Today, several molding processes are known for mass-producing everyday goods. However, still, some parts and pieces in numerous industries need to be more intricate to be manufactured using standard plastic injection molds. Such production needs are fulfilled using a technique known as high-precision plastic injection molding.
This efficient injection molding approach is a highly specialized technique involving precise molds. And what makes it more effective and accessible to fulfill various modern-day plastic goods production demands is that it is not utilized to create entire goods but rather to create more complicated plastic parts.
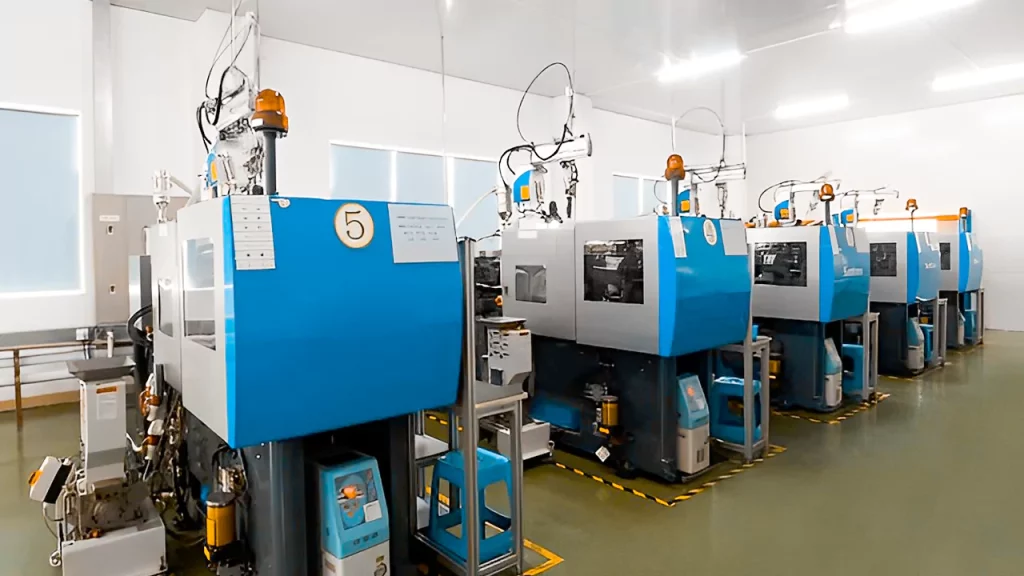
Hence, high-precision plastic injection molding differs from convective modeling in various aspects, including the materials utilized, the mold made, and the machine used to create the product. This article will discuss everything about high-precision plastic injection molding – from its definition to method, what makes it different from other production methods, and its advantages.
So keep reading to learn about this advanced and reliable injection molding solution.
High-Precision Plastic Injection Molding – Overview:
In simple terms, high-precision plastic injection molding is a type of injection molding that needs extreme precision. It is often employed when a project demands a precise form of plastic injection molding rather than making a whole product. Precision plastic parts are frequently utilized to replace high-precision metal parts in instruments, electronics, optics, medical equipment, and other applications.
Moreover, precision injection molding necessitates a precision mold and precise machinery due to these requirements. Precision molding is a complex procedure.
The Method:
Every piece created in a high-precision plastic injection molding project must be identifiable because it will be joined similarly. As a result, the high-precision plastic injection molding process can be slow, steady, and precise. This is a method that is individual to each project. A precision-molded part’s success depends on everything from the tooling to the part design, material selection, and procedures.
The high-precision plastic injection molding machine must be able to manage the product’s accuracy and repeatability. This machine should be subjected to high pressure to increase the overall precision and quality of the parts. The machine should have a rigid clamping system with a control range of 0.05 to 0.08mm, dimensional accuracy of parts, die speed, plasticizing parts such as the screw, screw head, material barrel, check ring, and more.
5 Key Properties of High Precision Plastic Injection Molding:
Due to the complexities, you can handle the high-precision plastic injection molding process during production; this process introduces unique properties and solutions for plastic product manufacturers. Five such vital properties include:
It Requires the Use of Polymer Optics:
Polymer optics are utilized in the process of accurate injection molding. In this process stage, CNC machining is utilized to shape the plastics in a calculated and precise manner. The high pressure of the machines contributes to an improvement in both the quality and the precision of the plastic components. They are also capable of producing correct products consistently.
An automatic handling system and computers are used throughout the process, which has been completely automated. It allows the manufacturer to tailor the molding process to the specific product that needs to be shaped.
Because of this, the labor cost is decreased, while the automated process contributes to increased production efficiency.
It Makes Precise Plastic Component Production Easier:
When compared to the process of plastic injection molding, this technique yields more exact plastic components than the former does. It does not engage in the bulk production of whole parts. These finished items, made as a byproduct of the process, are intended to replace high-precision metal components found in various industrial appliances.
Tolerances need to be extremely precise for precision injection molding to produce accurate plastic components. It denotes that the techniques outlined in the requirements for the product are concrete and precise. When the instructions are not followed, it can cause the mold to break.
The precise injection molding used in product production ensures the product has intricate geometric components. These things require specific shapes for medical, IT, pharmaceutical, and automotive goods.
It Introduces Low Shrinkage Capacity for Plastic Products:
High-precision plastic injection molding can cause the plastics being used in the manufacturing process to shrink. Hence this technique requires a material shrinkage capacity that is low. Because of this, the materials it uses are distinct from those used in other types of injection molding.
Since substances have a high potential for retração, they are more likely to melt during injection molding, which is entirely accurate. In the end, it makes the product unusable. Hence, for this molding process to be successful, the materials that are employed need to have a limited capacity for shrinkage. The required amount of shrinkage is around +/-0.01″ or +/-0.02″. However, this range is out of reach for many different materials.
1 this description is ABS, which is a thermoplastic polymer. This particular type of plastic can keep its suppleness even after being subjected to extreme temperatures. Despite this, the material’s shrinkage of +/-0.06 millimeters does not make it suitable for precision molding. It is possible to get the desired shrinkage by adding glass and other types of resin. They contribute to the material’s capacity to absorb excess heat while maintaining the plastic’s consistency.
Its Mold Is the Most Important Instrument for Ensuring High-Precision Manufacturing:
The mold used in this molding technique allows for a high level of precision produced. It must fulfill the requirements of design engineering.
It must first go through the proper investigation, design, and testing processes to successfully build the mold. For the mold, there are a lot of different factors that need to be considered. The following are some of the components that require special attention:
- The size of the mold cavity, as well as its position and the number of cavities it contains
- The precision of the parting surface
- The materials used for the mold (which can be made from steel alloys or cast irons)
- The thickness of the bottom plate
- The size of the runner
- The mold’s bottom plate thickness
- The mold’s runner size
- The mold’s bottom plate thickness is determined by several factors, including:
Depending on the model, tolerance for precision injection models ranges from +/-0.02 inches to +/-0.01 inches or less. Each of the factors above is considered when determining the dimension’s tolerance.
It is a Manufacturing Method That Is Both Slow and Consistent:
A model with high accuracy is required to manufacture plastic components with precise tolerances. Every single member molded using a specific injection model must be identical. This method can only be utilized for plastic parts positioned and joined with other plastic components in a predetermined configuration.
Because of the precise nature of the items, the maker must avoid relying on quick tools while utilizing this approach. The process of explicit injection modeling is slow and steady, resulting in an instrument with high precision.
Advantages of High Precision Plastic Injection Molding:
Below are some common benefits when opting for high-precision plastic injection molding as your go-to manufacturing solution.
Cost-Effective Manufacturing Approach:
High-precision plastic injection molding offers several benefits over traditional manufacturing processes, including improved cost-effectiveness. The fact that it is an efficient use of resources is among the most significant benefits provided by this method. Because the procedure does not require additional tooling or machining, the associated expenses are minimized to a bare minimum. Furthermore, the system takes just a reasonable amount of time, which allows for the production of components in a timely and effective manner.
Producing Parts with a High Level of Detail and Accuracy:
Another advantage of high-precision plastic injection molding is that it can make components with a high level of detail and accuracy. These parts can be exact. This is a result of the nature of the procedure, which is exceptionally accurate and precise. Because of this, it is ideally suited for manufacturing components with delicate details and complex shapes. Also, the procedure can be used to manufacture pieces with a smooth surface, improving the product’s overall look and feel. This is one more way in which the product can be improved.
Time-Saving Manufacturing Solution:
Last but not least, high-precision plastic injection molding manufacturing is high-speed. This results in the faster and more effective production of individual components, shortening the time necessary to create a finished good. Because of this, it is an excellent option for running large-scale production runs, as it enables the rapid and effective manufacture of individual parts.
Conclusão:
Now that you understand what high-precision plastic injection molding is and how to practice this practical production approach, you can ensure that your company’s/brand’s plastic product’s production is more detailed, cost-effective, time-saving, and of a higher quality.
Still have questions? Contact us at Prototool – we’re always here to help you out!