Individual plastic parts are produced and processed using the manufacturing process known as Spritzgießen. Injection molding creates molded items by injecting molten plastic materials into a mold, cooling, and solidifying them. The technique is helpful for bulk manufacturing items with intricate shapes and is crucial to processing plastic. The injection molding process necessitates a substantial initial outlay. Despite the initial expenditure, this manufacturing method is still popular due to the declining cost of individual parts. Production is more affordable because of this cost structure than it would be using conventional manufacturing methods. (We’ll going to explain the origin of the ISO injection molding standard)
ISO Standards are followed through the manufacturing process to maintain uniformity in the numerous individual parts. To assist businesses in establishing levels of homogeneity in management, provision of services, and Produktentwicklung in the industry, ISO Standards were established as the worldwide standard rules. The International Organization for Standardization was established for thorough standardization in the various sectors. Its founding dates back to 1946 when two organizations—the International Federation of National Standardizing Associations (ISA) und die United Nations Standards Coordinating Committee (UNSCC)—had previously existed and whose goal was the regulation and establishment of standards for manufacturing—joined forces.
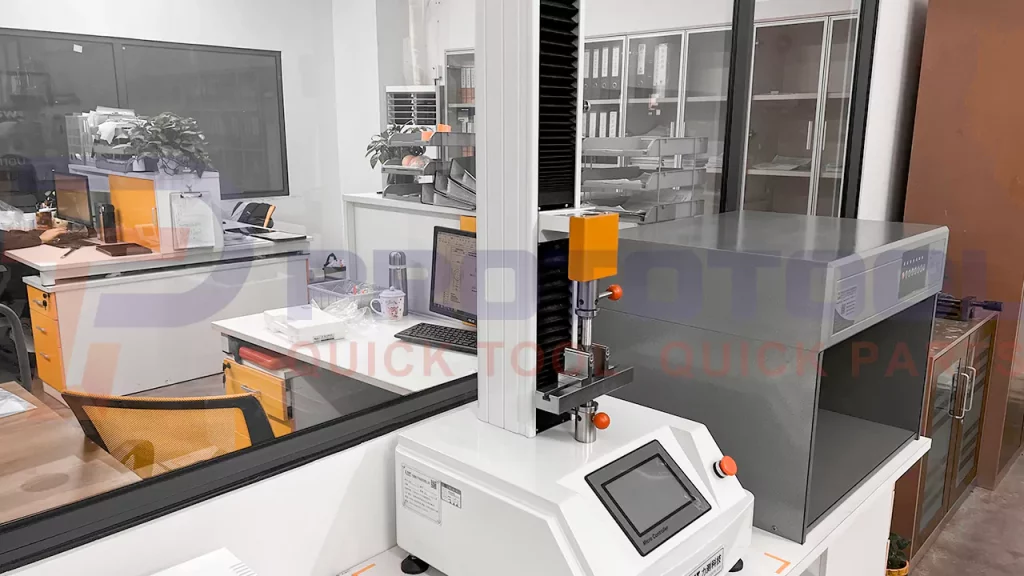
More than 23.000 standards have been developed since that time up to the present. These standards have been set for various sectors, out of which the manufacturing and technology sectors are primarily critical. For example, the Standards are crucial for manufacturing and ensuring homogeneity among millions of processed parts.
Why is there a need for ISO Injection Molding Standards?
The manufacturing process of injection molding involves producing numerous individual parts at a large scale. When there is a large quantity of the same products being manufactured, there needs to be a standard uniformity in the designs. However, errors are inevitable. Minor mistakes can lead to considerable losses in both raw materials and the financial aspect. The ISO Injection Molding Standards are established to reduce these little mistakes leading to huge losses. Some reasons that emphasize the importance of the ISO Injection Molding Standards are listed below.
Reasons Why ISO Injection Molding Standards Aare Important
1. Due to the need for design, testing, and tooling, upfront expenditures are frequently very high. These initial expenditures, however, help establish the minimum cost structure at later stages. The factories must get the design right to produce large parts. Getting the design right the first time will result in the maximum utilization of the upfront expenditure.
2. The ISO Injection Molding Standards are essential for businesses because these quality measures help minimize the waste of raw materials in production. Since most tools are constructed of aluminum or steel, a highly hard material, modifications at a later stage might be challenging. For example, the business might wish to remove steel or aluminum to expand the tool cavity and add plastic to the item. Another example includes the reduction of plastic materials. The tool cavity must be smaller to remove plastic by adding aluminum or metal. The process is incredibly challenging and, in many instances, might need altogether scrapping the tool and starting anew. Hence, the ISO Injection Molding Standards are essential in the organization of a design plan from the beginning of the manufacturing process. This will help in minimizing later changes.
3. Preventing flaws throughout production is the foremost consideration while creating the mold tool. Therefore, businesses should keep injection molding in mind from the outset regarding part design. Early geometrical simplification and part reduction will be beneficial in the long run. However, the design’s simplification is impossible after a certain point in time. The ISO Injection Molding Standards are crucial in maintaining both designs while not compromising and minimizing flaws.
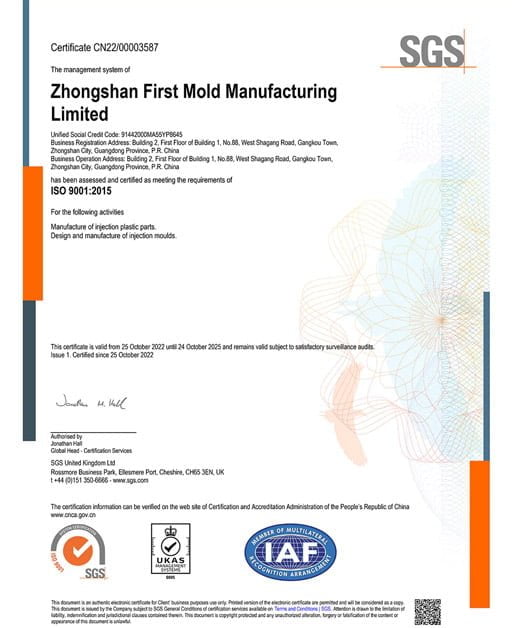
ISO Injection Molding Quality Standards
ISO Injection Molding Quality Standards are essential to facilitate an efficient manufacturing process of the bulk quantities of individual parts, primarily made from plastic. Furthermore, these quality standards are crucial in the overall quality of the product developed. One of the most essential ISO Injection Molding standards is ISO 13485.
This is the quality standard laid for the manufacturing process in medical industries. Design qualification (DQ), operational qualification (OQ), and performance qualification are included in this (PQ). By adopting ISO 13485, manufacturers follow a strict dedication to the security and caliber of medical devices during the manufacturing process and lay a solid foundation on which to address the EU Medical Device Directive (MDD), the EU Medical Device Regulation (MDR), and various other medical laws.
The latest version of the accepted ISO Injection Molding Standard ISO 13485 is the 2016 version. The ISO Injection Molding Standard ISO 13485 2016 version of the quality standard outlines some requirements for the quality management systems required for manufacturing medical products and related services that satisfy customers and adhere to legal standards. ISO 13485:2016 quality standard applies to all medical equipment manufacturing factories regardless of size. These requirements are of two kinds which are general requirements and documentation requirements. These requirements are listed below.
Requirements
General Requirements- These broad specifications are some formal specifications that act as the impetus for creating and implementing a quality management system. Respecting rules, documenting necessary information, and deploying suitable systems with defined protocols are among these requirements. The risk assessment introduces additional methods to lower the risks detected and try to prevent catastrophic events. It also determines the processes that must be followed to make your medical device and adhering to them, which are additional requirements. Finally, the businesses should establish methods for tracking the actions, address any errors or omissions in the process, and produce documents to demonstrate that all the activities are being carried out.
Documentation requirements- The documentation requirements are specific requirements that must be followed through the manufacturing process under the ISO Injection Molding Standards. Both the procedures and the records must adhere to the standard’s highly stringent standards, which are as follows:
- A file containing information on the specifics of the product and instructions for intended use should be included with every new medical equipment.
- Make a plan to manage documents.
- Make a plan for maintaining records.
Another ISO Injection Molding Standard applied to the manufacturing process is ISO 294. The standard has been revised over and over to include newer and latest features in the part design and production.
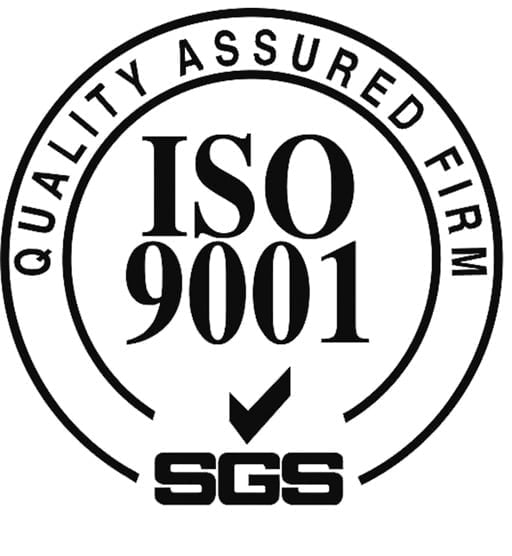
Other alternatives to maintain the quality of the manufactured products
In addition to the ISO Injection Molding Standard, alternative practices are used to standardize injection modeling processes. Quality control can be exercised through several methods. Some of these alternative practices are listed below.
Scientific Molding: Scientific molding refers to a benchmark process for developing, optimizing, and documenting the ideal setup process for each injection molding project so that the same procedures and variables are followed for each run. This process helps ensure homogeneity in the manufacturing of the individual parts along with the ISO Injection Molding standards.
Production Part Approval Process (PPAP): This Production Part Approval Process is a quality standardization process primarily used in the automobile industry. This method assures repeated consistency in the quality of the automobile parts. A PPAP inspection has 18 components that range from customer approval to sample part production.
First Article Inspection: Along with the ISO Injection Molding Standard, the First Article Inspection procedure is also used to ensure the quality of the manufacturing process. It ensures that the manufacturing process successfully produces the parts with the exact specifications. When it comes to injection molding process FAIs, the manufacturing process takes a quality-first approach. Customers use GD&T to highlight the most critical dimensions of their part.
How to choose whether the Injection Molding processes are a right fit for the manufacturing process of the industries?
Different factors must be considered to see whether the injection molding process is the right fit for a manufacturing project. The budget of the manufacturing project is the primary factor that needs to be considered before choosing the injection molding manufacturing process for the business. Before narrowing down the budget, determine the number of parts made at which injection molding becomes the most cost-effective manufacturing method.
The number of parts produced should be determined to have the actual investment value considering the costs of design, testing, production, assembly, marketing, and distribution, as well as the expected price point for sales. The prices should be finally determined to make a conservative profit margin.
Another factor you should consider is the design of the parts. The cycle time is critical in this case. There is a need to reduce the cycle time as much as possible to maximize the efficiency of the manufacturing process. Using machines with hot runner technology, as well as well-thought-out tooling, will help. Small changes can even make a big difference, and shaving a few seconds off your cycle time can add significant savings when producing millions of parts. All of these factors help in deciding whether the Injection Molding processes are the right manufacturing process for the industries.
Bottom line
The procedure is popular not only because it saves money but also because there is little material waste. Compared to traditional methods like CNC manufacture, which remove a sizeable percentage of the original plastic block or sheet, less material is wasted during the entire process. As a result, several sectors have switched from using traditional manufacturing procedures to injection molding. The manufacturing process of choice for industries including the automobile, consumer goods, and medical device industries is injection molding.
This manufacturing process needs to be carried out keeping some standards in mind. There are ISO Injection Molding Standards that are officially accepted for manufacturing processes.