externe Elemente angewendet oder hinzugefügt werden. Der Kauf neuer Materialzuführungen, die Anschaffung neuer Werkzeuge, die Rückgabe alter Werkzeuge oder die Lagerung alter Werkzeuge, die Dokumentation geeigneter Verfahren oder die Beantragung von Lizenzen sind einige Beispiele. Während sich das Auto noch auf der Rennstrecke befindet, bereitet das Team bereits die Reifen vor, bereitet Werkzeuge vor und positioniert Techniker. So kann die Mannschaft den gesamten Vorgang in Sekundenschnelle abschließen, sobald das Auto zum Stehen kommt.
SMED-Verfahren:
Das SMED-Verfahren (Single Minute Exchange of Dies) besteht aus mehreren Schritten. Sie können diesen LEAN-Ansatz umsetzen, indem Sie:
1. Trennen Sie interne und externe Einrichtungsprozesse.
In diesem Schritt werden die am Umstellungsprozess beteiligten Elemente identifiziert, die bei laufender Produktion mit geringen oder gar keinen Änderungen verwaltet werden können, und dann vor oder nach der Umstellung durchgeführt. Dieses Verfahren führt in der Regel zu einer Verkürzung der Umstellungszeiten um 50%.
Das Team muss sich fragen, ob jedes Element und jeder Teilprozess während des Betriebs der Anlage durchgeführt werden kann. Wenn die Antwort "Ja" lautet, ist das Element extern.
2. Standardisierung der externen Konfigurationsprozesse
In dieser Phase können alle externen Phasen durch Filme oder Flussdiagramme identifiziert und standardisiert werden. Das bedeutet, dass Sie solche Aufgaben bei laufendem Verfahren erledigen können. Wenn dies nicht sorgfältig gemacht wird, kann es vorkommen, dass die Werkzeuge bei stillstehenden Maschinen geholt werden müssen. Dadurch verlängert sich die Umrüstzeit über das notwendige Maß hinaus.
3. Interne Rüstvorgänge in externe Rüstvorgänge umwandeln
In diesem Schritt wird der Umstellungsprozess eingehend untersucht, um so viele interne Elemente wie möglich zu externen zu machen. In diesem Schritt muss das Team überlegen, ob es eine Möglichkeit gibt, interne Elemente in externe umzuwandeln, wie dieser Ansatz aussehen könnte und wie er umzusetzen ist.
Das Ergebnis ist eine Liste von Punkten, die Sie weiterverfolgen können. Diese Prioritätenliste ähnelt in mehrfacher Hinsicht einer Kosten-Nutzen-Analyse.
4. Verbesserung der internen Kommunikationsprozesse
Erst die letzte Umdrehung der Schraube fixiert das Teil an seinem Platz. Shigeo Shingo sagte einmal. Was danach übrig bleibt, ist nur Bewegung, und die kann man wegwerfen.
Das Konzept sieht vor, dass beispielsweise die Schraube durch kürzere, federbelastete Klemmen ersetzt werden kann, die das Teil in Position halten. Die Zeit, die bisher für das Drehen der Schraube aufgewendet wurde, wird nun eingespart. Verschiedene Maschinen oder Werkzeuge werden modifiziert, um Standardgrößen bereitzustellen. Darüber hinaus können Sie auch Befestigungspunkte reduzieren, um die Anzahl der Arbeitsschritte zu verringern.
5. Verbessern Sie die externen Einrichtungsverfahren
Die übrigen externen Elemente werden in diesem Schritt bewertet. Es geht darum, diese Prozesse zu straffen und zu vereinfachen, um Zeit zu sparen.
Wie bei den vorherigen Schritten prüft das Team, wie dieser Teil in kürzerer Zeit durchgeführt werden kann. Wie können wir dies einfacher gestalten? Eine Kosten-Nutzen-Analyse ist ebenfalls nützlich, um zu beurteilen, ob es effizient genug ist.
6. Wiederholen Sie SMED mehrere Male.
Sie können regelmäßig Zeit einsparen, indem Sie den gesamten Prozess immer wieder akribisch analysieren. Neue Technologien oder andere wichtige Erkenntnisse bieten zum Beispiel Chancen, den Prozess per Videoanalyse zu optimieren.
Die Vorteile:
Die folgenden Vorteile werden realisiert, wenn das Konzept des einminütigen Werkzeugwechsels richtig angewendet wird. Von allen Vorteilen bietet der einminütige Matrizenwechsel (Single Minute Exchange of Dies, SMED) vor allem eine höhere Produktivität. Lassen Sie uns nun auf einige weitere Vorteile eingehen:
- Gesteigerte Produktivität: Wenn der Zeitaufwand für Umrüstungen reduziert wird, erhöht sich die Anzahl der in einem vereinbarten Zeitraum produzierten Waren und die Arbeitszeiten steigen. Nicht wertschöpfende "Muda" wird eliminiert.
- Ein flexibler Herstellungsprozess ist denkbar: weil es möglich ist, nur eine bescheidene Menge an Gütern zu produzieren und weil der Wechsel zwischen verschiedenen Arten von Gütern einfach ist.
- Verbesserte Kundenzufriedenheit: Sie führt zu einer höheren Kundenzufriedenheit, weil ihre Bedürfnisse rechtzeitig erfüllt werden.
- Verbesserung der Produktqualität: Dies trägt dazu bei, die Anzahl der beim Einrichten der Maschinen erzeugten fehlerhaften Waren zu verringern.
- Senkung der Kosten für die Instandhaltung der Bestände: Die schlanke Produktion, bei der weniger produziert wird und keine Produkte mehr gelagert werden müssen, senkt die mit der Bestandsverwaltung verbundenen Kosten.
- Senkung der Wartungskosten: Da weniger manuelle Eingriffe, Anpassungen und Stapelungen erforderlich sind, verringert sich das Risiko, dass Stanzformen herunterfallen, anschlagen oder physisch beschädigt werden.
- Weniger Unfälle am Arbeitsplatz: Die Zahl der Arbeitsunfälle während dieses Prozesses ist aufgrund des einfacheren und kürzeren Vorbereitungsprozesses zurückgegangen.
Schlussfolgerung:
Das Ziel der digitalen schlanken Fertigung ist die Beseitigung von Verschwendung. Die Hersteller ergreifen Initiativen zur Verbesserung der Materialabläufe nach dem Auswechseln, um noch schnellere Anlaufzeiten zu erreichen, indem sie SMED (Single Minute Exchange of Dies) einsetzen. Eine intelligente, vernetzte Fertigungslinie gibt den Unternehmen noch mehr Informationen über den Betrieb und die Effizienz ihrer Produkte.