Flash is one of the most often occurring defects in injection molding. The thin layer of plastic forms when two different mold surfaces meet to create a boundary. There may be a difference in growth and other characteristics at these locations, which may enhance the risk of a flash. Managing flash from injection molding is a simple procedure, but it needs additional resources and reduces the overall efficiency of the process. In addition, Injection molding flash removal, which is the process of eliminating flash manually or mechanically, may have a detrimental effect on the product’s quality and may cause damage to the mold, which may result in additional costs and other losses. Projects using injection molding must focus heavily on eliminating flash defects to the fullest degree.
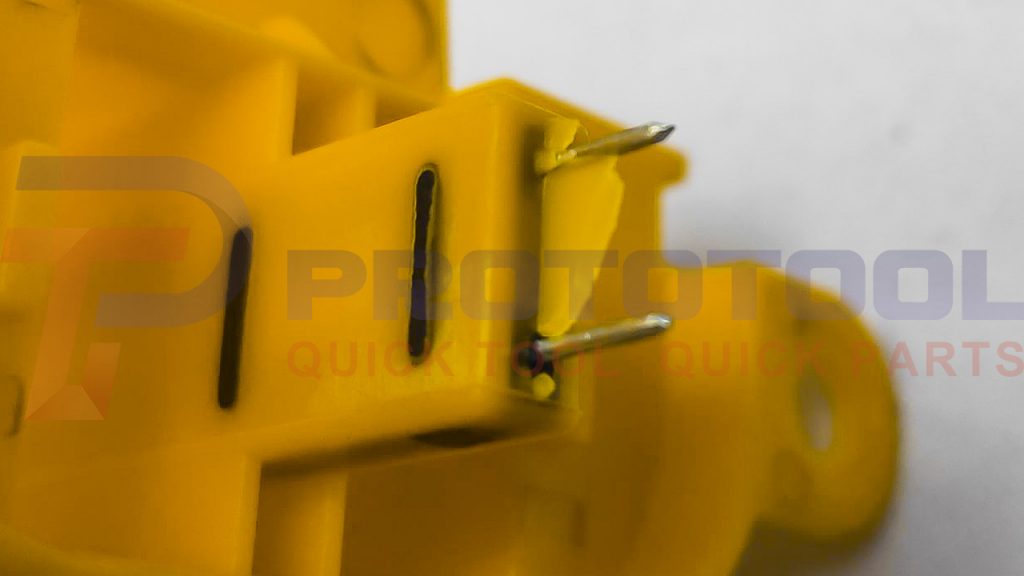
In order to minimize injection molding flash, it is first essential to identify the issue’s origins and then address those causes efficiently by adopting a targeted strategy. In this essential guide, we will be looking at the causes and prevention of flash injection molding.
Content
I. What Is Injection Molding Flash?
II. What causes flash in injection molding?
III. How to avoid flash in injection molding?
IV. Conclusion
What Is Injection Molding Flash?
You must be wondering what a flash is in injection molding. Well, you have turned to the right page.
The defect known as injection molding flash happens when a component has excess plastic on the parting line, a mold’s edge, or at any other spot where different shapes and regions meet. Flashing is often the most common occurrence on the separating line of plastic molding. Nonetheless, the influence extends to other regions of the area. It does not matter where they are since the causes and effects are always the same.
Most manufacturers in the industry significantly reduce the amount of flash present in molded components but do not eliminate it. The key consideration is the entire injection molding process cost. There is a substantial price premium associated with flash-free molds, yet, most businesses can achieve a balance between price, quality, and aesthetics.
Even though a certain amount of flash is thought to be a normal component of the molding process, excessive flash may damage the surface quality of parts and interfere with their seating, mating, or assembly. It is due to the fact that flash is a byproduct of the molding process.
What causes flash in injection molding?
This section will review some of the major reasons that cause injection molding flash.
· Mismatching of Parting Line
Environmental pollutants like dust and dirt, which may keep the mold open, are one of the primary causes of parting line mismatch. This causes extra material to escape, leading to a flash defect. In addition, defects in the mold may be the cause of this problem. As a result of continued usage, these problems often become more prevalent.
Flashing due to a mismatch in the separating line might be caused by leaks caused by aging or worn-out equipment. Even if you have the right mold and have tested for impurities, flashing may still occur if the clamping pressure is not properly regulated or the forms are very complex. Cavities and other intricate characteristics may increase the total pressure to which your mold is subjected, resulting in leaks and defects in some regions.
· Improper Venting During the Process
Injection molding is a complex process that requires attention to a variety of factors, including temperature, pressure, air pockets, and other characteristics. The existence of trapped air bubbles, for instance, is a crucial fault in any injection molding design, as they might impact the component’s mechanical performance and load-bearing capability. Similarly, the injection-molded components have a temperature range that permits optimum formation. Vents are essential to ensure that these components continue to operate correctly. Any problems would result in a multitude of flaws, and flashing is one of them.
· Low Clamping Pressure
A flash can occur during the packing and storage processes. During the packing process, the material shrinkage that occurs during the cooling process is taken into consideration. The easiest method is to inject more than necessary while the holding process maintains pressure balance across the whole system until it can be cooled.
In both instances, the clamping pressure must be defined accurately. Inappropriate clamping force may disrupt the separating line, allowing incoming liquid to escape and causing flashing.
· Sprue Bushing Issue
Sprue bushings are a crucial component of mold since they direct the flow of molten plastic into the mold chamber. Over time, they may lose the necessary support to withstand the force of the injection pressure, resulting in a decline in their functionality. In these instances, the injection-molded components you purchase will include flaws, with flashing being the most typical.
· Viscosity
Aside from the process stage, a few other variables might induce injection molding flash depending on the process and flow characteristics. The ability of a liquid to flow is known as its viscosity, and this quality is crucial to the injection molding process. If the viscosity of the molten liquid is low, it will readily flow out of the mold and exhibit faults in the form of a flash.
· The temperature of the Barrel and Nozzel
In addition to pressure, other factors contribute to the rise in viscosity and, thus, the increase in a flash in your injection-molded product. Both the barrel and nozzle temperatures also impact it. Due to the decreased viscosity caused by an increase in temperature, the fluid is more likely to leak, increasing the likelihood of injection molding flash.
· Over-Fill or Metering
Any injection molding configuration will be subject to restrictions, which will be determined by size and shape. If excessive molten plastic is in the mold, the injection pressure will inevitably exceed the clamping pressure, resulting in leaks. As a consequence, the likelihood of flash and other defaults increases. However, care must be taken while modifying the feed parameters since plastic shrinks as it cools, and you do not want the injection molding process to result in a short shot that leaves the product unfinished.
· High Pressure
Pressure present during a procedure is one of the major factors that may contribute to an increased risk of flash. As a matter of fundamental physics, increased pressure in a limited space will increase both temperature and flow characteristics. The increased pressure and subsequent rise in viscosity may lead to a number of undesirable outcomes, including flash. One of these defaults is attributable to the flash.
· Over-Packing
Injection-molded items may be susceptible to flash because of design challenges and powerful route features in the mold. Even a small quantity of solidified molten liquid may impede material flow in confined spaces. As a result, intense pressure develops inside the mold. The resulting issues are not limited to the flash itself. However, you will have to deal with a number of additional challenges, such as warpage, non-uniform density, and a number of other associated concerns.
How to avoid flash in injection molding?
This section will highlight the solutions to avoid injection molding flash.
· DFM
DFM, or design for manufacture, is essential for both the avoidance and reduction of flash. For instance, plastic injection molding rules advocate positioning the parting line along the component’s edge rather than on a flat surface. This is done to enhance the aesthetic and functionality of the object. This makes seam concealment easier and minimizes the likelihood of flash. DFM analysis is becoming a fundamental part of industrial injection molding projects. In injection molding, specialized software tools can simulate the results, depict the flow characteristics, and predict common difficulties like warpage, flash, and heat flux. These gadgets are now available for use.
· Slowing Down The Injection rate
Controlling process variables is an effective method for minimizing the amount of flash produced by injection moulding. The injection rate has a direct influence on the viscosity, pressure, and temperature of the mixture, all of which have the potential to generate a flash. Given that most of the process’s variables are tied to the injection rate, this is often the first step used by seasoned professionals when addressing flash.
· Specifying A Flash-Free Mold
Using a flash-free mold is an effective, if expensive, method for totally eliminating flash from injection-molded products. It provides the greatest outcomes, but its high price makes it inappropriate for many applications and organizations.
- Mould Cleaning
The collection of dirt, debris, and other impurities in the mold is a primary reason for a mismatch in the separating line. In addition, microparticles in tiny mold cavities may induce overpacking, hence aggravating the component’s overall flaws. Maintaining a clean and well-maintained mold may help reduce the likelihood of these problems occurring and provide the greatest outcomes.
· Maintenance and Process Improvement
Maintenance of the mold and enhancement of the process is vital to achieving consistent and reliable outcomes. Tonnage and pressure imposed by the clamp may sometimes generate mold damage, resulting in particular deformations that may lead to many component defects.
Tips: Other Injection Molding Defects
Conclusion
We hope this guide gives you a better understanding of injection molding flash and how to deal with it. If investing in flash-free tooling is out of the question, or if you’re already working with a mold, you can achieve the desired results by refining your part design, arranging for mold cleaning or maintenance, consulting with your injection molder about potential process improvements, or switching to a different piece of machinery.