The importance of an máquina de moldagem por injeção cannot be overstated in the manufacturing industry, particularly in producing plastic parts and products. From efficiency to productivity, versatility, precision, consistency, cost-effectiveness, and much more – manufacturing with injection molding machines is common today for endless benefits. However, these benefits can only be availed if you know how an injection molding machine works, especially when operating its different components. Now if you’re starting you indulge in the injection molding manufacturing industry, it’s time you dive deeper into exploring its different components and how they work. Today we will cover everything you need to know about an injection unit.
What is an Injection Unit?
A moldagem por injeção de plástico machine’s injecting unit is a unit that pushes an injection plunger or a screw forward inside a cylinder to inject molten plastic into the mold. The clamping force is typically used to represent the size of an injection molding machine.
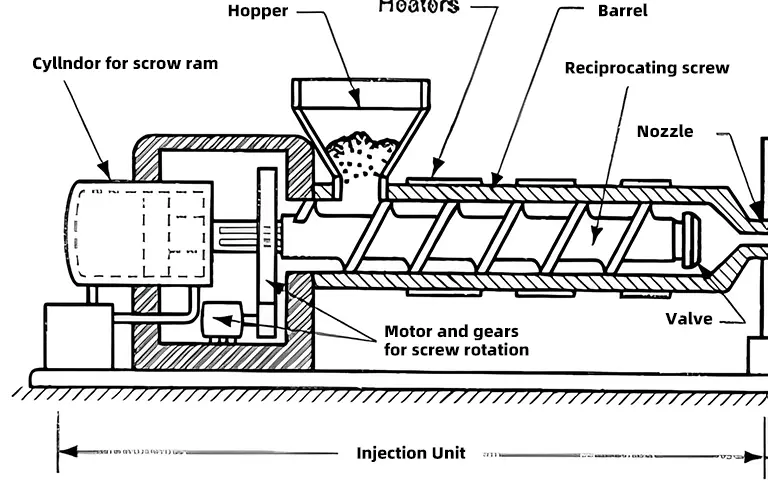
The injection unit’s functions are to melt plastic using heat and inject molten plastic into a mold. The screw is turned to melt plastic introduced from the hopper and to collect molten plastic in front of the screw (a process known as metering).
Functions of an Injection Unit:
The following are the fundamental roles that a machine’s injection unit plays:
- Melting the polymeric resin and preparing it
- Pressurizing and feeding the molten resin into the mold while controlling the circumstances.
Two separate system designs, the plunger, and the reciprocating screw designs, are typically utilized as the foundation for an injection unit. This latter method is the one that is utilized the vast majority of the time on contemporary molding machines. A standard reciprocating screw injection device.
Working:
The rotation of the screw that is caused by the screw drive motor causes solid granules of resin to be pulled into the flights of the screw. The wall of the barrel acts as a source of heat for the resin, and the friction created due to the shearing action of the screw also contributes heat. Because of the design of the screw, the flight volume decreases as it moves near the front of the barrel, which results in the softening resin being compressed into a molten phase.
The term “plasticizing” is frequently used to refer to this process. After that, the pressurized molten resin is metered into the cavity between the screw tip and the nozzle using a ring valve, sometimes known as a “collar.” It is common practice to refer to resin accumulation before the screw tip as the shot or the screw cushion.
Because the screw cushion expands as the screw turns, the screw must go back up the barrel until the desired cushion size is obtained. When this is acquired, the screw rotation will be put to a halt. At this point, the injection unit is considered primed and prepared for the subsequent operation, referred to as the injection phase.
The screw must be forced forward, which results in the ring valve being closed so that the molten resin may be injected into the mold through the nozzle. The pressure on the screw cushion is increased due to the ring valve being securely closed and placed against the screw shoulder.
Relacionadas: Princípios de seleção e criação de uma base de moldes eficaz
As the cushion pressure builds up, it eventually reaches an adequate point to force molten resin through the nozzle and into the mold feed system. The pressure exerted will continue until the impression left by the mold is entirely filled with molten resin. This particular chain of occurrences is called the “first stage” of the injection process or the high-pressure phase.
If the injection first stage is permitted to proceed until the point at which the mold is completely filled, overpacking of the moulding will be the consequence. Because of the high amounts of moulded-in stress caused by overpacking, components with overpacked mouldings have poor dimensional stability and unpredictable mechanical characteristics.
After the first step of injection has been completed, the pressure being applied is lowered to an adequate level to prevent the component from being overpacked. On the other hand, excessively lowering the pressure could lead to components being under packed, leading to high levels of component after-shrinking and distortion.
It is maintained until sufficient solidification of the feed system is sufficient to allow for the complete removal of the applied pressure. This pressure is called holding, dwell, packing, or the second stage pressure. After the second part of the process is finished, the injection unit can be reprimed to prepare for the next shot.
Controlling the movement of the screw and changing each of the following variables in a combination appropriate for the machine allows for metering control of the molten resin throughout the entirety of the injection cycle.
Leia também: 8 Métodos de manutenção para aumentar a vida útil da cavidade do molde
The amount of pressure given to the screw; the amount of time allowed for movement; the pace of movement; and the ability to control where the screw is positioned.
Injection profiling is a term commonly used to utilize all the factors above together during the holding/injection process.
Potential Challenges Arising from an Inadequately Maintained Injection Unit:
A defective or unmaintained injection unit in an injection molding machine can lead to various issues that can affect the quality of the molded parts and the machine’s overall performance. Here are some common problems that can arise:
1. Inconsistent Melting and Mixing:
A poorly maintained or defective injection unit can result in inconsistent melting and mixing of the material plástico. This can lead to variations in the material properties and result in the uneven filling of the mold cavity, leading to defeitos such as short shots, marcas de afundamento, or inconsistent part dimensions.
2. Injection Pressure and Speed Issues:
Problems with the injection unit can cause issues controlling the injection pressure and speed. If the pressure is too low, it may result in incomplete mold filling or inadequate packing of the material. Conversely, excessive pressure can cause overpacking, flash, or even damage to the mold. Inconsistent injection speed can lead to variations in part dimensions and surface defects.
3. Poor Plasticizing:
The plasticizing process in the injection unit involves melting and homogenizing the plastic material. A defective or poorly maintained injection unit may struggle to achieve proper plasticization, resulting in inadequate melting or poor material mixing. This can lead to variations in material properties, reduced strength, or inconsistent appearance of the molded parts.
4. Material Degradation:
Inadequate maintenance of the injection unit, such as insufficient purging or cleaning, can lead to material degradation. Residual material from previous runs can mix with the new material, resulting in impurities, color variations, or reduced material properties. Material degradation can negatively impact part quality and cause production delays.
5. Leakage and Nozzle Issues:
A defective injection unit may experience leaks or nozzle-related problems. Leakage can lead to material loss, contamination, and inconsistent filling of the mold. Nozzle issues, such as clogging or poor alignment, can result in the improper flow of the molten plastic and cause defects like flow marks, jetting, or hesitation marks on the parts.
6. Temperature Control Problems:
The injection unit relies on precise temperature control for optimal material flow and consistency. Temperature fluctuations can occur if the heating or cooling systems malfunction or are improperly maintained. This can lead to issues like material degradation, variations in part dimensions, or inconsistent acabamento da superfície.
7. Reduced Productivity and Increased Downtime:
A defective or unmaintained injection unit can result in increased downtime due to frequent machine breakdowns, mold damage, or the need for constant adjustments. This leads to reduced productivity and increased production costs.
Conclusão:
In the end, the injection unit plays a substantial role in processing an injection molding machine and producing plastic products. And if the injection unit is not used properly or maintained after frequent use, it can lead to various manufacturing issues.
Regular maintenance, inspection, and calibration of the injection unit are crucial to mitigate these issues. Furthermore, adequate training for operators and technicians, along with adherence to maintenance schedules and recommended procedures, can help prevent many of these problems and ensure the smooth operation of the injection molding machine.
For more details and queries, contact our professionals at Prototool.com.
Leia também: 11 produtos muito utilizados atualmente fabricados por moldagem por injeção