Machining services are crucial in manufacturing, as they shape and transform raw materials into finished products. Various machining services are available, each with its unique set of benefits and applications. From milling to drilling and turning, machining methods have revolutionized how products are made. This article will explore the most common types of machining methods, their advantages, and the industries that use them. Understanding these services will help businesses determine the best machining processes for their manufacturing needs.
This article will discuss different machining services and how they are conducted in the plastic injection molding/manufacturing industry.
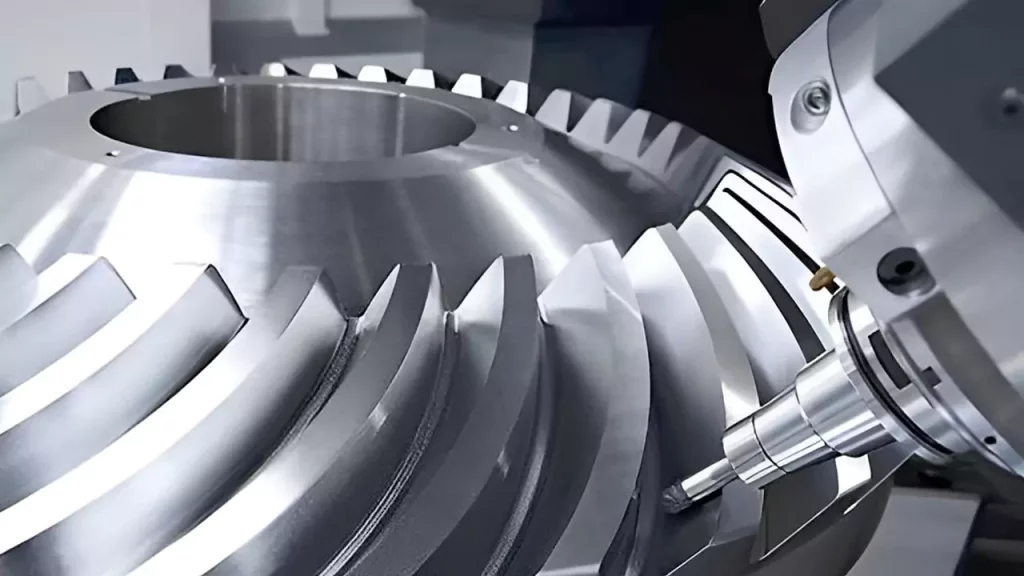
Common Machining Services:
Maquinação de precisão
Precision machining can be defined as any machining technique that requires unusually narrow cutting tolerances (as a matter of thumb, between 0.013 mm and 0.0005 mm) or surface finishes finer than 32T.
Precision machining, like CNC machining, can be applied to various manufacturing methods and tools.
The exactness of a precision tool’s cut can be influenced by factors such as stiffness, damping, and geometric correctness.
Precision machining applications also require motion control and the machine’s ability to respond at high feed rates.
CNC Manufacturing
CNC machining (computer numerical control machining) is a computer-aided process that can be used in conjunction with a wide range of equipment.
When directing a machining tool in shaping the workpiece according to predefined specifications, software and programming are often required in the G-code language.
CNC machining, instead of manually guided processes, is automated.
Some of its advantages are as follows:
- Faster production cycles: Once the Máquina CNC is properly coded, it usually requires less maintenance or downtime, allowing for a faster output rate.
- Uniform production: CNC machining services are often precise and produce items with high design consistency.
- Low manufacturing costs: CNC machining can be cost-effective, especially for high-volume production runs, due to its rapid turnover speed and low human labor needs.
Different Machining Processes:
Various machining processes are available, each of which is tailored to meet the specific demands placed on a given set of raw materials, finished workpieces, and end products. The terms “cars,” “tongs,” “washing,” “planning,” and “grinding” is commonly associated with the more conventional machining services. In terms of mechanical processing, new techniques like electroplating, wire cutting, casting, forging, and powder processing have emerged alongside the progression of mechanical technology. It includes:
Turning:
The turning process is primarily characterized by the rotation of the workpiece, while the turning tool is responsible for sculpting the workpiece into the desired form.
It is possible to acquire the cylinder’s inner and outer cylindrical surfaces if the tool is moved along the axis of rotation that is parallel to it.
The process of moving the tool in a diagonal direction along the axis of the junction results in the construction of the cone.
Lathes, known as profile lathes or CNC lathes, are responsible for producing a rotating surface. These lathes manage the feed of the tool along a curve.
Utilizing formed turning tools with lateral feeding is another method for creating spinning surfaces.
Turning also allows for machining threaded faces, end planes, and eccentric shafts, among other things.
Grinding:
Grinding is a type of processing that relies mostly on abrasives and grinding wheels to process the workpiece. This processing method also depends on the rotation of the grinding wheel.
The abrasive particles on the grinding wheel are primarily responsible for the cutting, engraving, and sliding action that occurs on the surface of the workpiece when the grinding wheel is in motion.
Because the abrasive grain becomes less sharp with time, the cutting motion becomes less effective, and the effort required to cut becomes greater.
Consequently, the grinding wheel needs to have diamond-turning tools applied to it after it has been used for a predetermined amount of time.
Milling:
Milling is a process that mostly depends on the tool’s rotation.
This process may be broken down into two categories: horizontal milling and end milling. The cutting edge located on the milling cutter’s outer circular surface creates the horizontal milling plane.
End milling is produced by the face edge of the milling cutter during its operation.
It is possible to raise the speed of the milling cutter to attain high cutting speeds and boost overall productivity.
Nevertheless, because of the cutting in and out of the milling cutter teeth, the impact is created, and the cutting process is simple to produce vibration; this makes it difficult to increase the surface quality of the material.
Machining of Complex Surfaces:
A CNC machine is an invaluable tool when it comes to the machining of complex surfaces.
For the most part, profile milling, CNC milling, and other specialized processing techniques are utilized in cutting three-dimensional surfaces.
When milling a profile, a prototype serves as a necessary support mold.
The ball profile head is machined, and while it is being done, a specific amount of pressure is always applied to the prototype’s surface.
Inductance is used to convert the movement of the profiling head, while the processing amplification controls the three axes’ movement of the milling machine. This forms a trajectory for the cutter head to move along the curved surface and create its profile.
Ball nose milling cutters with the same radius as the contoured head are the most common type of cutter used in milling cutters.
The development of computer numerical control (CNC) technology has created a more effective surface machining method.
Special Processing:
Special processing is different from the traditional cutting machining method. It can use physical (electrical, sound, light, thermal, and magnetic), chemical, or electrochemical methods to process the material of the workpiece so that the workpiece can be shaped into the desired form.
Types of Machining Technologies:
Erosion Machining Technologies:
There are two types of erosion machining technologies:
- Electric discharge machining (EDM): Also known as spark machining, this process employs electric arcing discharges to create micro-craters that result in full cuts in a short time. EDM is utilized in applications that call for complicated geometrical shapes in hard materials with tight tolerances. EDM requires an electrically conductive base material, which limits its application to ferrous alloys.
- Water jet cutting: A high-pressure stream of water cuts through the material in this operation. The abrasive powder can be added to the water stream to facilitate erosion. Water jet cutting is most commonly employed on materials that can be damaged or deformed by a heat-affected zone.
Burning Machining Technologies:
Welding and burning machine tools both use heat to shape a workpiece. The following are the most frequent types of welding and burning machining technologies:
- Laser cutting: A laser machine produces a narrow, high-energy light beam that melts, vaporizes, or burns material. The most prevalent types of lasers used in machining are CO2 and Nd: YAG lasers. The laser cutting procedure is ideal for shaping steel or etching patterns into material. High-quality surface finishes and exceptional cutting precision are among their advantages.
- Plasma cutting: Plasma torches generate an electrical arc, converting inert gas into plasma. This plasma reaches extremely high temperatures and is rapidly applied to the workpiece to melt away undesirable material. The method is frequently used on electrically conductive metals that require a precise cut width and little prep time.
- Oxy-fuel cutting: Also known as gas cutting. This machining service and technology melts and cuts away material using a mixture of fuel and oxygen. Because of their great flammability, acetylene, gasoline, hydrogen, and propane are widely used as gas media. The advantages of this technology are its portability, limited reliance on basic power sources, and the capacity to cut thick or hard materials such as robust steel grades.
Conclusão:
Are you looking for a professional consultation to evaluate which type of machining services, processes, and technology is ideal for your production demands? Feel free to contact our experts at Prototool!