トップCNC加工工場はCNC加工の欠陥をどのように処理するか
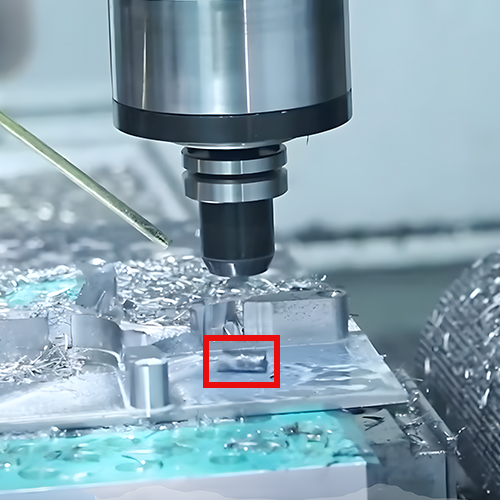
この記事では、トップクラスのサプライヤーがCNC加工の欠陥にどのように取り組んでいるかを紹介し、高品質の部品が課題を克服する方法を明らかにします。
大型ダイカスト金型の割れ要因分析
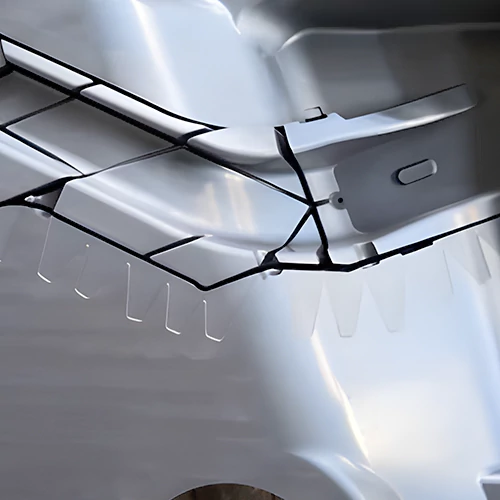
経験豊富なダイカストサプライヤーが、ダイカスト金型割れの原因を分析し、お客様の製品をより完璧なものにします。
一般的なダイカストの欠陥:原因と解決策の概要
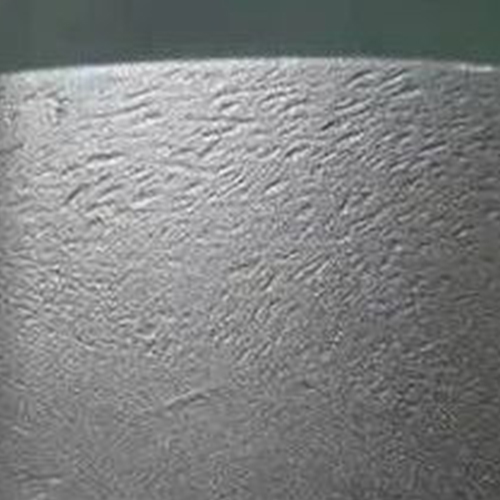
一般的なダイカスト鋳造の欠陥、その原因、および解決策を簡単に理解できます。専門家の洞察でダイカスト品質を向上させましょう。
射出成形における反りの原因と解決策
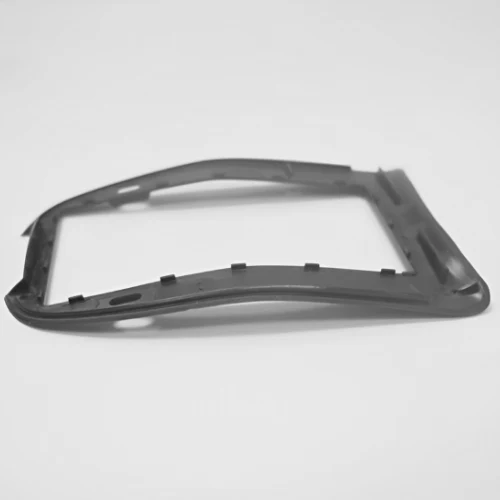
射出成形機の宿敵、反り!特に微調整の工程では、よくある問題です。キャビティと一致するはずの部品がズレてしまい、反った部分ができてしまったとします。このシナリオでは、専門家でなくても曲がりやねじれを見つけることができます。では、このような場合、どうすればいいのでしょうか?単純なことですが、プラスチック製品にそりが発生するのを防ぐために、意図しない曲げを避けることです。しかし、それでも同じ問題が発生した場合、射出成形品全体の品質に影響を与えないよう、反りの原因、種類、解決策を特定することが重要です。本日は、詳細なアプローチ [...] をご紹介します。
射出成形における真空ボイド:最も一般的な射出成形の欠陥を解明する
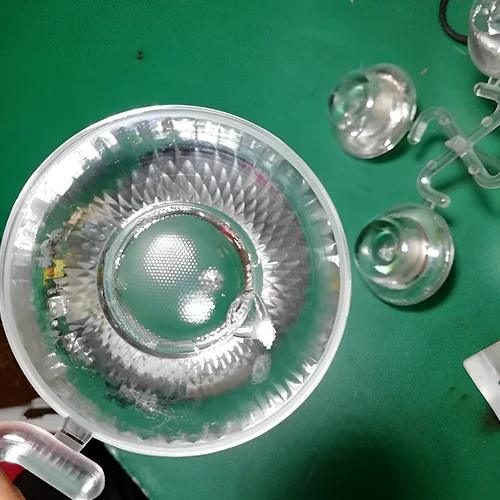
プラスチック射出成形サービスのおかげで、プラスチック製造業の生産性は向上したが、その完成品は必ずしも顧客の期待に応えていない。射出成形プロセスの管理効率の欠如から、操作ミス、生産ミスなど、この生産アプローチのさまざまな側面が、一般的な射出成形の欠陥につながる可能性があります。気泡や真空ボイドは、見過ごされがちな射出成形の欠陥のひとつです。些細なことに見えるかもしれませんが、射出成形で真空ボイドに直面すると、製品が非効率で低品質になる可能性があります。もしあなたがこの問題を警戒し、生産品質や一貫性に影響を与えたくないのであれば、 [...]...
射出成形におけるジェッティング - 原因の特定と欠陥のトラブルシューティング
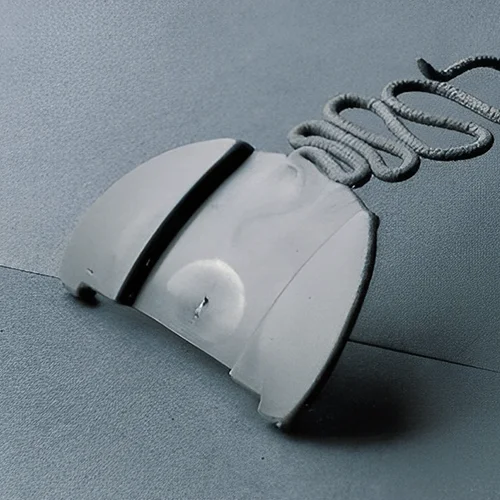
溶融した材料が金型キャビティに注入され、キャビティを満たす前に固化し始めると、成形部品にジェッティングが発生する。この早期凝固によって生じる歪みの一種です。さらに、ジェッティングは最終的な成形品の表面に、通常は最初の射出ゲートから続く四角い線として目に見えることがよくあります。射出成形品に噴流欠陥があると、欠陥の流動パターンのために自動的に弱くなります。この一般的なプラスチック射出成形の欠陥を特定し、時間内に解決する方法をお探しなら、このガイドで欠陥、その特定、トラブルシューティング方法について説明します。それでは、引き続き [...] をご覧ください。
射出成形部品に変色?それをフィットさせる方法がここにあります!
射出成形による変色は、プラスチックの地色からの変化である。過熱、汚染、製造上の欠陥など、すべてがこの欠陥部品の原因となる可能性があります。熱劣化による部品の着色の欠陥が明らかになる程度は、劣化の程度によって異なります。この問題を回避するためには、プラスチック射出成形工程で射出成形品の変色につながる要因をしっかりと把握することが重要です。変色した製品の一例を以下に示す。それでは、射出成形品の変色の分析、影響、解決策についてさらに深く掘り下げてみましょう。こちらもお読みください:CNC [...] が直面する6つの共通課題
射出成形におけるフローラインの欠陥:一般的な射出成形不良の解決と予防
その精密さゆえに、射出成形のプロセスを通していくつかの問題が発生する可能性があります。オペレーターのミスから金型設計の欠陥に至るまで、部品の外観や構造の完全性が損なわれる可能性がある。この工程で製造業者がよく直面するエラーのひとつに、射出成形におけるフローラインの欠陥があります。もしあなたが、生産工程でフローラインの問題にしばしば直面するプロの製造者なら、この問題を解決したり、生産される部品の品質や見通しに影響を与えないようにする方法を学ぶ時です。この記事では、射出成形におけるフローラインの不具合について、その全貌をご紹介します。こちらもお読みください:原因は何か
射出成形ウェルド・ラインの発生とその解決策の分析
射出成形のウエルドラインとは、射出成形された部品にできる線のことで、2つの金型が合わさる部分にできます。その結果、その部分にはかすかな、おそらく検出できない線ができます。 この線は通常、成形品の全体的な形状や寸法には影響しません。しかし、金型の磨き方、材料の種類、材料の色、加工の設定によって、さまざまな程度で見られることがあります。成形品にこの線を目立たなくする方法は数多くありますが、射出成形は2分割金型に頼るため、完全に避けることはできません。このガイドでは、[...]の原因、差別化要因、影響、解決策を探ります。
射出成形におけるバーンマークの深い分析
「バーンマーク」とは、射出成形部品の欠陥の一種で、キャビティ充填工程の最終段階付近で黒ずんだエッジとして現れます。射出成形金型のキャビティ内に閉じ込められた空気が、バーンマークを引き起こす。プラスチックが金型に送り込まれると、キャビティ内の空気が圧縮され、ディーゼル燃料が発火した。溶融プラスチックの前縁が黒く焦げたのがその原因である。プラスチック部品や射出成形用金型の設計上の欠陥により、成形サイクルの射出(または充填)段階で空気が閉じ込められた場合、火傷の痕が残ることがある。その結果 [...]...